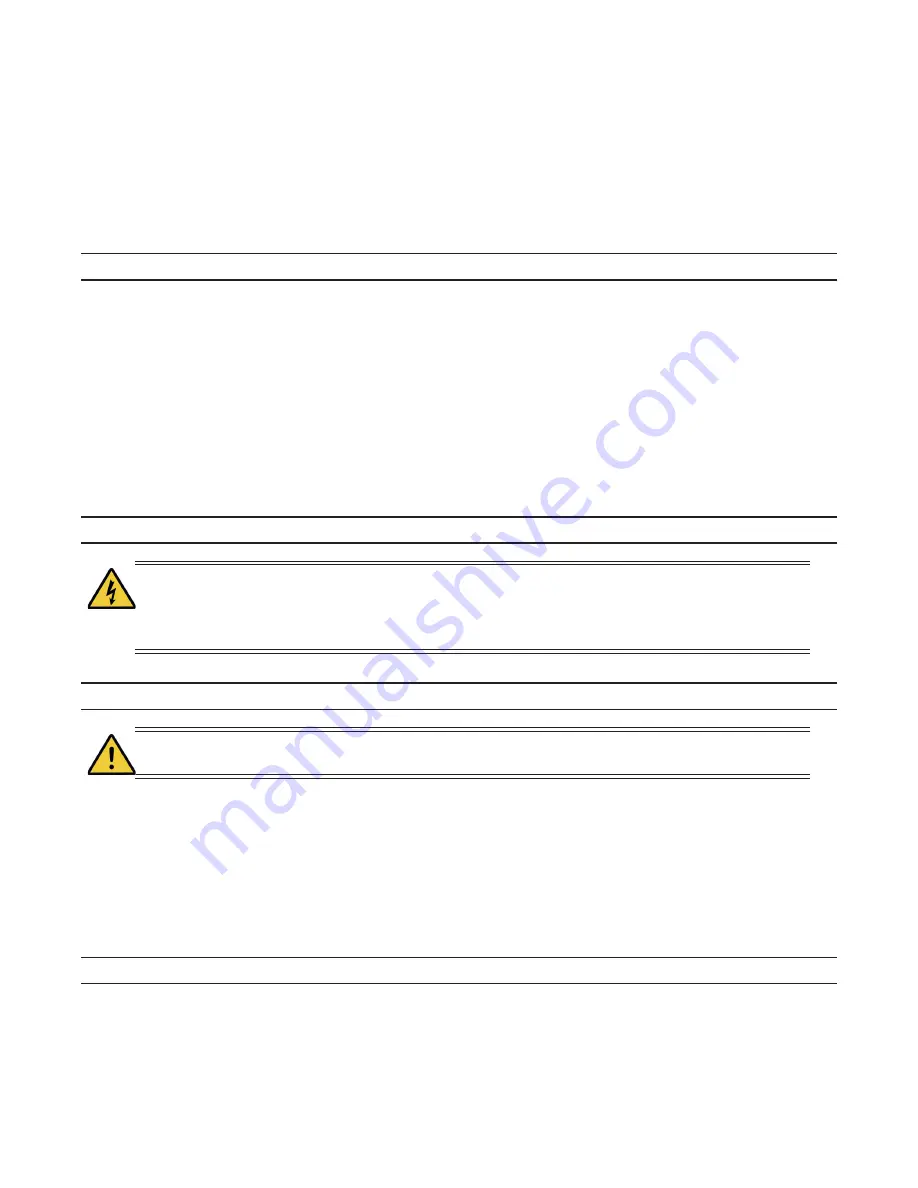
5
If safety devices need to be dismantled during setup, maintenance, or repair work, they must be
reinstalled and inspected immediately after completion of the service or repair work.
Make sure that materials and replacement parts are disposed of safely and in an environmentally-
friendly manner.
Make sure that electrical components used for replacement purpose comply with the original parts
and are correctly adjusted if necessary.
2.6
Safety Off Position
The safety off position is the position of the machine when it cannot generate any hazard.
How to put machine in safety off position:
• Turn off the grinder.
• Turn off the dust collector.
• Wait for all drives to stop.
• Pull out main plugs.
• Secure machine against unintended start-up.
2.7
Dangerous Aspects of the Machine
Every machine, if not used according to the regulations, may be hazardous for operating,
setup and service personnel. The operating authority is responsible for compliance with
the safety regulations during operation and maintenance of safety devices supplied with the
machine, as well as the provision of additional safety devices.
2.8
Electrical Engineering Regulations
The machine must only be started when all guards and dust collection parts are attached
and machine is standing flat on work surface.
If work on electrified parts is necessary, a second person must be deployed who can pull out the
plug in an emergency. The working area must be sealed with a red and white safety chain and a
danger sign. Use tools that are insulated against voltages.
Only start work once familiar with the electrical engineering regulations that apply to the area.
Only use voltage testers that comply with the regulations when troubleshooting. From time to time,
check voltage tester to ensure it is operationally efficient.
2.9
Special Instructions
Use proper tools for work. Damaged tools must be repaired or replaced immediately.
Use the required safety equipment and safety clothes (e.g. safety glasses, safety shoes, safety
gloves).