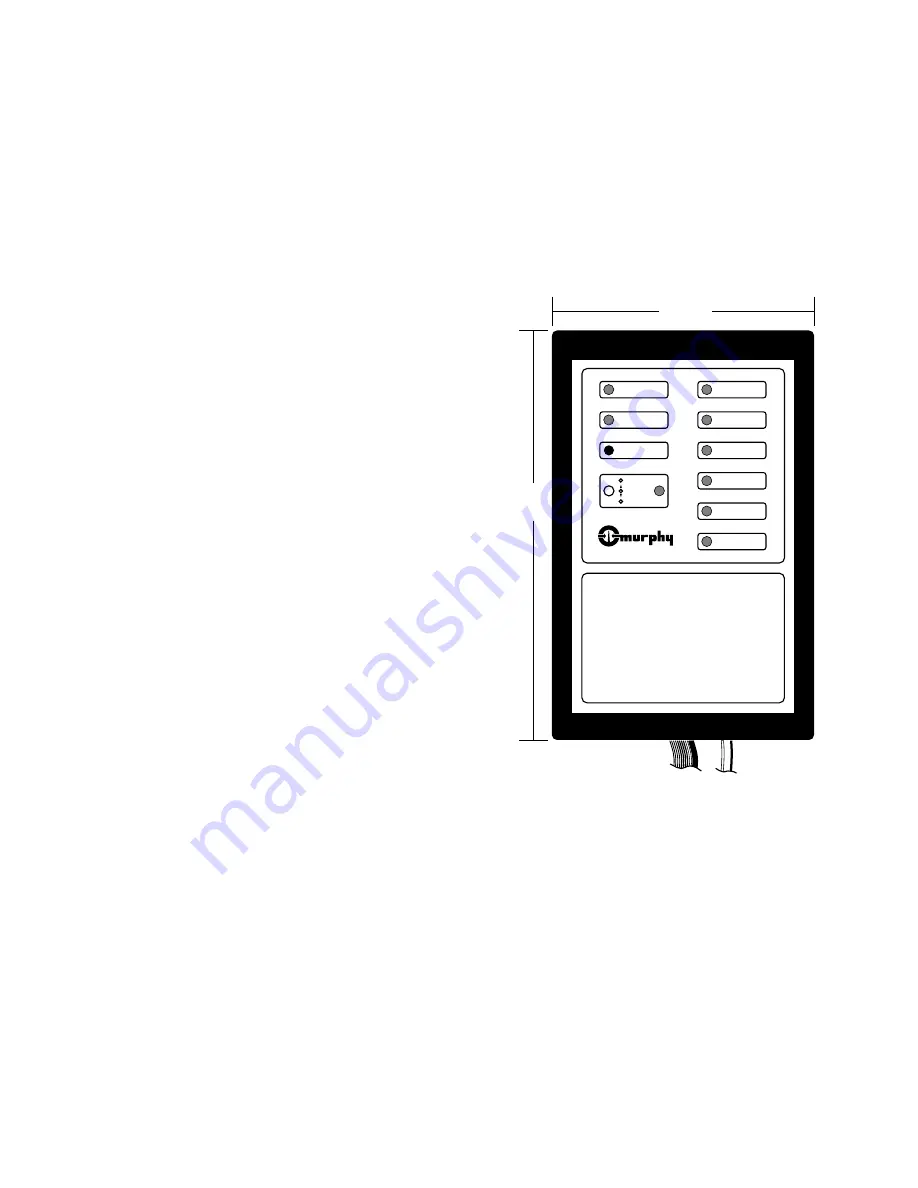
7
to operate a local audible alarm as required by NFPA- 110,
Level 1 and Level 2.
3-3.2.5 Remote Audible Alarm Relay; provides a contact
closure to operate a remote audible alarm as required by NFPA-
110, Level 1.
3-3.2.6 Remote Visual Alarm Relay; provides a contact closure
to operate a remote visual alarm as required by NFPA- 110,
Level 1.
3-3.3 Status Signals. The relay module also includes three
outputs that can be used with external circuits for signaling or
control functions.
3-3.3.1 The Control On function at terminal 12 is on (closed
to negative) as long as the Mode Selector Switch is in either
Auto or Test. When the Mode Selector is turned Off, the
Control On signal is open. This can be used to signal switch
position or to reset an external circuit when the Mode Selector
is turned Off.
3-3.3.2 The System Ready signal at terminal 13 is on (closed
to negative) as long as the Mode Selector Switch is in either
Auto or Test and no shutdown Tattletale circuit is latched on.
This can be used to signal that the generator engine is ready to
automatically start or is running in Test.
3-3.3.3 The Control On function at terminal 14 is on (closed
to positive) as long as the Mode Selector Switch is in either
Auto or Test. When the Mode Selector is turned Off, the
Control On signal is open. This can be used to signal switch
position or to reset an external circuit when the Mode Selector
is turned Off.
3-4 A902.
3-4.1 Control / Display Module. The Control / Display
Module, figure 3-4.1, includes the control and test switches, the
solid state logic elements, shutdown and alarm TATTLETALE
®
lights that make up the generator engine control for a four-cycle
engine.
3-4.1.1 Mode Selector Switch, OFF-AUTO-TEST:
(a) OFF; turns off the control system and resets any shutdown
circuits.
(b) AUTO; turns on the engine controls and shutdown
circuits. System is on standby waiting for a contact
closure to start engine.
(c) TEST; turns on the engine controls and shutdown circuits.
A start signal is applied to the automatic control and the
engine start sequence begins.
3-4.1.2 Lamp Test Pushbutton: Tests the lights on the A902
module.
3-4.1.3 The A902 SELECTRONIC
®
Control Module includes
the following engine control features:
(a) Cycle crank circuit; will crank the engine for 15 seconds
then rest for 15 seconds until the engine starts. The
crank/rest time is selectable for either 10, 15, 20, 25 or 30
seconds. If the engine false starts, goes above crank
disconnect speed then drops below that speed, the control
will rest for a fixed 10 second period before cranking
again.
(b) Crank Disconnect Speed Switch; this circuit detects
engine speed and terminates cranking when engine speed
rises above the speed switch setting. The speed switch is
adjustable, 25 Hz to 2000 Hz, and is factory set at 1180
Hz. This would be 600 RPM on an engine with 118 teeth
on the flywheel ring gear.
(c) Auxiliary Crank Disconnect Circuit; this circuit, required
by NFPA-110, is provided as a back up for the Crank
Disconnect Speed Switch. It is operated by an external
switch sensing either speed, generator voltage or some
other variable that could be used to terminate cranking.
Either circuit will disconnect the starter when the engine
starts.
(d) Overcrank circuit; will stop automatic cranking and
indicate overcrank if engine fails to start after 3 attempts.
The number of cranks are selectable for 1, 2, 3, 4 or 5
cycles before shutdown. The overcrank circuit may also
be turned off so no overcrank shutdown occurs.
(e) Shutdown Time Delay Bypass; this delay prevents the oil
pressure, water temperature and loss of speed signal
shutdown circuits from operating for 15 seconds after the
engine starts as detected by the crank disconnect circuit.
(f) Overspeed Speed Switch;
1. Provides a signal to the overspeed shutdown circuit if
the engine exceeds the preset speed. The factory
setting is approximately 3894 Hz, or 1980 RPM on an
engine with 118 teeth on the flywheel ring gear. The
adjustment range is 300 Hz to 10,000 Hz.
2. A push to test switch is provided to allow testing of the
overspeed circuit without overspeeding the engine.
When switch is depressed, the set point of the speed
switch is lowered approximately 10%.
3. The push to test switch can also be used to set the
overspeed switch at approximately 110% of running
speed. Hold the switch depressed while adjusting the
Low Water
Temperature
AUTO
OFF
TEST
Loss of Speed
Signal
Lamp Test
Water
Temperature
Oil Pressure
Overspeed
Overcrank
6-1/2 in.
(165 mm)
9-3/4 in.
(248 mm)
Figure 3-4.1