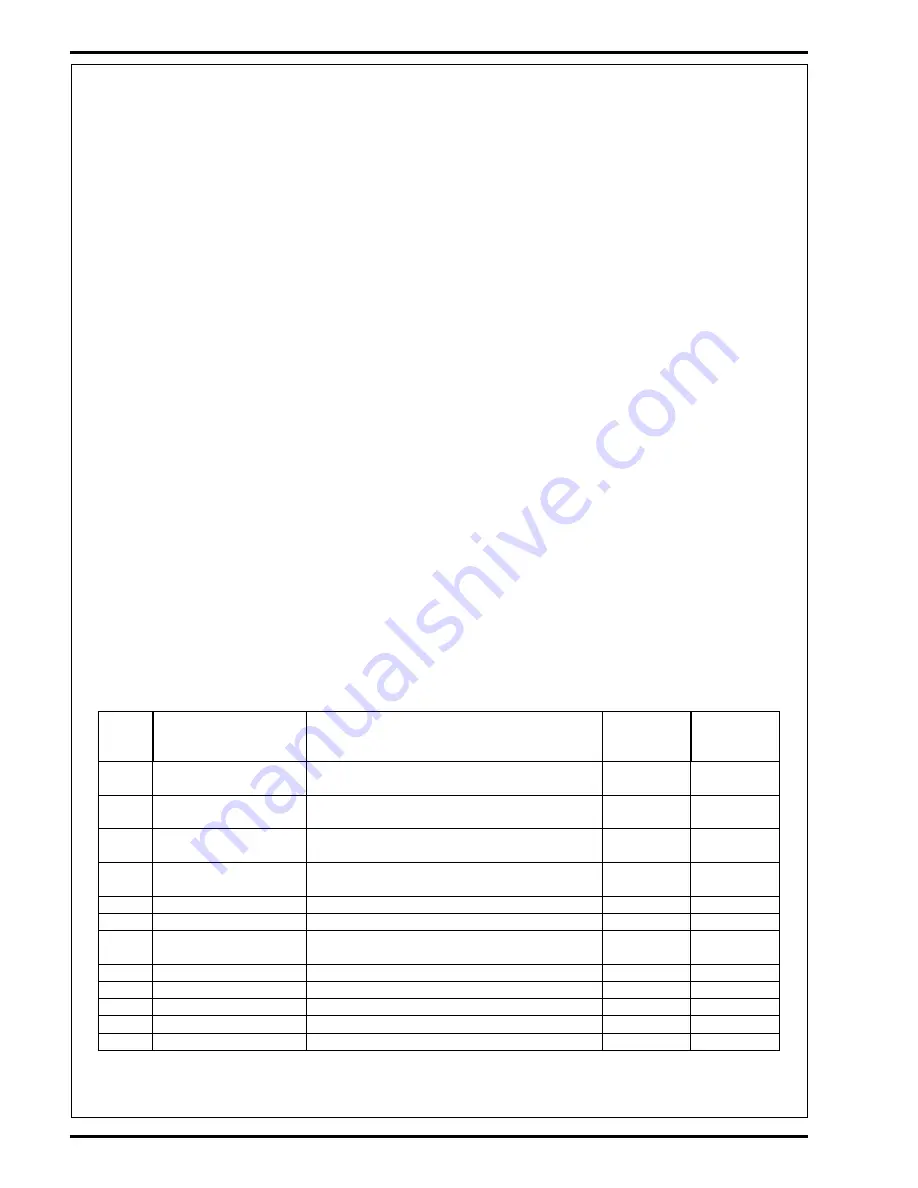
18
18
18
18
18 - FORM NO. 56043089 / AquaRide
™
/ BRX 700
WHEEL DRIVE SYSTEM
WHEEL DRIVE SYSTEM
WHEEL DRIVE SYSTEM
WHEEL DRIVE SYSTEM
WHEEL DRIVE SYSTEM
TABLE #1
Value
Curtis Display Callout
Description
Factory
Programmed
Values
Approximate
Travel Speed
3.0 sec
ACCEL MAX SPEED
Acceleration rate [time to go from stop to maximum
speed in seconds
1, 2
3.0 sec
ACCEL MIN SPEED
Acceleration rate [time to go from stop to maximum
speed in seconds]
3, 4
3.0 sec
REVERSE ACCEL MAX
Reverse acceleration rate [time to go from stop to
maximum speed in seconds]
1, 2
3.0 sec
REVERSE ACCEL MIN
Reverse acceleration rate [time to go from stop to
maximum speed in seconds]
3, 4
100%
M1 MAX SPEED
Transport speed maximum limit [% of full throttle]
1
4.2 MPH
40
%
M2 MAX SPEED
Fast maintenance mode speed limit [% of full throttle]
2
1.
4
MPH
24%
M1 MIN SPEED
Maintenance/fast restore mode speed limit [% of full
throttle]
3 .8
MPH
17%
M2 MIN SPEED
Restore mode speed limit [% of full throttle]
4
.5 MPH
70%
M1 REVERSE MAX SPEED
Reverse speed maximum limit [% of full throttle]
1
30%
M2 REVERSE MAX SPEED
Reverse speed maximum limit [% of full throttle
2
24% REVERSE
MIN
SPEED
Reverse speed maximum limit [% of full throttle]
3, 4
OFF
THROTTLE AUTOCAL
Used for calibration of the throttle assembly
GENERAL FUNCTIONAL OVERVIEW
GENERAL FUNCTIONAL OVERVIEW
GENERAL FUNCTIONAL OVERVIEW
GENERAL FUNCTIONAL OVERVIEW
GENERAL FUNCTIONAL OVERVIEW
See Figures 1 & 2. An 840-watt 1.1 HP (permanent magnet) 36V motor/gear transmission combination wheel unit (M3) is used to propel
all machines. A Curtis model 1228 PMC solid state speed controller (A1) regulates (outputs) the variable speed Fwd/Rev wheel drive
motor functions. The controller unit is located to the left of the operator seat, behind the electrical access panel. The potentiometer
R1 mounted to the operator’s foot pedal, inputs to the (A1) controller the machine operator’s desired speed and directional demands.
DRIVE MOTOR SYSTEM CONTROLLER FUNCTION OVERVIEW
DRIVE MOTOR SYSTEM CONTROLLER FUNCTION OVERVIEW
DRIVE MOTOR SYSTEM CONTROLLER FUNCTION OVERVIEW
DRIVE MOTOR SYSTEM CONTROLLER FUNCTION OVERVIEW
DRIVE MOTOR SYSTEM CONTROLLER FUNCTION OVERVIEW
See Figure 2. To make the A1 speed controllers internal control circuits operational (power it up) the two switches S1 (key) and S2
(seat) must be closed. This circuit inputs a positive (+) 36V to the A1 speed controls pin terminal #5 (*KSI). The F2 circuit breaker 45
Amp supplies the positive high current (load) circuit input to the B+ controller terminal (Brn/Blk wire). The black wire from the
negative (-) battery standoff supplies the battery ground input to the B- terminal for both the control and load circuits.
See Figure 3. Depressing the foot pedal in either Fwd or Rev will move the 5K Ohm (R1) potentiometer shaft off its centered balanced
(neutral) setting of approximately 2500 Ohms. With this pot shaft movement the pot’s resistance value changes which generates a
variable voltage signal (0-5 volts). These control board voltage input signals are what energizes the Fwd & Rev directional relays,
which selects the motor polarity and what also manages switches the battery voltage On and Off (**PWM) that varies the motor
speed.
*KSI: Key Switch Input
**PWM: Pulse Width Modulation, also called “chopping” is a technique that switches battery voltage to the motor ON and OFF very
quickly, thereby controlling the speed of the motor.
DRIVE MODE SELECTION OPERA
DRIVE MODE SELECTION OPERA
DRIVE MODE SELECTION OPERA
DRIVE MODE SELECTION OPERA
DRIVE MODE SELECTION OPERATION OVERVIEW
TION OVERVIEW
TION OVERVIEW
TION OVERVIEW
TION OVERVIEW
The following is a list of the speed control parameters that can be adjusted using a Curtis hand held programmer:
There are four programmable speed limits on the AquaRide. These are transport speed, fast maintenance speed, maintnance/fast
restore speed, and restore speed. For the maintenance and restore modes, the fast speed is selected by pressing the speed select
speed select
speed select
speed select
speed select
switch*
switch*
switch*
switch*
switch* on the control panel.
For reference purposes, the speed control parameters below are followed by a number from 1 to 4. These are used to indicate which
parameters apply to which operating mode of the machine.
(1) Transport mode [fastest] (scrub system off)
(2) Fast Maintenance Mode (maintenance mode, speed select indicator = on)
(3) Maintenance/Fast Restore Mode (maintenace mode, speed select indicator = off
OR restore mode, speed select
indicator = on)
(4) Restore Mode [slowest] (restore mode, speed select indicator = off)
*Speed Select Switch:
*Speed Select Switch:
*Speed Select Switch:
*Speed Select Switch:
*Speed Select Switch: This switch will allow the operator to select a faster travel speed while the scrub system is enabled thereby
allowing extracting at a higher rate of speed. The speed select indicator will be green if a scrub mode has been selected and the
faster scrub speed has been selected. It will be off otherwise.