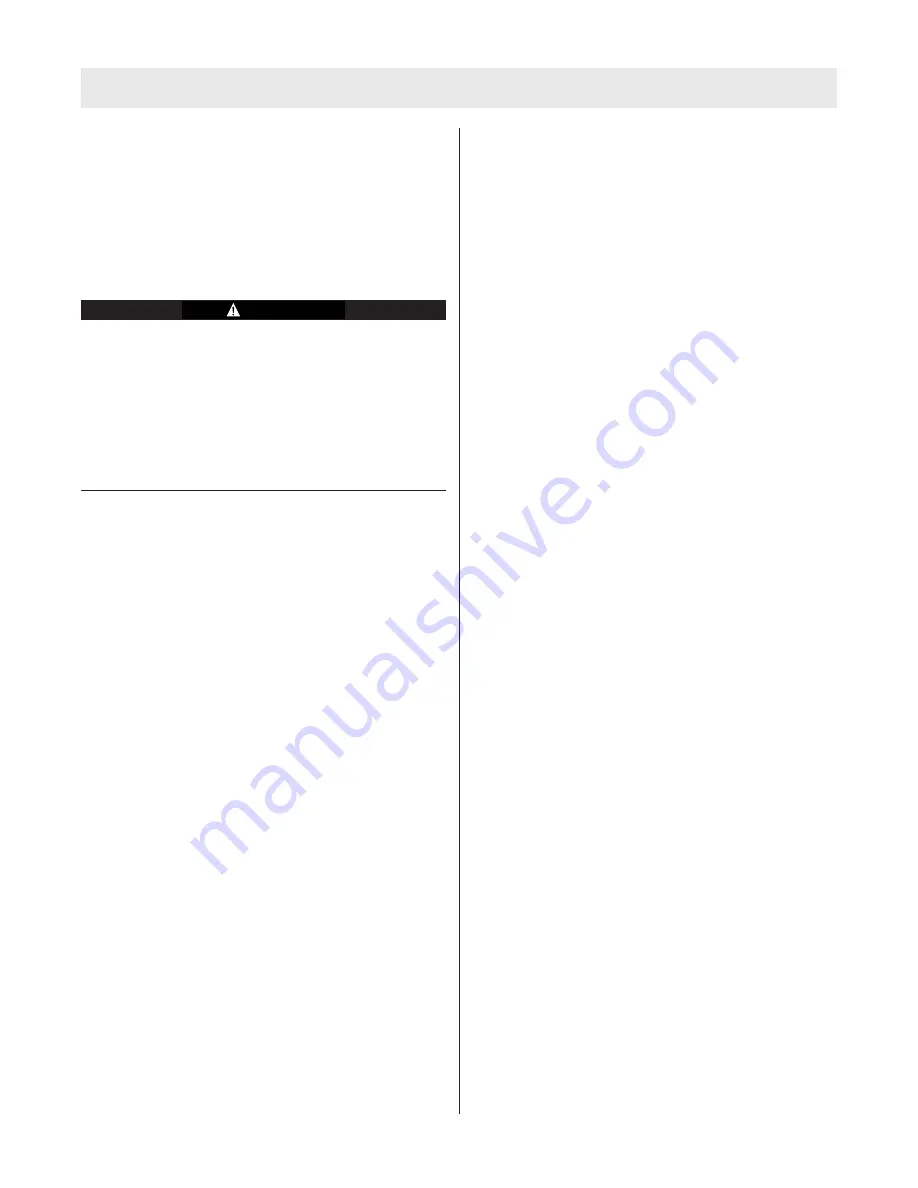
INSPECTION
INSPECTION
Inspect the entire SCBA after it is cleaned and disinfect-
ed. ANSI Standards Z88.2 and Z88.5, describe three lev-
els of inspection procedures which are to be performed.
Refer to these documents, or to an inspection program
prepared by a health professional in establishing an
inspection program. Detailed repair procedures are locat-
ed in MMR User’s Maintenance Instructions.
If the Air Mask does not meet any of the following
inspections, it must be removed from service.
Do not inspect the Air Mask before cleaning if there is
danger of contacting hazardous contaminants. Clean
and disinfect first, then inspect. Failure to follow this
warning can cause inhalation or skin absorption of the
contaminant and result in serious personal injury or
death.
COMPONENT INSPECTION
(AFTER EACH USE AND MONTHLY)
1. Don the Air Mask following the instruction procedures.
These steps make up the Air Mask Functional Test.
2. If all steps are performed successfully, remove the Air
Mask and inspect it following the steps below.
3. Facepiece
a. Inspect the facepiece for rubber deterioration, dirt,
cracks, tears, holes, or tackiness.
b. Check the harness headstraps for breaks, loss of
elasticity, missing buckles or straps. Check the
straps for signs of wear.
c. Inspect the lens for cracks, scratches, and a tight
seal with the facepiece rubber.
d. The exhalation valve must be clean and operate
easily. The valve must move off the seat and return
when released.
e. Inspect the facepiece coupling for damage. Also
check to be sure the spider gasket, and valve disc
are present.
4. Cylinder and Remote Gauges
a. Be sure you can see both gauge needles and face
clearly through the lens. Also be sure the gauge
stem is not bent.
b. Inspect the gauge hose for any visible damage.
5. Whistle Audible Alarm
a. Check that the whistle is undamaged and clean.
6. Cylinder
Breathing apparatus cylinders should be recharged as
soon as possible after use. Cylinders should not be
stored partially charged for two reasons:
• If used without recharge, the service life of the
apparatus is reduced.
• The cylinder burst disc vents excess pressure if a
full cylinder is over exposed to fire or heat. If the
cylinder is not full, it may be damaged before the
burst disc vents.
It is also essential that the required inspections and tests
be performed on all SCBA cylinders in accordance with
Department of Transportation (DOT) regulations. DOT reg-
ulations require that composite cylinders be retired from
service after the fifteenth year. Please note this does not
include cylinder valve assembly which may be reused.
Aluminum cylinder service life is indefinite if proper
inspection and hydrotest procedures are followed and
they indicate that the cylinder may remain in service.
Please contact your MSA distributor or sales associate if
you have questions or if you need additional information
regarding this policy.
Note:
ANSI Z88.5 recommends checking cylinder pres-
sure weekly. For maximum safety the cylinders should be
stored full or empty (pressure above ambient but less than
100 psig).
a. If the cylinder is less than FULL, recharge it before
storing it. Cylinder air must be at least CGA Quality
Verification Level (Grade) D respirable air.
b. Inspect the cylinder valve for signs of damage. The
valve may be opened slightly to be sure it operates
properly. Be sure to fully close the valve.
c. Inspect the cylinder body for cracks, dents, weak-
ened areas, corrosive agent, causing the fibers to
break or peel, or signs of heat-related damage. If
the cylinder is damaged return it to an MSA Service
Center. Call 1-800-MSA-2222 for instructions.
d. Check the hydrostatic test date on the cylinder
approval sticker located on the cylinder neck.
Fiberglass and Kevlar composite cylinders must be
tested every three years. Steel cylinders and carbon
fiber cylinders must be tested every five years.
8. Harness
a. Inspect all harness components for cuts, tears,
abrasion or signs of heat or chemically-related dam-
age.
9. Carrier
a. Inspect the cylinder strap and buckle to be sure it
holds the cylinder securely. Operate the over center
buckle to be sure that it opens and closes properly
and that it holds the cylinder securely.
b. Inspect back plate for cracks, weakened areas or
signs of heat or chemically related damages.
10. Record Keeping
Following inspection, the date and initials of the desig-
nated person should be recorded on an inspection
tag. A more detailed record of the operations per-
formed can be noted on an inspection and mainte-
nance log. Inspection tags and inspection and mainte-
nance logs are available from MSA. When the inspec-
tion data has been recorded, the breathing apparatus
is stored in a ready position.
17
WARNING
TAL 5010 (L) Rev. 3 - 10037469
Содержание AirHawk MMR
Страница 4: ...NOTES 4 TAL 5010 L Rev 3 10037469...
Страница 14: ...NOTES 14 TAL 5010 L Rev 3 10037469...
Страница 16: ...NOTES 16 TAL 5010 L Rev 3 10037469...
Страница 18: ...NOTES 18 TAL 5010 L Rev 3 10037469...
Страница 21: ...NOTES 21 TAL 5010 L Rev 3 10037469...
Страница 22: ...NOTES 22 TAL 5010 L Rev 3 10037469...
Страница 24: ......