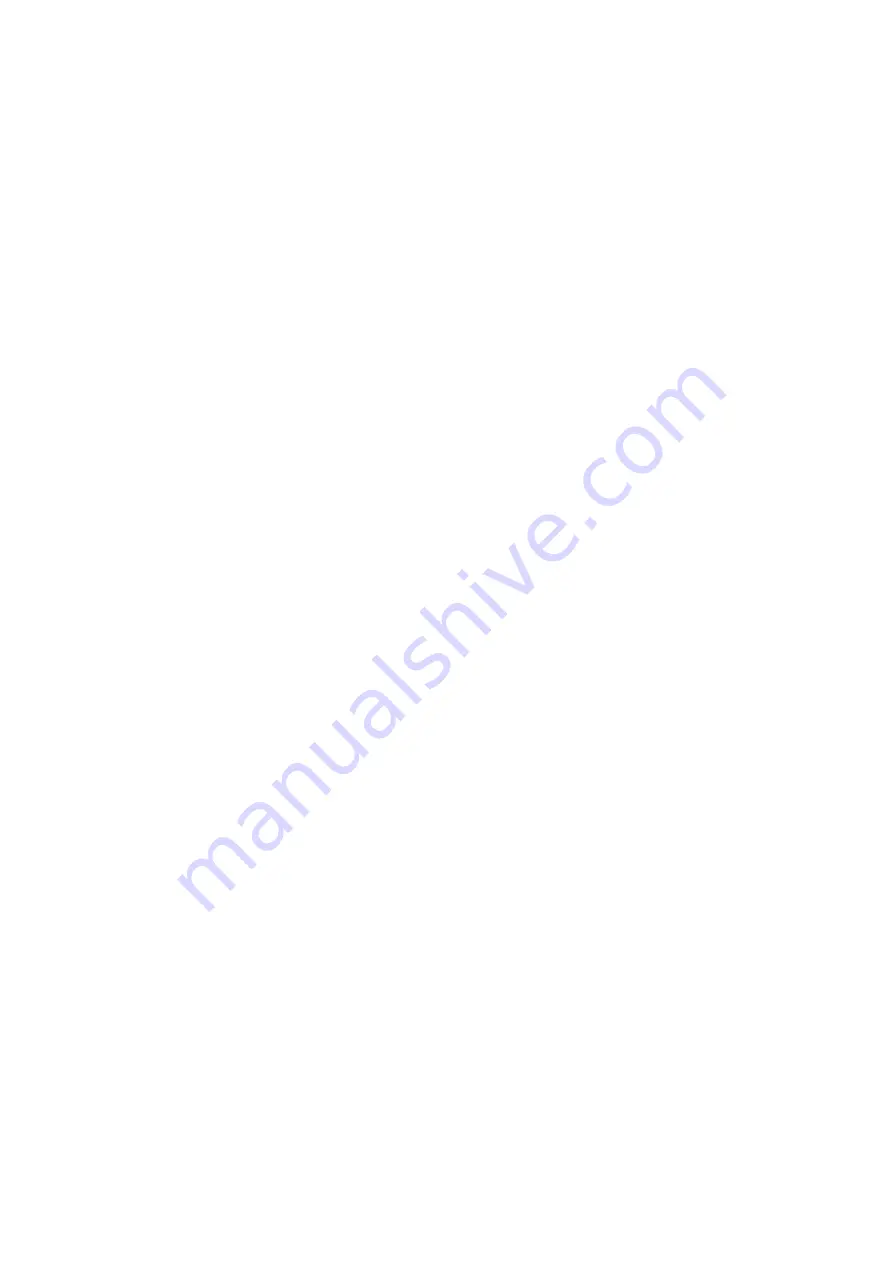
flags commence to move, then screw
anti-clockwise until it remains steady,
which is normally around the 10mmwg
(0.4
”
wg) mark. Setting higher than
0.5mbar (0.2
”
w.g) with the indicator
flag bouncing will give rise to nuisance
lockouts. Setting around 0.175mbar
(0.07
”
w.g) or less may not lockout the
heater in the event of air failure.
Ensure gas valve motor rotational
switch to L (normal position). Reset
active duct sensor temperature set
point to 40
˚
C adjust the minimum
settings to 25
˚
C.
Tamper sealings
On completition of commissioning all
adjustable setting are to sealed with
suitable evident seal.
Safety checks
With the burner firing, close burner
isolating valve V6, lockout will occur.
Open valve and reset lockout
condition.
Remove the air sensing tube from the
bottom connection of the air pressure
switch. The heater will lockout.
Replace and reset. Adjust overheat
controller set point down until heater
shuts off on overheat. Reset
temperature to 85
˚
C for the DV range
and 75
˚
C for the DH range. Reset by
depressing the red button on the
Honeywell overheat thermostat.
Particular attention should be given to
the adequacy of the air supply.
Commissioning procedure
Ambi-Stat controllers
To be read in conjunction with the
schematic wiring diagram, and
process diagram. Commissioning of
Nordair heaters should be carried out
by competent engineers. Training
courses are available at Nordair works.
Externally positioned heaters should
not be commissioned during adverse
weather conditions i.e. during rain and
high winds etc...
Each heater is fully tested for safety
checks and operational sequence,
prior to delivery, but requires the
following inspection to be carried out
PRIOR TO commencing
commissioning.
All manual gas valves are closed.
All electrical supplies are isolated.
Electrical earth continuity between the
heaters, gas pipework and main
electrical supply.
Gas installation pipework has been
tested for soundness.
Gas installation has been purged.
Note and record fan motor data badge
details.
Note and record fan and motor pulley
sizes, belt reference and pulley
centres.
Fan belt tension and alignment.
Check overheat controller setting is
85
˚
C.
Pre firing commissioning
Ensure all MCB’s in control panel are
in the OFF position.
Set motor overload to the motor plate
FLC. For direct on line motors, and
60% of the motor FLC for star delta
motors.
Set the discharge head vertical
distribution blades to give maximum
spread, and the horizontal blades
slightly upwards, to prevent downward
air movement. Discharge heads
fitted with Novo-Jet nozzles should be
twisted to give maximum spread with
no downward air movement.
Switch on electrical supply to heater,
check voltage across each phase for
415 volts, and down to neutral for 240
Volts.
Switch on the 240 and 24 volt control
circuit breakers.
Adjust the room thermostat on the
Ambi-Stat to minimum, override the
time clock to the OFF position.
Switch the fan motor circuit breaker to
the ‘ON’ position. Switch the
Heat/Vent switch to the vent position.
Override the time clock and the air fan
will start up. Check fan rotation is
correct if not isolate the electrical
supply and change two of the phases
over. Switch on the electrical supply
and check isolation is correct.
Measure and record the motor FLC
over each phase. Measure and record
the air velocity over the burner profile
opening. Reading should be between
14-16 m/sec adjust profile opening if
required. Measure and record final
profile opening.
Connect a suitable manometer to the
pressure tapping point P5 upstream of
the motorised gas valve. Open burner
isolating valve V6 and record the gas
line suction pressure. Close V6 on
completion.
Check within the factory area that no
air movement can be felt at low level,
adjust horizontal blades in distribution
head or Nova-Jet nozzles if necessary.
Check gas soundness of the gas
control train by following the procedure
leak testing the gas line at the end of
the commissioning and testing section.
Содержание DH2 150
Страница 16: ...Layout of electrical equipment DV heater Layout of electrical equipment DH heater...
Страница 25: ......