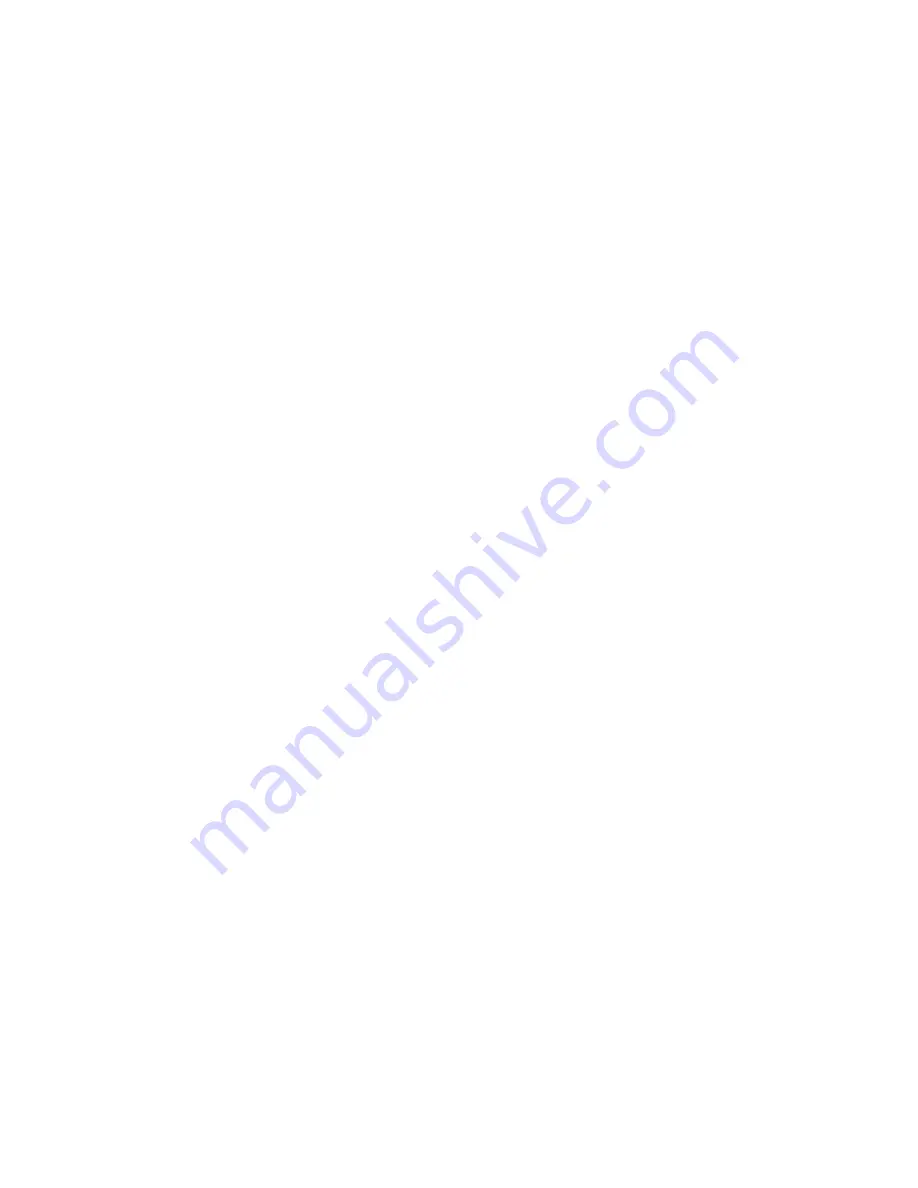
CSD Series
Variable Frequency AC Drive
MOTORTRONICS
- 47 -
Fn70 =
Electronic thermal overload reference current (motor rated
current)
Defines the motor rated current for the drive to set up the overload
protection curves as well as for slip compensation. Program the motor
rated current (FLA) into Fn70.
Fn71 =
Drive Overload Protection
XXX0:
Free run (coast) to stop after electronic thermal drive protection
is energized
XXX1:
Operation continued after electronic thermal drive protection is
energized
Fn71 determines the mode of operation of the drive after an overload
condition has been detected. After electronic thermal drive protection
is energized, the drive will baseblock immediately and the keypad will
blink OL2. To start the drive, it is necessary to press RESET key or
turn on the remote control RESET terminal. After the electronic thermal
drive protection is energized, the drive will continue to run and the
keypad will start blinking OL2 until current is lower than 110% rating.
Torque Boost Control
Fn71 =X0XX:
Torque boost Enable
X1XX:
Torque boost Disable
Note:
Fn72 is only active with this feature activated.
Fn72= Torque compensation gain - Factory Setting = 0.0%;
Range = 0.0% - 10.0%
Allows the customer to manually define the amount of torque boost
the drive puts out to the motor.
Fn73 = Reserved
Fn74 = Reserved
Slip Compensation
Fn75 and Fn76 can be used to allow the drive to automatically adjust
the PWM (Pulse Width Modulation) output to control motor slip to the
value specified by the motor manufacturer. Program Fn75 to the value
of motor current in a no load condition.
Fn75 = Motor no load current
Fn76 = Motor rated slip - Factory Setting = 0.00 Hz;
Range = 0.00 - 6.00 Hz
Program Fn76 to the value of motor rated slip as calculated by the
following formula:
Fn76 = (Fn36*/120) X (motor asynchronous speed**-motor rated speed)
*Fn36 = motor poles (2, 4, 6, etc.)
**motor asynchronous speed (RPM) = 120/Fn36 X motor rated
frequency (50 or 60 Hz)
The adjustment to the PWM output control is calculated internally by
the drive as follows:
Slip compensation frequency = [(output current - Fn75)/(Fn70 -Fn75)]
X Fn76
*Fn70 = motor rated current
Содержание CSD Series
Страница 2: ...CSD Series Variable Frequency AC Drive MOTORTRONICS 74 ...
Страница 4: ...CSD Series Variable Frequency AC Drive MOTORTRONICS 76 ...
Страница 30: ...CSD Series Variable Frequency AC Drive MOTORTRONICS 26 ...
Страница 32: ...CSD Series Variable Frequency AC Drive MOTORTRONICS 28 ...
Страница 65: ...CSD Series Variable Frequency AC Drive MOTORTRONICS 61 ...
Страница 74: ...CSD Series Variable Frequency AC Drive MOTORTRONICS 70 Prepared By Date Set By Date Received By Date ...