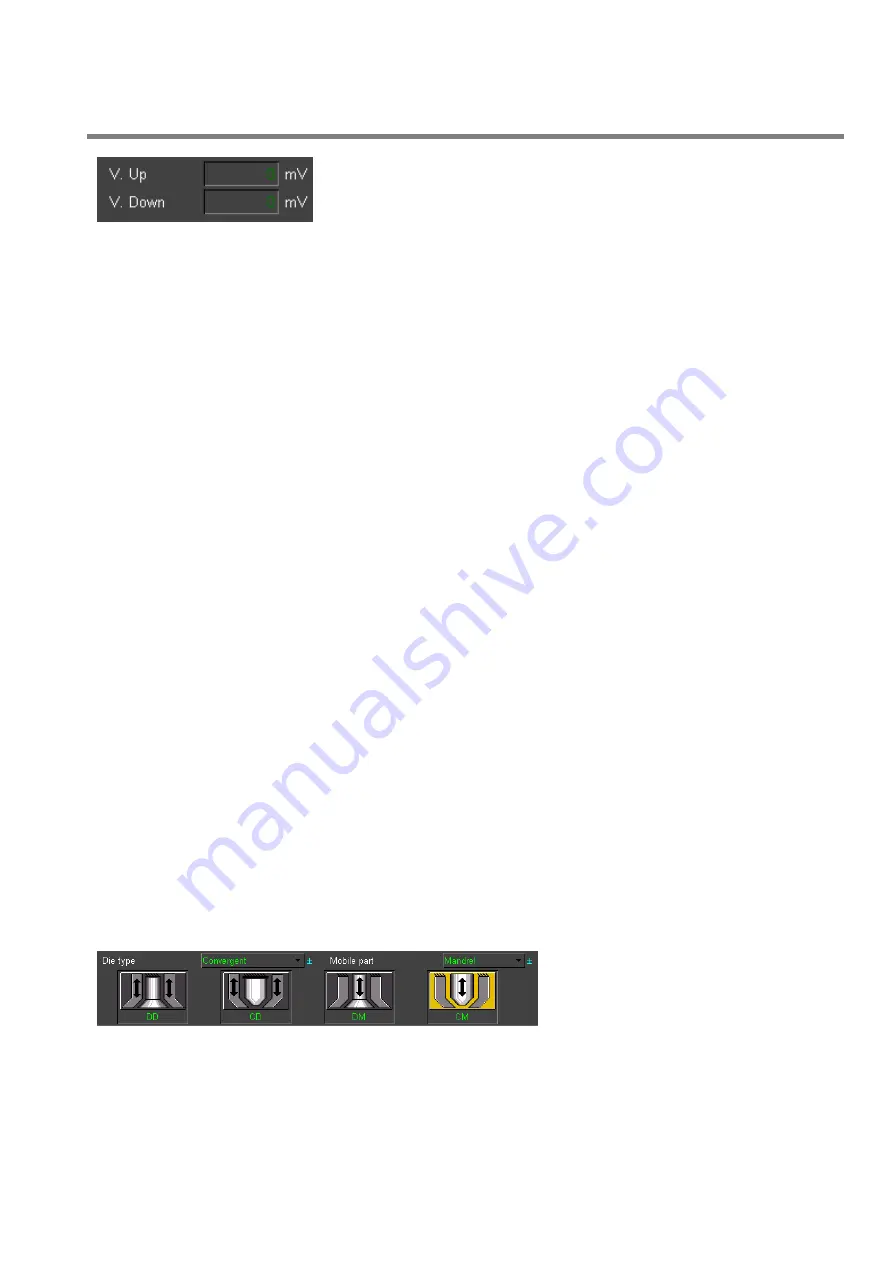
PARISON CONTROLLER
moog
Moog Italiana srl - Bergamo
MAN145-UM-D01A-EN
69
Figure 63
V. Up
and
V. Down:
In these fields the minimum and the maximum values
are visualized in mV relevant to the head total stroke. It is possible to modify
manually these values.
MANUAL OPEN LOOP CALIBRATION WITH NO-INTELLIGENT ACTUATORS:
The input calibration can be made in manually open loop state. The purpose can be input calibration or manual
movement. Through manual commands it is possible to issue an output voltage that moves the actuator up or
down. The operator can visually check that the mechanical limits have been reached and confirms them. Output
command during manual motion ramps up while buttons are pressed and stay fixed when released. The output
command is expressed in % of maximum value, while the ramp is expressed in mV per second.
MANUAL OPEN LOOP CALIBRATION WITH INTELLIGENT ACTUATORS:
Through manual commands it is possible manage two kinds of ramps: from 0 to max and from max to 0. Output
command during manual motion ramps up while buttons are pressed and stay fixed when released.
MANUAL CLOSE LOOP CALIBRATION WITH NO-INTELLIGENT ACTUATORS:
The input calibration can be made manually in closed loop. The system generates a position setpoint (expressed
in %) and holds it in close loop. Through manual commands it is possible to change the position setpoint causing
the actuator to move up and down. The operator visually acknowledges when a mechanical limit has been reached
and confirms. The position setpoint is set by generating ramp signals increasing in % per second.
MANUAL CLOSED LOOP CALIBRATION WITH INTELLIGENT ACTUATORS:
It automatically generates the ramps with the pressure of the UP or DOWN buttons. The movement is interrupted
with a new pressure of the same button.
AUTOMATIC CALIBRATION WITH NO-INTELLIGENT ACTUATORS:
The input calibration can be made automatically in closed loop. By keeping the regulator in loop it is possible to
automatically start the procedure that moves the actuator down, intercepts the mechanical end-of-stroke, moves
the actuator up, intercepts the mechanical end-of-stroke and saves the corresponding voltage values. Change of
position setpoint is made by setting up two ramp values in % per second.
AUTOMATIC CALIBRATION WITH INTELLIGENT ACTUATORS:
Starting the procedure generates a ramp from 0 to max. to move the head down. At the end of this phase after 3
seconds it generates a ramp from max. to 0 to move the head up. It automatically saves the input values.
4.6.3
Die type.
It is possible to indicate if the actuator moves the mandrel or the die and if the mandrel is convergent or divergent.
This univocally identifies if the zero position is when the actuator is at upper or lower end-point.
Figure 64
Die type:
Select the die type with the knob
then press SET to confirm:
Convergent
.
Divergent
.
Mobile part:
Select the mobile part with the knob then press SET to confirm:
D-D:
Die type
Divergent
and mobile part
Die.
C-D:
Die type
Convergent
and mobile part
Die.
D-M:
Die type
Divergent
and mobile part
Mandrel.
C-M:
Die type
Convergent
and mobile part
Mandrel.
Содержание IMI220-145D001
Страница 1: ...MOOG Manual IMI220 145D001 Parison Controller...
Страница 24: ...PARISON CONTROLLER moog 24 MAN145 UM D01A EN Moog Italiana srl Bergamo 2 5 8 Position Accumulator Figure 25...
Страница 25: ...PARISON CONTROLLER moog Moog Italiana srl Bergamo MAN145 UM D01A EN 25 Figure 26...
Страница 44: ...PARISON CONTROLLER moog 44 MAN145 UM D01A EN Moog Italiana srl Bergamo 3 7 Terminal measures Figure 36 UNIT mm...
Страница 45: ...PARISON CONTROLLER moog Moog Italiana srl Bergamo MAN145 UM D01A EN 45 Figure 37 UNIT mm...
Страница 46: ...PARISON CONTROLLER moog 46 MAN145 UM D01A EN Moog Italiana srl Bergamo Figure 38 UNIT mm...
Страница 54: ...PARISON CONTROLLER moog 54 MAN145 UM D01A EN Moog Italiana srl Bergamo...