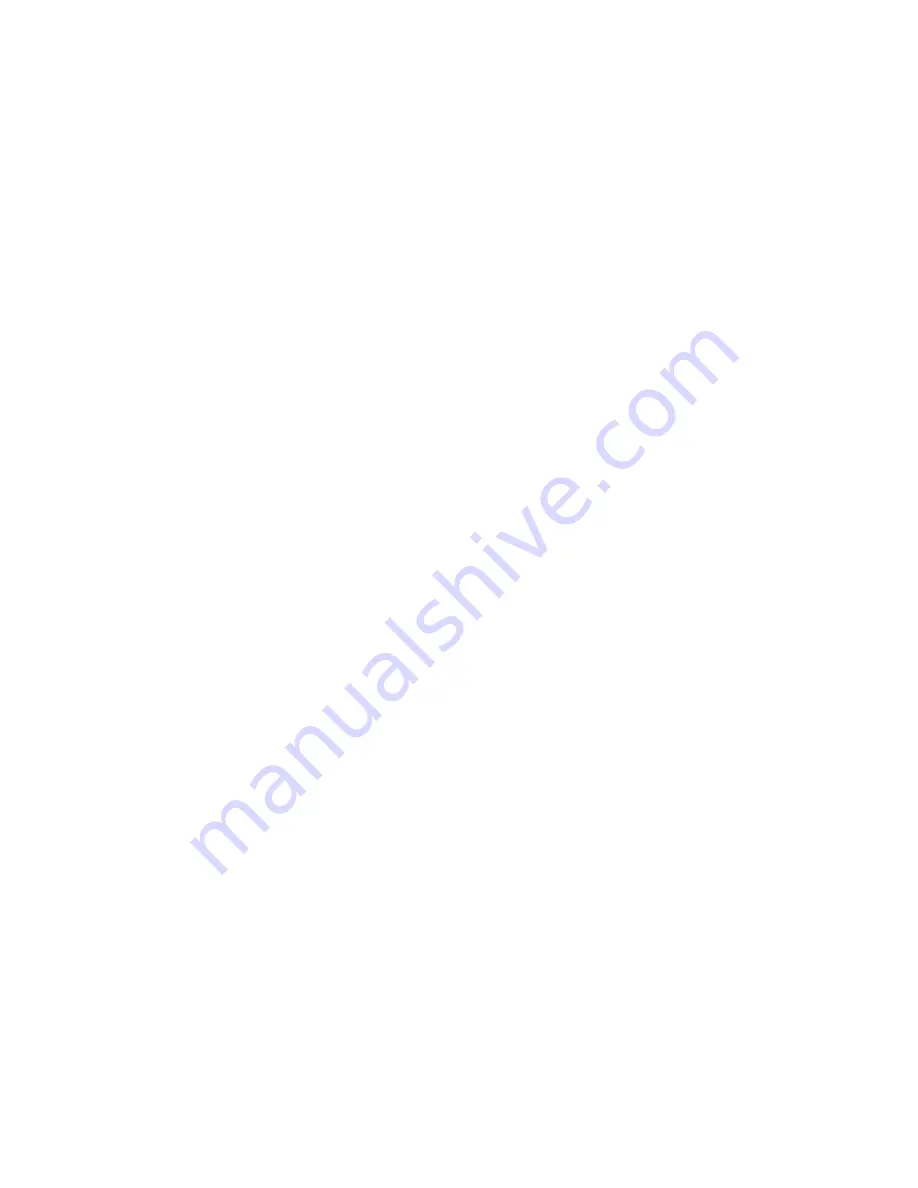
3.2.
Considerations and Explanations
•
The CDR is not intended to be a replacement for filtering conveyors and is not to be
used after a standard hinge belt conveyor.
•
The CDR is intended to be used after the following filtering conveyor styles. Drum,
disc, filter box, and in certain applications, magnetic conveyors.
•
A filtering conveyor is a conveyor with a filtration rating of 500μm (micron) or lower.
Common examples are the Mayfran Consep 2000 or similar, and LNS MH250 or
MH500 or similar.
•
The CDR is intended for machines running water-based coolants only. It does not
work with oil applications. A purge would be recommended for oil applications.
•
High volume machining centers running multiple shifts should get a filtering
conveyor.
o
A shift is considered 2000 hours/year, 2 Shifts would be 4000 hours/year, etc
•
The CDR is intended to filter out fines/debris smaller than 1/32” (thickness of a
credit card)
o
An easy way to determine this is to take a reasonably sized sample of chips
from the coolant tank right after the conveyor, dry them out, and lay on a
piece of paper next to a steel rule with graduations of 1/32”. Individual
chips/grains should not exceed 1/32”
•
The CDR is not intended to pick up or filter large chips. Large chips tend to settle to
the bottom of the tank rapidly and once the debris begins to pile up, it will stay there
until manually removed. Particles must stay in suspension long enough to get
sucked up by the pump.
•
The CDR does a great job at capturing and filtering “snow” like debris that spreads
evenly throughout the machine tank.
•
The CDR is for use with materials that have a specific gravity of 2x water or higher,
or a density 2g/cm^3 or higher. (Cast Iron, Aluminum, Steel, Alloys)
•
The CDR does not work well with plastics or composites. A purge would be
recommended for plastics or composites applications.
•
The CDR is typically located alongside the machine’s coolant tank where space will
allow. 15’ length hoses are provided to allow for positioning the CDR system where
it makes the most sense.
•
Machine’s producing less than 10 gallons of debris a month can typically use the 5-
gallon bucket to dispose of the debris in the CDR settling tank.
•
Machines with higher debris loads can purchase taller legs and mounting pads to
position the settling tank higher up to allow them to scrape the debris from the
settling tank right into their chip hopper.
•
The tank must be configured to allow proper circulation to ensure that a high
percentage of debris is removed over time and the tank eventually reaches an
equilibrium of debris being deposited, to debris being removed, maintaining an
acceptable PPM in the machine’s coolant tank.
•
Hydro cyclones work based on centrifugal forces separating the denser debris from
the lighter fluid and concentrating that debris into the discharge area while the
lighter fluid is carried back through the return to tank.
Содержание CDR80
Страница 4: ......
Страница 18: ...4 3 Floor Layout Standard CDR Dimensions ...
Страница 19: ... Severe Duty Models Only Extra Capacity Pre Filter Dimensions ...