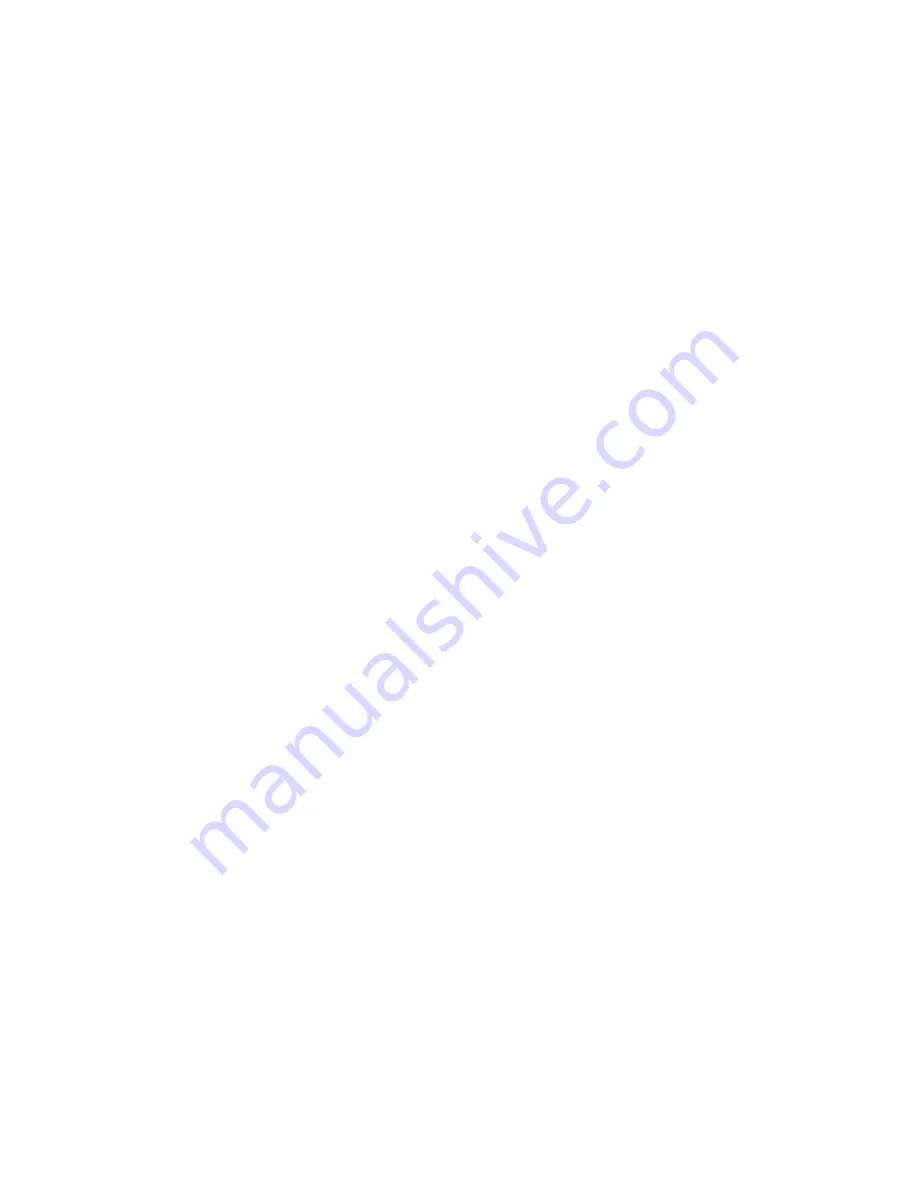
o
The high fluid velocities create high centrifugal forces that “pull” the denser
particles towards the walls of the cyclone cone. The velocity and forces
increase as the cone narrows towards the bottom. The heavier concentrated
debris is discharged through the bottom apex. The lighter fluid exits the top
of the cyclone via the vortex finder and returns to the machine coolant tank.
•
The CDR uses polypropylene hydrocyclones with ceramic apex cones for abrasion
resistance.
•
Performance on this type of technology is rated by the D50 cutoff point.
o
D50 cutoff means depending on several variables, 50% of the debris of a
certain size will be removed from the coolant and report to the settling tank,
while the other 50% of the debris will return back to the tank to be circulated
and filtered again.
•
Cyclonic filtration works on the idea that the coolant will be constantly circulated
and re-filtered every time is passes through the CDR.
o
Example, each time coolant passes through the cyclones, 50% of 5μm
particles are removed. The remaining 50% is then recirculated through the
tank and filtered again, removing 50% of it, and thus returning 25% of the
initial debris back to tank. On the 3
rd
pass, it will return 12.5% and so on.
•
The CDR has a flowrate of 80 GPM, meaning it can circulate and filter tanks at a
quick rate. Examples are as follows.
o
Tank = 80 gallons, CDR is 80GPM, tank is circulated once every 1 minute.
o
Tank = 100 gallons, CDR is 80GPM, tank is circulated once every 1 min 15
sec.
o
Tank = 200 Gallons, CDR is 80GPM, tank is circulated once every 2 min 30
sec.
•
The system should always be on and filtering when machining. There are several
ways to run the filter system, most do not require any additional wiring. Factory
settings are to start/stop the CDR by pressing the buttons on the HMI display. A
setting can also be enabled to allow the CDR to run automatically when powered
up. Another option is to run the filter on a scheduled Real time clock timer. Refer
to the quick start guide and PLC settings section for more information.
•
The alarm circuit interface with the machine is not typically required but is available
if desired. Typically, customers will rely on the status indicator light on the control
box to tell them when the CDR requires maintenance. This works for most
customers but if wanted, an alarm signal can be interfaced with the machine tool.
Refer to the interface drawing for more explanation.
•
For machines currently running, there is a quick way to determine debris load that
accumulates in the tank so it can be compared to how much debris is removed by
the filter over time. Carefully vacuum only the liquid coolant from one corner of the
tank and leave all sludge and debris remaining in the tank. Take several
measurements around the tank of how deep the layer of sludge is. Calculate the
average level. Calculate the volume of debris by measuring the area of tank and
multiplying by the average height of the debris. If measuring in “inches”, then divide
the total area of cubic inches by 231 to calculate total gallons of debris in the tank.
Then simply divide the number of gallons by the number of days it took to
accumulate. This will result in “X” gallons per day of material deposited into the
Содержание CDR80
Страница 4: ......
Страница 18: ...4 3 Floor Layout Standard CDR Dimensions ...
Страница 19: ... Severe Duty Models Only Extra Capacity Pre Filter Dimensions ...