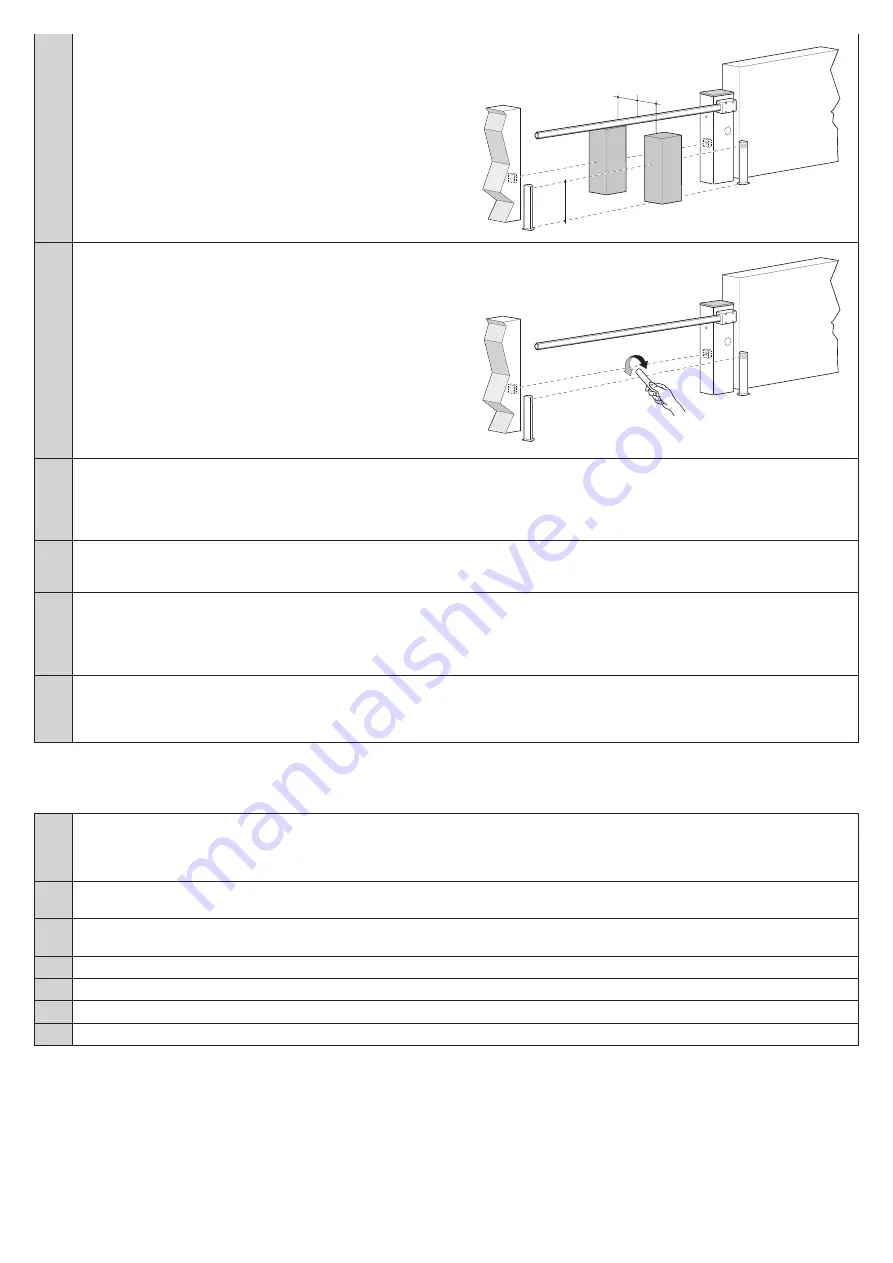
English –
22
If the test is on two pairs of photocells, the test must first be per-
formed individually for each pair of photocells using 1 testing block
and then repeated using 2 testing blocks.
Every testing block must be positioned laterally in relation to the
centre of the boom, at a distance of 15 cm and then moved along
the entire length of the boom.
During these tests, the testing block must be detected by the pho-
tocells at any position along the entire length of the boom.
300
200
700
500
300
200
700
300
200
700
500
150
150
07.
a - Check that there is no interference between the photocells and
other devices:
- interrupt the optical axis linking the pair of photocells using a
cylinder (
diameter
of 5 cm and length of 30 cm)
- pass the cylinder first close to the TX photocell, then close to the
RX and lastly at the centre between the two photocells.
b - Check that the device intervenes in all cases, going from active
status to alarm status and vice versa
c - Check that it causes the intended action in the control unit (e.g.
a reverse movement during the closing manoeuvre).
300
200
700
500
300
200
700
300
200
700
500
150
150
08.
Check on the safeguard against the lifting hazard: in automations with vertical movement you must ensure that there is no lifting hazard.
Run the test as follows:
- at a point half-way along the boom, hang a weight of 20 kg (e.g. a sack of gravel)
- send an Opening command and check that during the manoeuvre the boom does not exceed the height of 50 cm above its closed
position. If the boom exceeds this height it is necessary to reduce the working force by using the FL trimmer (Section 7.1).
09.
If the dangerous situations caused by the movement of the boom have been safeguarded by limiting the force of impact (step 8), the
impact force must be measured according to EN Standard 12445 and, if the control of the “motor force” is used to assist the system
for the reduction of the impact force, it is necessary to experiment and, in the end, find the adjustment that provides the best results.
10.
Check the efficiency of the manual release system:
a - place the boom in its closed position and perform the manual release of the gearmotor, making sure that it takes place with ease
b - check that the manual force for moving the boom to the Open position does not exceed 200 N (approximately 20 kg); the force is
measured perpendicular to the boom and at 1 m from the axis of rotation
c - check that the manual release key is available near the automation.
11.
Check the power supply disconnection system:
a - operate the power disconnection device and disconnect any available back-up batteries
b - check that all the LEDs on the control unit are OFF and that the boom remains still when a command is sent
c - check the efficiency of the manual locking system to prevent any unintentional or unauthorised reconnection
6.2 - Commissioning
Commissioning can take place only after all testing phases have been terminated successfully (par. 6.1).
Partial or “makeshift” commissioning is strictly prohibited.
01.
Prepare and store the technical documentation for the automation for at least 10 years. This must include at least: an assembly drawing
of the automation, a wiring diagram, an analysis of hazards and solutions adopted, a manufacturer’s declaration of conformity of all the
devices installed (use the annexed CE declaration of conformity); a copy of the automation system instruction manual and maintenance
schedule
02.
Affix a label or plate permanently to the barrier mechanism, bearing instructions on how to manually release the gearmotor: use the
figures included at the end of the User Manual (removable insert)
03.
Using the key switch or radio transmitter, test the Opening and Closing of the barrier mechanism and make sure that it moves in the
intended direction
04.
Prepare the CE declaration of conformity for the automation system and deliver it to the owner
05.
Give the owner the user manual (tearout insert)
06.
Prepare and give the owner the maintenance schedule
07.
Before commissioning the gate, inform the owner in writing about the attendant residual risks.
Содержание WIDEL
Страница 13: ...English 11 WIDE M WIDE M a b c d e f l 90 i h g...
Страница 32: ......
Страница 34: ......