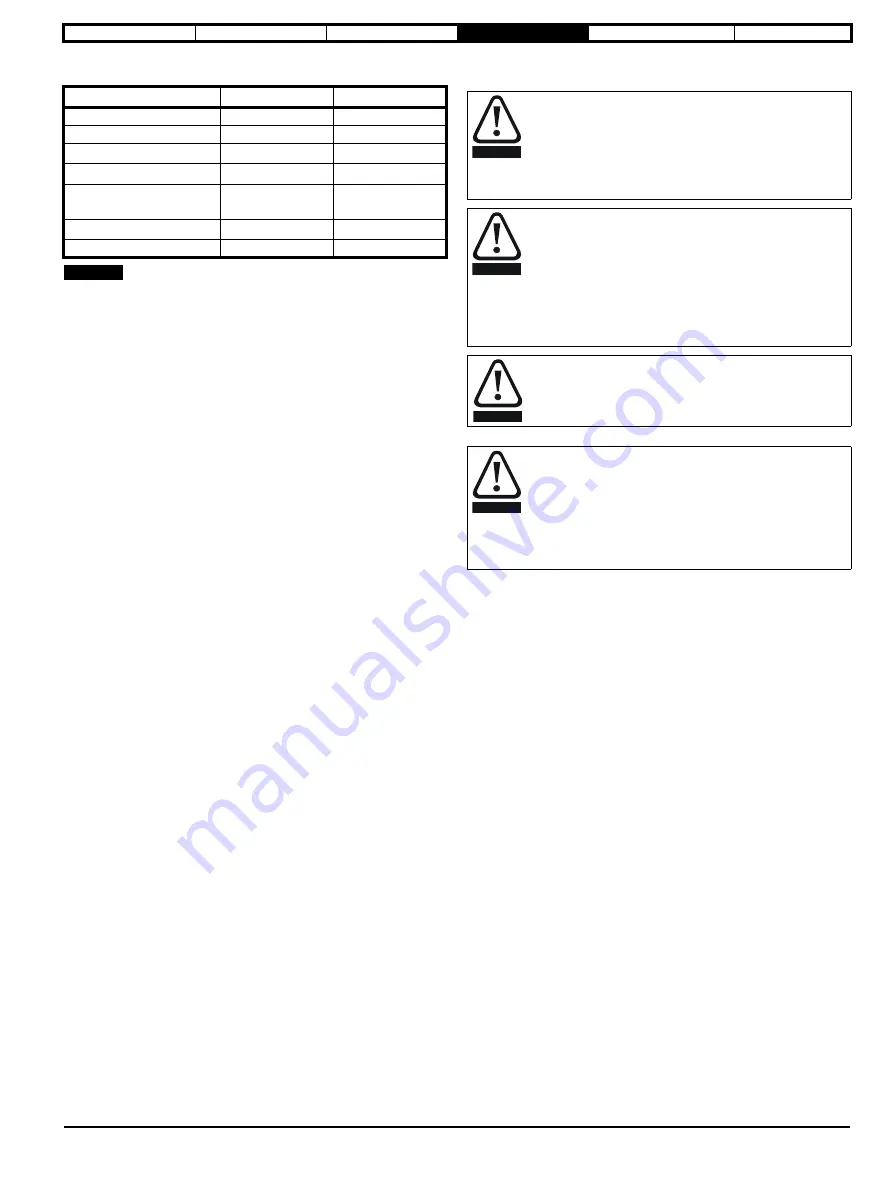
Digitax HD M75X Series Installation and Technical Guide
83
Issue Number: 5
According to EN ISO 13849-1
Logic levels comply with IEC 61131-2:2007 for type 1 digital inputs rated
at 24 V. Maximum level for logic low to achieve SIL3 and PL e 5 V and
0.5mA.
Two-channel Safe Torque Off
Models Digitax HD M75X have dual channel STO.
The dual channel STO has two fully independent channels.
Each input meets the requirements of the standards as defined above.
If either or both inputs are set at a logic low state, there are no single
faults in the drive which can permit the motor to be driven.
It is not necessary to use both channels to meet the requirements of the
standards. The purpose of the two channels is to allow connection to
machine safety systems where two channels are required, and to
facilitate protection against wiring faults.
For example, if each channel is connected to a safety-related digital
output of a safety related controller, computer or PLC, then on detection
of a fault in one output the drive can still be disabled safely through the
other output.
Under these conditions, there are no single wiring faults which can
cause a loss of the safety function, i.e. inadvertent enabling of the drive.
In the event that the two-channel operation is not required, the two
inputs can be connected together to form a single Safe Torque Off input.
One-channel Safe Torque Off (Including Two- channel Safe Torque
off with the inputs connected together.)
In a single channel Safe torque Off application there are no single faults
in the drive which can permit the motor to be driven. Therefore it is not
necessary to have a second channel to interrupt the power connection,
nor a fault detection circuit.
It is important to note that a single short-circuit from the Safe Torque Off
input to a DC supply of > 5V could cause the drive to be enabled.
This might occur through a fault in the wiring. This can be excluded
according to EN ISO 13849-2 by the use of protected wiring. The wiring
can be protected by either of the following methods:
• By placing the wiring in a segregated cable duct or other enclosure.
Or
• By providing the wiring with a grounded (0V of the Drive) shield in a
positive-logic grounded control circuit. The shield is provided to avoid a
hazard from an electrical fault. It may be grounded by any convenient
method; no special EMC precautions are required.
Note on response time of Safe Torque Off, and use with safety
controllers with self-testing outputs:
Safe Torque Off has been designed to have a response time of greater
than 1 ms so that it is compatible with safety controllers whose outputs
are subject to a dynamic test with a pulse width not exceeding 1 ms.
Safe Torque Off over-ride
The drive does not provide any facility to over-ride the Safe Torque Off
function, for example for maintenance purposes.
Lift (Elevator) Applications
The Safe Torque Off function is suitable for use as a safety component
in lift (elevator) applications:
The Safe Torque Off function can be used to eliminate electro-
mechanical contactors, including special safety contactors, which would
otherwise be required for safety applications.
For further information, contact the supplier of the drive.
Type
Value
Classification
Category
4
Performance Level (PL)
e
MTTF
D
(STO1)
>2500 years
High
MTTF
D
(STO2)
>2500 years
High
MTTF
D
(Single channel
STO)
>2500 years
High
DC
avg
≥
99 %
High
Mission time
20 years
NOTE
The design of safety-related control systems must only be
done by personnel with the required training and experience.
The Safe Torque Off function will only ensure the safety of a
machine if it is correctly incorporated into a complete safety
system. The system must be subject to a risk assessment to
confirm that the residual risk of an unsafe event is at an
acceptable level for the application.
Safe Torque Off inhibits the operation of the drive, this
includes inhibiting braking. If the drive is required to provide
both braking and Safe Torque Off in the same operation (e.g.
for emergency stop) then a safety timer relay or similar device
must be used to ensure that the drive is disabled a suitable
time after braking. The braking function in the drive is
provided by an electronic circuit which is not fail-safe. If
braking is a safety requirement, it must be supplemented by
an independent fail-safe braking mechanism.
Safe Torque Off does not provide electrical isolation.
The supply to the drive must be disconnected by an approved
isolation device before gaining access to power connections.
It is essential to observe the maximum permitted voltage of
5 V for a safe low (disabled) state of Safe Torque Off. The
connections to the drive must be arranged so that voltage
drops in the 0V wiring cannot exceed this value under any
loading condition. It is strongly recommended that the Safe
Torque Off circuit be provided with a dedicated 0V conductor
which should be connected to either terminals 1, 3, 4, 5, 7 or
15 at the drive.
WARNING
WARNING
WARNING
WARNING
Содержание Digitax HD M75 Series
Страница 115: ......
Страница 116: ...0478 0395 05...