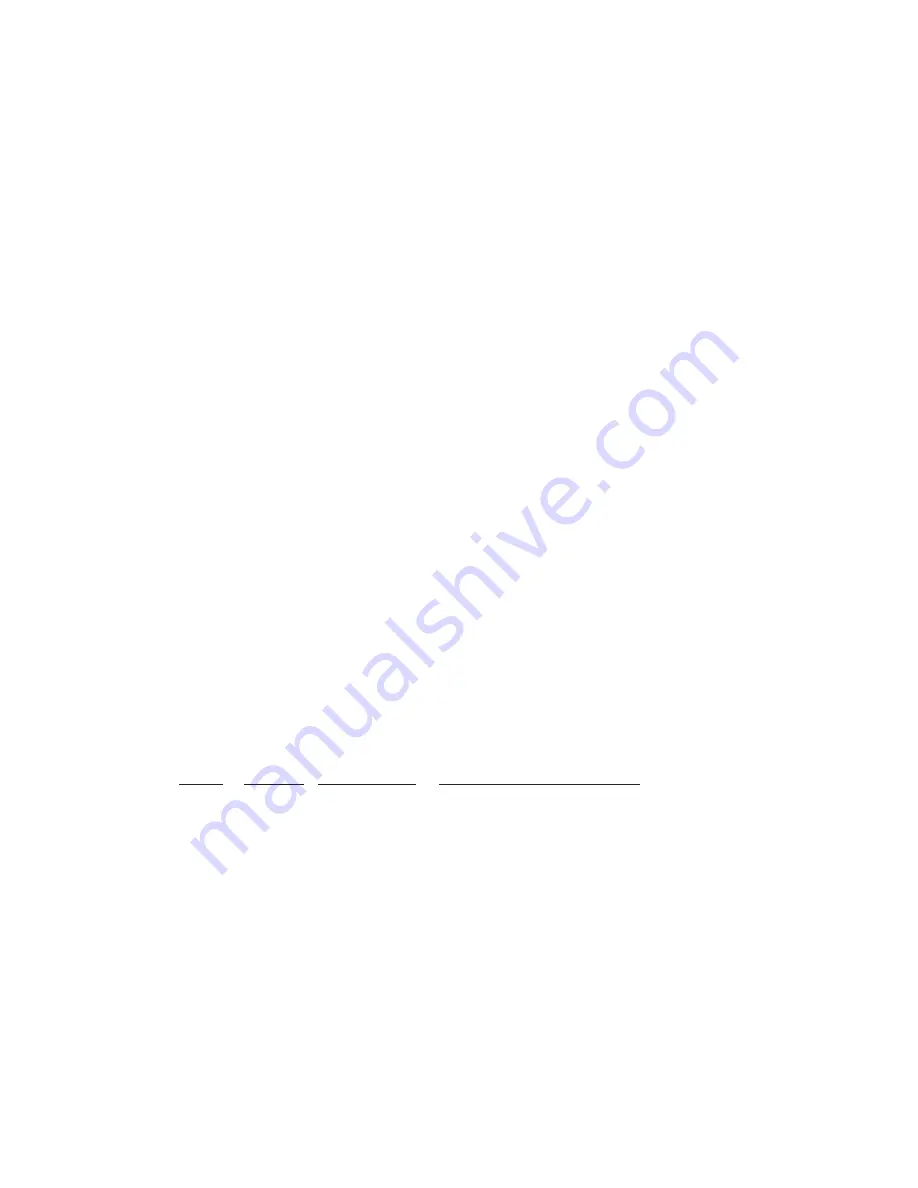
11.0 Strainer Cleaning
All ASPX modules have a 30-mesh filter strainer in the Chilled Water inlet header. The purpose for the filter strainer is to keep debris from entering the heat
exchanger. An external “Y” or basket type system strainer should also be installed as a pre-filter to the factory supplied strainers.
There is no set time for cleaning the filter strainers. The frequency of this process is dependant on the water quality in the Chilled Water loop. Normally, debris
in a water loop is going to take the path of least resistance and build up on the last modules to receive water.
If circuits are faulting on Low Suction Temperature, or Low Chilled Water Temperature the Chilled Water inlet filter cartridge should be checked. The strainers
are located in the top header on the Chilled Water side. If the strainers are clean, the fault is most likely being caused by a low flow condition--or set-points
in the master control that are too low. If these possibilities are eliminated, the Chilled Water heat exchangers may need cleaning.
Steps to remove the strainers for cleaning
1. Stop Chilled water pump and shut down chiller.
2. Close inlet and outlet water valves to the chilled water
3. Drain the water/glycol from the top header in the end module so the strainers can be removed.
4. Remove the 4-8” Victaulic end cap on last module.
5. Remove strainers and clean. You may need to make a tool to hook the other strainers for removal.
6. Re-install clean strainers.
7. Open the bottom water isolation valve and fill unit from the bottom up to prevent air from being trapped.
8. Restart Chilled Water pump, bleed any air and start Chiller.
12.0 Compressor Oil Level
Compressors used on ASPX modules are oil charged by the compressor manufacturer. The standard tandem Copeland compressors do have an oil equalizer
line and oil level sight glass indicator. Oil level should be maintained at 1⁄8 – ¼ full.
To ensure no liquid is present in the oil the crankcase heaters should be on 24 hours before starting of the compressors.
Factory oil charge volume for each compressor can be found in section 13.0.
13.0 Refrigerant Charge/Evacuation
All ASPX modules are factory charged with the recommended refrigerant volume. Prior to charging, each circuit is evacuated to a maximum of 150 microns
and held 15 minutes. The proper refrigerant charge for each module can be found on the module data plate.
On air-cooled packaged machines, the proper charging procedure is calculated by the weigh-in method. Charging to a full sight glass on air-cooled ma-
chines will likely result in over charging because the elbows in the liquid line, as well as the liquid line solenoid valve, still produce some flashing--even with
the correct charge. As fans are cycling, the sight glass will also display some bubbling.
Model #
Lbs. R410a Lbs. Low Ambient
Total Tandem Compressor Oil Charge
ASP10X
50
90
114
oz.
ASP15X
60
85
220
oz.
ASP20X
100
100
220
oz.
ASP30X
125
125
252
oz.
ASP60X
220
360
426
oz.
14.0 Filter Driers
ASPX Chiller modules have a liquid line filter drier installed. When doing a repair to the refrigerant side because of a compressor motor burn, or moisture
entering the system, a proper replacement drier should be installed.
15.0 Condenser Fan Control
10-, 15- and 20-ton modules can be ordered with standard pressure control cycling of fans or optional VFD control. ASP30 and ASP60 modules come standard
with VFD control.
16.0 Superheat/Subcooling
ASPX modules use a mechanical expansion valve. By turning the valve adjustment clockwise superheat is increased.
On each module, superheat is set at the factory during the run test. Superheat is set between 10 – 12°F during the test run.
Subcooling is necessary in the system to prevent flash gas when the refrigerant enters the expansion valve. ASPX condensers are sized so that subcooling of
the liquid refrigerant will take place without a separate subcooler. The general range of subcooling seen is 7- 15°F.