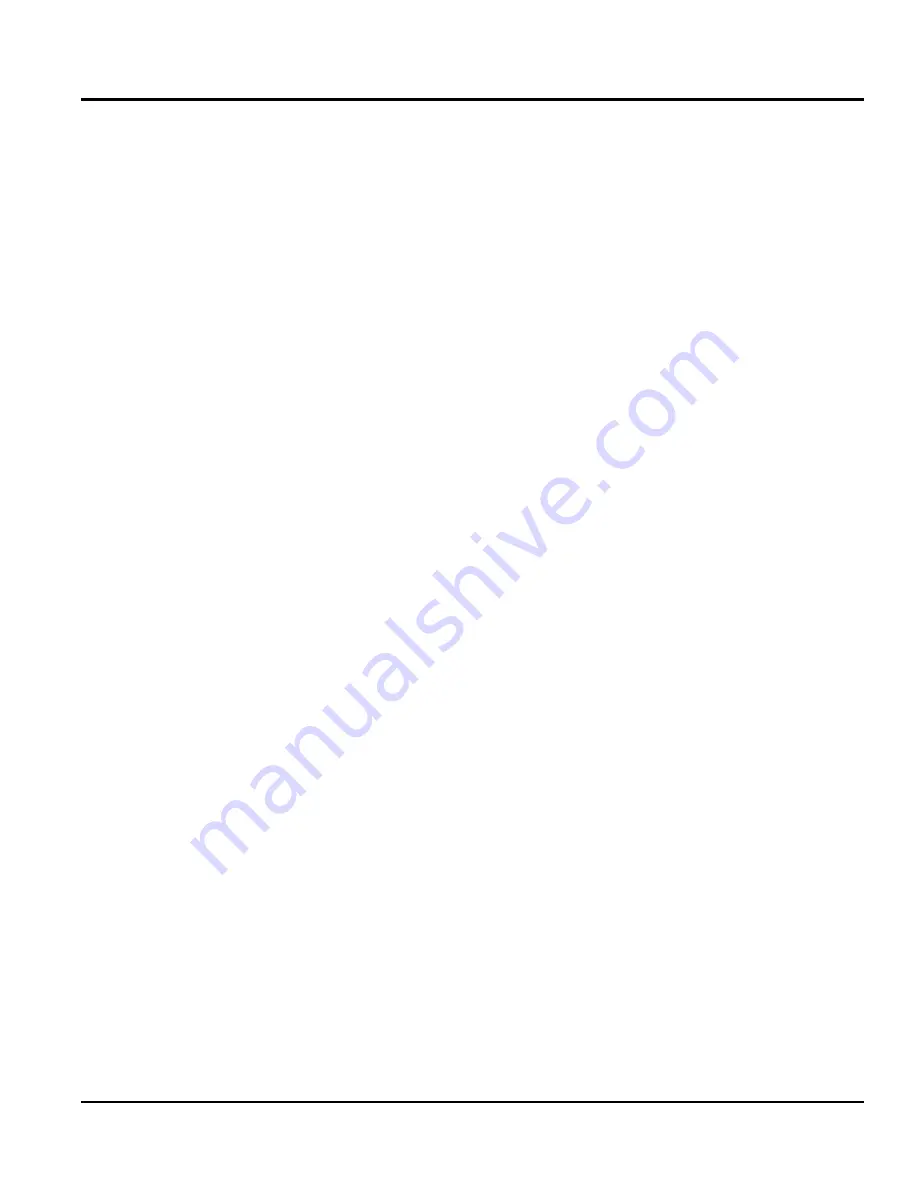
TB12SE/TB12PE TUFFTRUK POWER BUGGY• OPERATION MANUAL — REV. #0 (04/01/22) — PAGE 13
COMPONENTS
1.
Tub or Bucket
— Used for the transportation of
material. Tub holds approximately 12.0 cubic feet
(0.44 cubic yards) of water.
2.
Lifting Point
— Attach a suitable lifting strap to these
points when lifting of the buggy is required.
3.
Handle Bar (Steering)
— This handle bar is used to
steer the buggy. When steering the buggy, use both
hands and hold onto both handle bar grips.
4.
Deadman Control Lever
—
Red
handle lever, when
engaged (closed) allows the buggy to travel in either a
forward or reverse direction. Works in conjunction with
forward and reverse control levers. In addition, this lever
when engaged releases the brake.
5.
Forward/Reverse Speed Control Lever
— When fully
engaged, the buggy will travel at
FULL
speed in either
the forward or reverse direction. When released, the
buggy will
STOP
. This feature is only on the electric
models.
6.
Reverse Control Lever Signal Cable
— This lever/
cable is a 2-wire cable (switch) that when activated
sends a +12 VDC signal (J1-10) to the motor controller
indicating that the reverse travel function has been
selected.
7.
Battery Charger Cable
— Plug battery charger cable
plug into a 120 VAC power source.
8.
Tires
— Unit uses pneumatic tires. Reference
Table 1 for tire size.
9.
Tipping Bracket Pivot Bar
— Attach this bar to the
buggy frame to tip tub. Be sure to lock in place (locking
levers).
10.
Deadman Microswitch
— When activated sends a
+12 VDC signal (J1-3) to the motor controller to release
the brake. Microswitch is located inside handle.
11.
Dump Control Lever
— Push the lever forward to
place the tub in the dump position (vertical).
12.
Free-Wheel Brake Bypass Switch
— Momentary
toggle switch. Allows the buggy to be moved with the
electric motor brakes disengaged
13.
Battery/Diagnostic Gauge
— Uses a Curtis Model
3100R Gauge Display. Displays battery voltage and
fault codes. CAN bus compatible.
14.
Emergency Stop Switch
— In the event of an
emergency,
push
this button to shutdown the electric
motor.
15.
Electric Motor (Front)
— Uses a 24 VDC, 750 watt
electric motor.
16.
Electric Motor (Rear)
— Uses a 24 VDC, 750 watt
electric motor.
17.
Ignition/Key
— When activated allows the unit to be
started.
18.
Contactor
— Heavy duty relay used for the switching
of the ON and OFF +12 VDC power required for
the Curtis Model 1229 motor controller. Works in
conjunction with the contactor solenoid.
19.
Fuse Box
— Provides protection for various electrical
circuits. Reference wiring diagram in the manual.
20.
Contactor Fuse
— 100 amp fuse that provides
protection for the electric motor.
21.
Contactor Solenoid (Coil)
— When energized (coil),
12 VDC power to transfered to the Curtis Model
1229 motor controller via the K1-1and K1-2 contacts.
22.
5K OHM Potentiometer
— Provides signal for speed
sensor.
23.
Motor Speed Controller
— Unit uses a Curtis Model
1229 Controller. Requires a 24 VDC input. Interfaces
with CAN bus applications.
24.
Battery Charger (Electric)
— When activated, charges
both 12-volt batteries. This feature is only on the
TB11E
model.
25.
Battery
— Uses two 12 volt batteries connected in
series (24 volts). Always use gloves and eye protection
when handling the batteries.