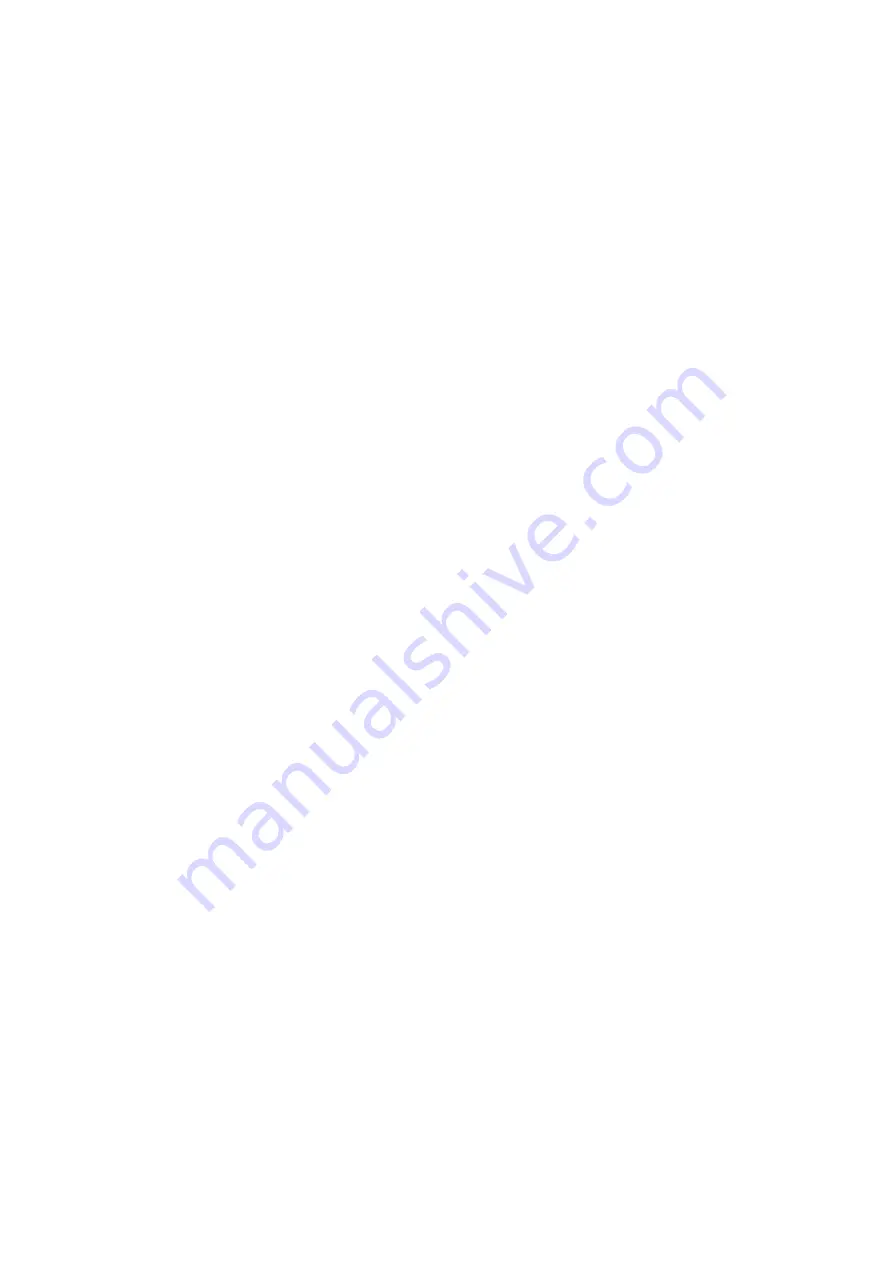
To be read in conjunction with the
schematic wiring diagram and the
process diagram.
Commissioning settings are to be
recorded on the enclosed sheets, a
copy of which is to be returned to
Nordair.
Override the time clock to a ON
position adjust room thermostat to
maximum setting.
The flame programmer will commence
a 40 second air purge followed by
ignition and lockout.
Open main gas isolating valve V1, and
pilot isolating valves V7 and V11.
Ensure burner isolating valve V6 is
closed.
Connect a suitable manometer to
pressure tapping point P7.
Depress the lockout-reset button on
the front of the Satronic Flame
Programmer. A 40 second air purge
will commence, followed by pilot
ignition and lockout. Check pilot gas
pressure and reset governor, if
necessary to 5mbar (2
”
wg). Additional
lockout resets may be required to
adjust pilot governor pressure due to
the time allowed prior to lockout
occurring.
Remove the cover from the active duct
sensor situated in the discharge
ducting/distribution head to reveal a set
point and proportional band adjusters.
The active duct sensor transmits a
0-10 VDC output signal to drive the
gas control valve motor.
Adjust temperature set point to
maximum adjustment.
Open burner gas isolating valve V6
and reset the lockout condition. A 40
second purge will commence followed
by pilot ignition and main flame ignition.
Within 3 seconds of main flame ignition
the gas valve will commence driving to
the full open position. Whilst driving
the flame colour should be blue with a
maximum flame length of 250-300mm
(10
”
-12
”
) extending from the burner
plates. If flame lengths in excess of
250-300mm (10
”
-12
”
) occur, or orange
in colour, close burner isolating valve
V6, until the correct length/colour is
obtained.
Connect a manometer to pressure
tapping point P1. Measure and record
the main gas inlet pressure, which
should be in the range of 19.8-45mbar
(7.5
”
wg-18
”
wg).
Connect a manometer to pressure
tapping point P3 and measure
governor outlet pressure, which should
be approximately 9.5mbar (3.8
”
wg). If
valve V6 had to be closed reduce
governor outlet pressure and fully open
valve V6.
To increase or decrease the gas supply
pressure to the burner, turn clockwise
to increase the governor outlet
pressure, and anti-clockwise to reduce
outlet pressure. It is strongly
recommended that a pressure gauge is
connected to pressure point P3 when
adjusting governor outlet pressure.
Note DO NOT adjust governor
pressure when setting low fire gas
pressure.
If increasing the governor outlet gas
pressure does not increase the burner
pressure at high fire, then the gas
control valve requires resetting.
Connect a separate manometer to
pressure tapping point P5 and P9
measure the pressure. The differential
gas pressure which should be 5.0mbar
(2.0
”
wg). If the differential pressure is
lower than 5.0mbar (2.0
”
wg) increase
governor outlet pressure until this
differential pressure is obtained. If the
differential is higher than 5.0mbar
(2.0
”
wg) lower the governor outlet
pressure, note and record governor
outlet pressure.
As a cross check at high fire, measure
the outside air temperature and deduct
from the duct discharge temperature,
this should be 42
˚
C.
Reset the Belimo gas control valve
motor directional switch between L/R.
The gas control valve will commence to
drive to the minimum position.
The flame at low fire should be a small
continuous blue flame, along the full
length of the burner, with a
temperature rise of 5
˚
C maximum over
the outside air temperature. The low
fire valve setting may have to be
adjusted to obtain this temperature rise
if the main gas governor outlet
pressure was increased to obtain high
fire setting.
To adjust the low setting, slacken the
M6 nuts from the motor ‘U’ clamp
around the valve spindle and with a
pair of grips on the valve spindle
minutely close to the valve in small
stages until the 5
˚
C temperature rise is
obtained. With great care, tighten the
‘U’ clamp onto the valve spindle,
ensuring that the shaft does not move.
Override the gas valve motor to high
fire and then back to low fire to ensure
the low fire setting has not altered, by
switching the directional switch
between L & R.
The high fire stop has been factory set
to ensure the valve opens fully, and
should not require adjusting.
To ensure that the burner ignites
smoothly and consistently at low fire.
Repeat this 4/5 times to ensure trouble
free ignition.
With burner firing at minimum rate
connect both ends of a manometer to
the tapping points on the pressure
switch sensing tubes, to measure and
record the differential air pressure
across the profile plate at full fresh air.
Reading should be between 1 to
1.5mbar (0.4-0.6wg
”
).
Adjust air pressure switch by inserting
a screw driving into the slotted
adjusting screw. Screwing clockwise,
increases the pressure range. Anti-
clockwise reduces the pressure range.
The ideal setting is to screw clockwise
until the flags commence to move,
then screw anti-clockwise until it
remains steady, which is normally
around the 10mm wg (0.4
”
w.g) mark.
Setting higher than 10mm wg (0.4
”
w.g)
with the indicator flag bouncing will
give rise to nuisance lockouts. Setting
around 0.175mbar (0.07
”
w.g) or less
may not lockout the heater in the event
of air failure.
Burner commissioning
Ambi-Stat controllers
Содержание DH2 150
Страница 16: ...Layout of electrical equipment DV heater Layout of electrical equipment DH heater...
Страница 25: ......