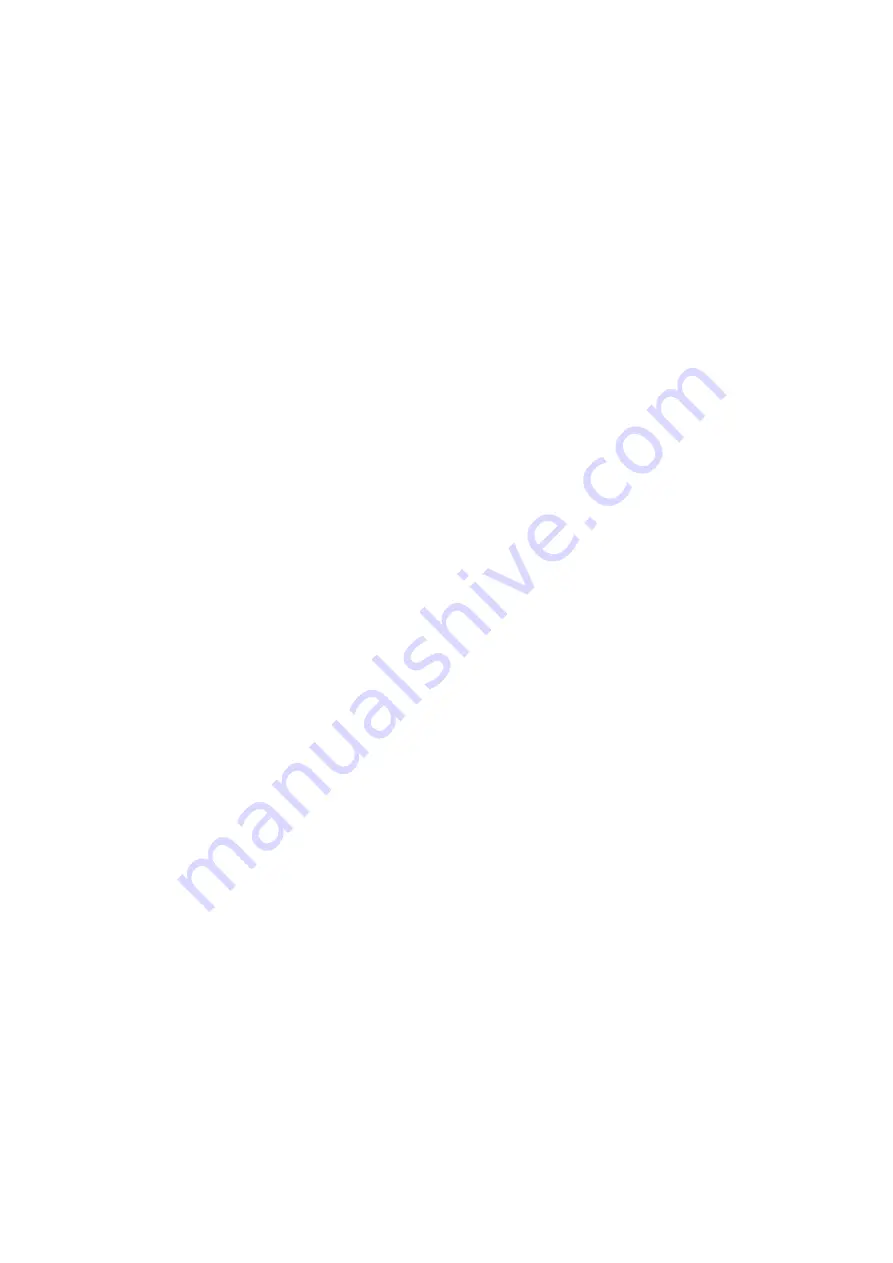
Leak testing the gas line
The procedure should be used in
conjunction with the Process and
Instrumentation drawing.
1. Ensure that gas and electricity
supplies are turned off and close
manual valves V1, V6, V7 and V11.
Testing the pipework up to and
including the upstream main safety
shut-off valves.
2. Connect a suitable pressure gauge
to pressure test point P2.
3. Open V1 to pressurise the governor
assembly.
4. Close V1. Leave the system for 3
minutes and watch for a fall in
pipework pressure. If the pressure
falls open V1, and test for leaks
with a soap solution. Make good as
necessary and re-check.
Note 3 minutes should be allowed for
all pressure checks.
5. If no external leaks are observed,
the upstream main safety shut-off
valve is passing gas.
To check this, replace the sealing
screw on the pressure test point 2,
and connect the pressure gauge.
To test point 4 and leave for 3
minutes with V1 still open. A rise in
pressure will confirm main valve is
passing gas. Replace the valve and
re-check for soundness.
Testing the downstream main safety
shut off valve.
6. Close V1 and connect pressure test
points P1 and P4 with a length of |
rubber tubing.
7. Open V1 to pressurise the assembly
upto the burner isolating valve, V6.
8. Using a leak detection solution
check all joints downstream of the
second safety shut off valve up to
V6. If leaks are detected close V1
and remake leaking joints. Repeat
7 and 8 to re-check after assembly.
9. If no external leaks are observed,
close V1 and connect rubber tube
to pressure test point P1 and P3
to pressurise the assembly between
the two safety shut off valves.
Connect pressure gauge to
pressure test point P4.
10.Open V1, any rise in pressure
indicates the downstream safety
shut off valve is passing gas.
Replace valve and re-check for
soundness.
Testing the start gas pipework
11.Connect pressure gauge to P2 and
open V7 and V1 to pressurise the
start gas line up to the first gas
safety shut-off valve.
12.Close V1. Leave the systems for 3
minutes and watch the pressure
gauge. If the pressure falls, open
V1 and soap test the start gas
pipework and re-test.
13.If no external leaks are evident the
start gas safety shut-off valve is
passing gas.
To check this, replace the sealing
screw on the pressure test point P2
and connect the pressure gauge to test
point P6 and leave for three minutes
with V1 still open. A rise in pressure
confirms the upstream pilot valve is
passing gas. Replace valve and re-
check for soundness.
Testing the downstream pilot safety
shut off valve
14.Close V1 and V11, connect
pressure test points P1 and P7.
15.Open V1 to pressurise the
assembly up to the isolating valve,
V11.
16.Using a leak detection solution,
check all joints downstream of the
second safety shut off valve up to
V11. If leaks are detected close
V11 any remake leaking joints.
Repeat 15 and 16 to re-check after
re-assembly.
17.If no external leaks are observed,
close V1 and connect rubber tube
to pressure test point P1 and P6 to
pressurise the assembly between
the two safety shut off valves.
Connect pressure gauge to
pressure test point P7.
18.Open V1, and rise in pressure
indicates the downstream safety
shut off valve is passing gas.
Replace valve and re-check for
soundness.
Содержание DH2 150
Страница 16: ...Layout of electrical equipment DV heater Layout of electrical equipment DH heater...
Страница 25: ......