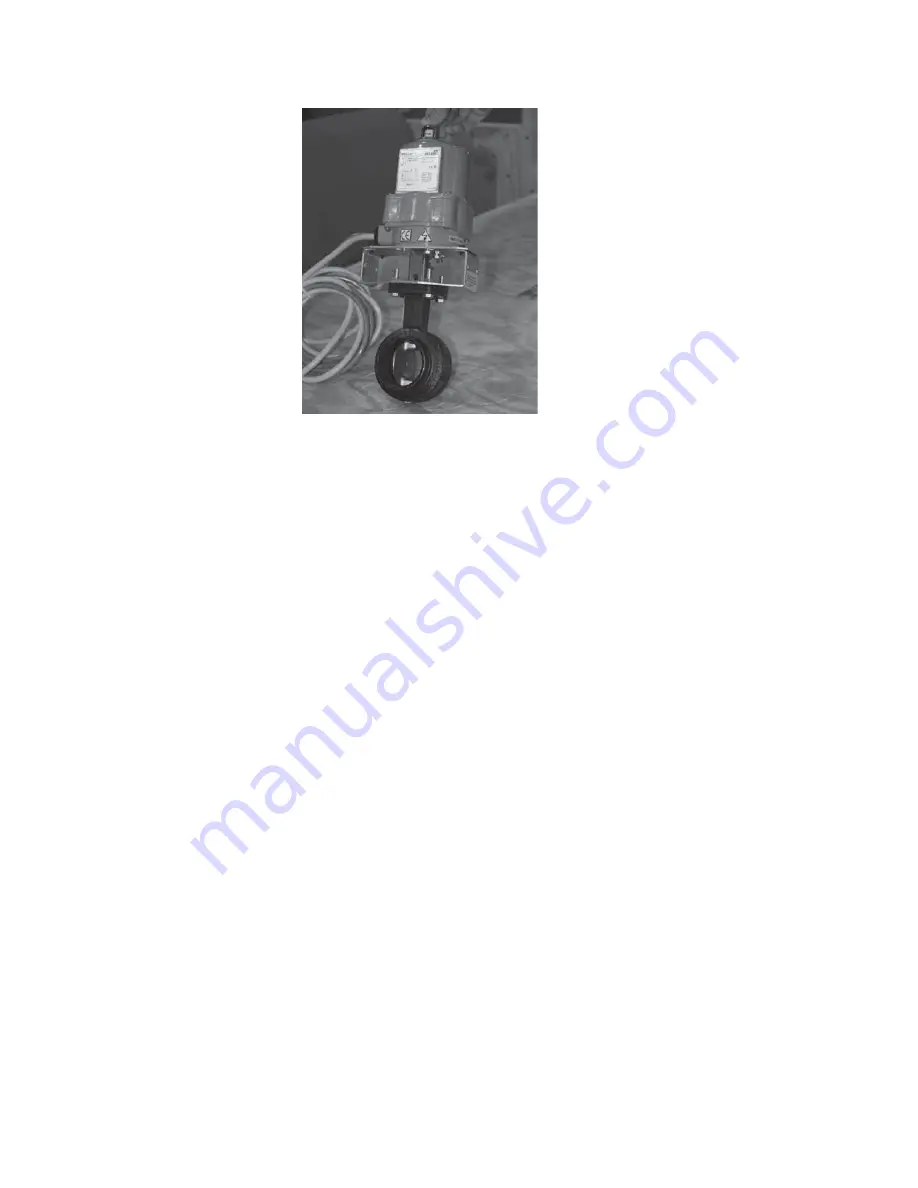
13
26.0 Optional Variable Flow CHW Valves
To accomplish variable flow on the chilled water side, modules must be special ordered with power actuated butterfly valves. In some configurations this
will change the footprint of the modules as valves will need to be installed between the heat exchanger and water header pipe of each module. The valves
on each module will open, close, and modulate as compressors cycle on or off. The valves allow flow to go through only modules that are running. Therefore
pressure drop increases as modules cycle off (closing valves) and allowing the pump to slow down to maintain constant pressure drop across the chiller.
Control of the variable speed pump needs to be taken from the pressure differential between the inlet and outlet of the chilled water at the chiller. Control
based off of system pressure will result in erratic temperature control as well as likely faults with operating modules. On the chilled water side a minimum
flow needs to be supplied to the chiller. In the factory setup menu of the master control you can select the number of valves to be open all of the time to
maintain a minimum flow. For further information on variable flow please see the Multistack Variable Flow Supplement.
The Variable Setpoint also works differently when doing variable flow. Since valves are used to isolate each heat exchanger, we do not need to account for
the mixing effect of modules that are running with modules in the off mode. On a normal application without water valves, if you have 10 compressors and
flow at a true 10°F Delta T with setpoints of 55 Up and 45 Lo and VSP at 50% your no load point would be 50°F. The last module running would be producing
water at 50° in and 40° out and mixing with those not ON producing the same temp as system entering (50°). The system LCHW temps would then range
between 45-50°F depending on the number of circuits ON and number OFF. With motorized butterfly valves on each module we do not have to take into
effect the mixed temperature as those heat exchangers are isolated. Since the CHW pump will be speeding up and down based on a constant chilled water DP
we should always be producing the same Delta T through modules as we are with the system temps. So if we kept the VSP at 50% the last module would be
on at 50°F entering water temp and producing both module and system leaving temp at 40°F. If we raise the VSP to 80% with the same 55° and 45° setpoints
the last module would be on at about 53.5° entering and then produce both module and system leaving temp at 43.5°. So basically when doing variable flow
a higher VSP is desired to maintain closer leaving water temps.
27.0 Optional Gear Driven Condenser Fan (low sound)
Service recommendations for ASP modules using the Right Angle Gear Drive for condenser fan motor. The gear drive has an oil level sight glass that should
be checked regularly. The model # 65 requires .50 gallons of ISO grade 220 synthetic oil (for applications from -20 – 150°F). Change the oil after 500 hours
of operation (break-in) then every 6 months or 2500 hours of operation which ever happens first. Since this gear box has only a small amount of oil, proper
oil change frequency is the key to longevity.