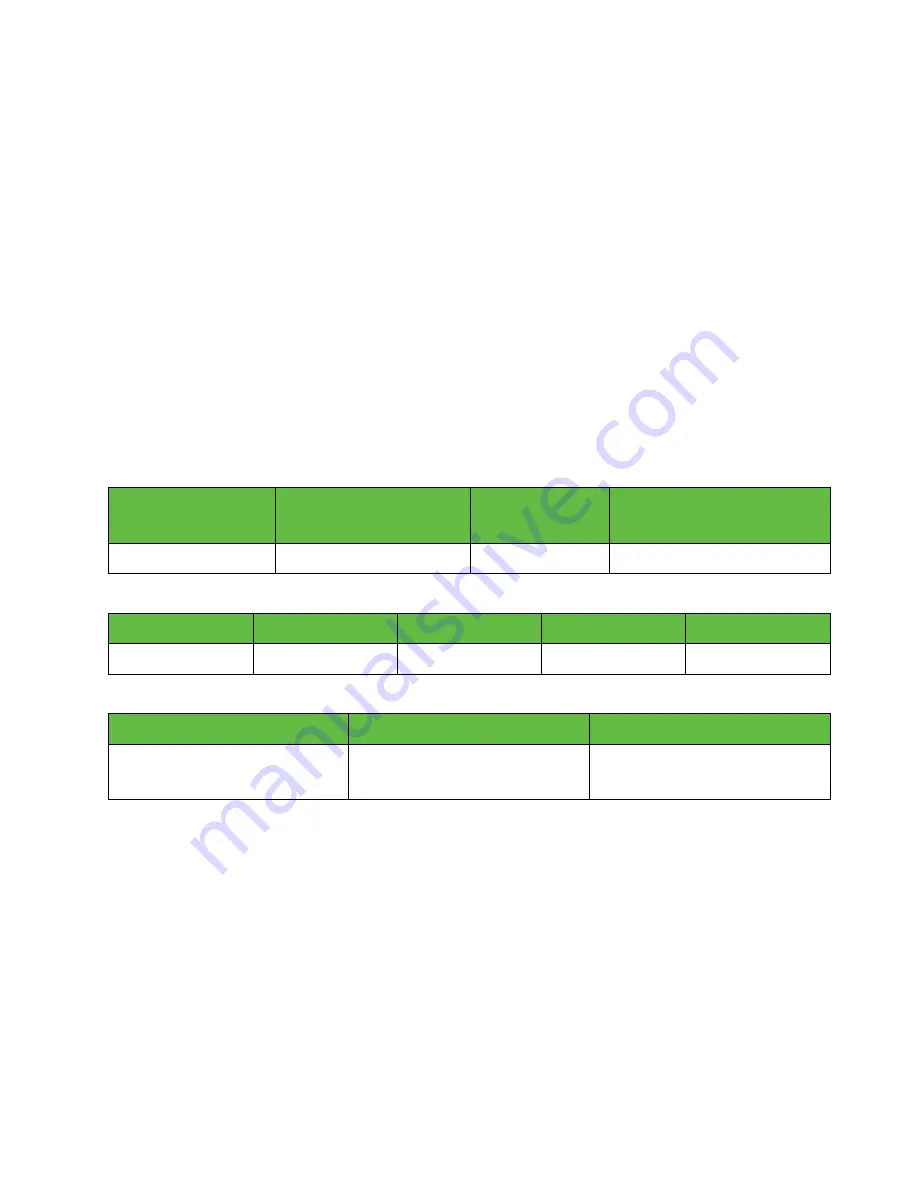
4.
Specifications
*All specifications are subject to change.
All MP Systems equipment ships with identification label. The label is located by main
disconnect on front of the system.
The label contains
•
Pump Type
•
Serial Number
•
Build Date
•
Operating voltage (208-230VAC)
(optional 480V)
•
FLA/ Largest Load for determining power service requirements
4.1 Electrical Specifications
All power for motors and hydraulics is derived from CDR Series power input source.
Main Power: 3 Phase @ 60Hz
Model
FLA @
208-230 VAC
FLA @
480 VAC
kVA
CDR80
8.5*
4.0*
3.2
Motor
HP
RPM
208-230 VAC
460 VAC
Feed Pump
3
3450
8.5A
4.0
Control Power
Control Signal
Alarm Circuit
208-230 VAC
24vdc
NC (Normally Closed)
NO (Normally Open)
Содержание CDR80
Страница 4: ......
Страница 18: ...4 3 Floor Layout Standard CDR Dimensions ...
Страница 19: ... Severe Duty Models Only Extra Capacity Pre Filter Dimensions ...