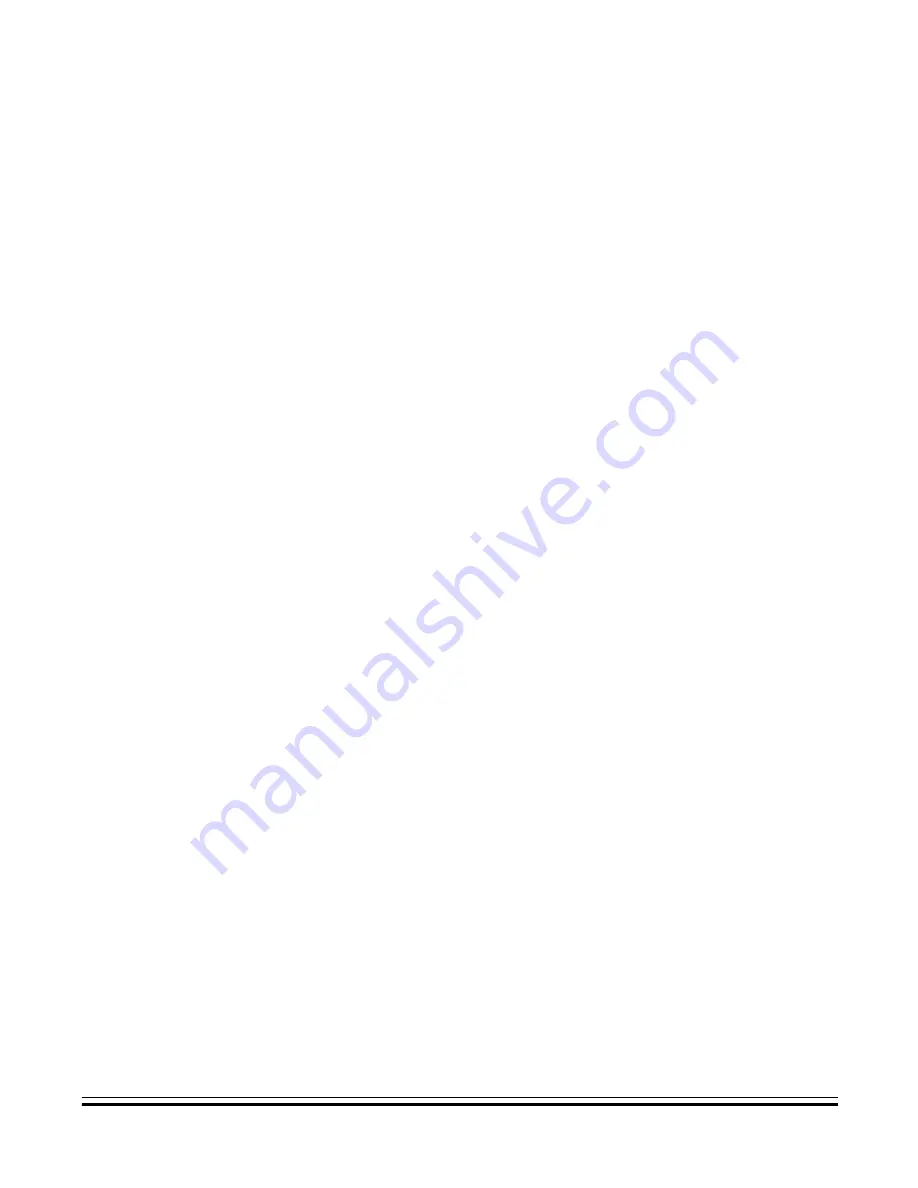
User Guide
Tuning for Customer Motor
DRM028 — Rev 0
Designer Reference Manual
MOTOROLA
User Guide
143
22. Observe the current transient at Alignment start, then stop motor
(or reset software)
23. Then modify the regulator parameters with PC master software as
in steps
8.
,
9.
,
10.
, and
11.
24. Repeat steps
21.
to
23.
until regulation is improved
25. Open
const_cust_x.h
and modify the regulator parameters with
the final variable values evaluated with PC master software
26. Build the code (see
Software Execution
and
Build
)
The last Alignment setting constant is Alignment Time period [ms]:
/* MUST_CHANGE_6_EXPER: */
#define PER_T_ALIGN_MS 1000.0
Range: <0,PER_BASE_T3_ALIGN_US/1000/255>
This period can be set experimentally. This constant can also be
evaluated using PC master software tuning file. This period must be high
enough to let the rotor stabilize during Alignment state. It is
recommended that you begin with large values such as 20,000 ms, then
it can be lowered. The period should be set to ensure that the rotor (and,
therefore, also the current) is stabilized at the end of Alignment state.
6.5.5 Software Customizing to Motor — Commutation and Start-up Control Setting
When all voltage and current settings are done, the motor commutation
and start-up parameters need to be set.
For settings which must be done, follow the labels
MUST_CHANGE_nn
,
MUST_CHANGE_EXPER_nn
in file
const_cust_x.h
.
For changes, which can be done (but usually are not necessary), follow
the labels
CAN_CHANGE_nn
,
CAN_CHANGE_EXPER_nn
in file
const_cust_x.h
NOTE:
Thanks to the Motorola patented start-up technique, the start
parameters setting is quite simple and reliable. However, in order to
reliably start the motor, the commutation control constants must be
properly set.
Detailed description starts here.
F
re
e
sc
a
le
S
e
m
ic
o
n
d
u
c
to
r,
I
Freescale Semiconductor, Inc.
For More Information On This Product,
Go to: www.freescale.com
n
c
.
..