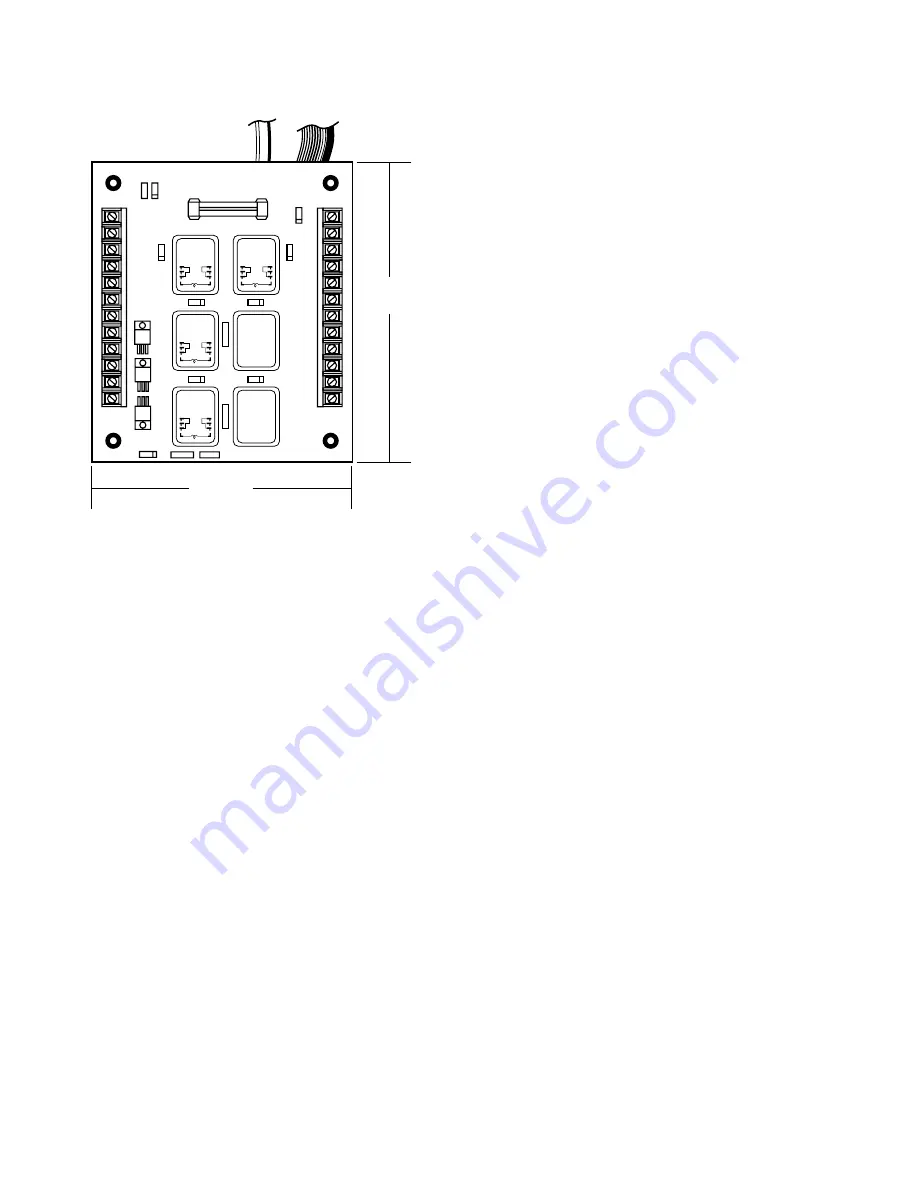
make up the generator engine control. Relays are available for
operation on either 12 or 24 volt battery systems. Four (4)
relays are included for:
3-7.2.1 Fuel Relay; this relay provides two outputs, one to
energize the engine fuel solenoid and a separate circuit to
energize the battery charging alternator field.
3-7.2.2 Shutdown Relay; this relay is operated by the shutdown
circuits of the Control / Display Module and provides an output
that can be used to trip the generator circuit breaker on an
emergency shutdown.
3-7.2.3 Overspeed Relay; operates only on an Overspeed
shutdown. This relay provides an output to trip an air shut off
solenoid to close the air damper on a two-cycle engine.
3-7.2.4 Local Audible Alarm Relay; provides a contact closure
to operate a local audible alarm as required by NFPA- 110, Level
1 and Level 2.
3-7.3 Status Signals. The relay module also includes three
outputs that can be used with external circuits for signaling or
control functions.
3-7.3.1 The Control On function at terminal 12 is on (closed to
negative) as long as the Mode Selector Switch is in either Auto
or Test. When the Mode Selector is turned Off, the Control On
signal is open. This can be used to signal switch position or to
reset an external circuit when the Mode Selector is turned Off.
3-7.3.2 The System Ready signal at terminal 13 is on (closed
to negative) as long as the Mode Selector Switch is in either
Auto or Test and no shutdown TATTLETALE
®
circuit is
latched on. This can be used to signal that the generator
engine is ready to automatically start or is running in Test.
3-7.3.3 The Control On function at terminal 14 is on (closed to
positive) as long as the Mode Selector Switch is in either Auto
or Test. When the Mode Selector is turned Off, the Control On
signal is open. This can be used to signal switch position or to
reset an external circuit when the Mode Selector is turned Off.
Section 4: Installation
4-1 Location.
4-1.1 The A900 series is designed to mount in a
MURPHYMATIC
®
Generator Control panel with the Control /
Display module on the front panel and the Relay module on the
inside bottom surface. Other types of installation is possible as
long as the relationship of the two modules are maintained.
4-1.2 Clearance for Installation and Service; The modules must
be accessible for wiring to the terminal blocks and adjustment of
the user controls on the back of the Control / Display module.
Figure 4-1.2 shows the mounting dimensions and the minimum
clearances recommended for installation.
4-1.3 Wiring Terminals; Terminal blocks are provided on both
sides of the Control / Display enclosure and the Relay Module.
Torque all terminal screws to 12 inch pound maximum.
4-2 Wiring.
4-2.1 After the A900 has been located and installed, the wiring
connections can be made. This work should be done with all
electrical power disconnected from the engine. BE SURE THAT
THE BATTERY IS DISCONNECTED.
4-2.2 All electrical installation work should be done in
accordance with the National Electrical Code, NFPA-70, and all
applicable local codes.
4-2.3 In general, the following connections will be made:
(a) Battery positive and negative. An 8 A fuse or circuit
breaker must be provided to protect powered relay contact
circuits.
(b) Engine run device, such as a fuel shutoff solenoid.
(c) Engine speed sensor, such as a magnetic pickup or the
tachometer output of a battery charging alternator.
(d) Auxiliary crank disconnect device, such as a voltage
sensing relay contact wired to the generator output.
(e) Engine starter circuit; an auxiliary starter solenoid is
required to handle most starter solenoid requirements.
(f) Remote start contact. This is normally from the automatic
transfer switch but other sources are possible.
(g) Alarm and shutdown sensing switches as required.
4-2.3.1 The complete wiring of a Model A901 control is shown
in figure 4-2.3.1. Provision is made in the A900 series to
operate remote lights for all of the alarm and shutdown circuits
however these circuits do not have to be wired for the A900 to
function. Alarm input switches are not required but the alarm
circuits will not work without them.
4-2.3.2 Figure 4-2.3.2 is for wiring of the A902 control. The
same provisions as for the A901 are made.
4-2.3.3 The A903 wiring is shown in figure 4-2.3.3.
4-2.3.4 Wire Termination; the terminal blocks that are supplied
requires that all wires be terminated with #6 stud size forked
spade solderless wire connectors or stripped and inserted under
the captive terminal plates. Torque all terminal screws to 12
inch pound maximum.
4-2.3.5 All inductive loads (relays-soleniods-coils-etc.) that are
connected to the A900 must have reverse diodes wired across
the coil to supress reverse voltage that is generated whenever the
inductive load is de-energized. This will protect the electronic
components in the A900 and should prevent operating
malfunction due to noise. The “rule of thumb” for sizing the
reverse diode is to use one with a PIV (Peak Inverse Voltage)
rating equal to the operating voltage, or at least 100 volts and a
14
DC12V
3A Fuse
1A
4
5
6
7
8
9
16
17
18
19
20
21
22
23
24
25
DC12V
DC12V
DC12V
6-1/4 in.
(159 mm)
4-1/2 in.
(114 mm)
Figure 3-7.2