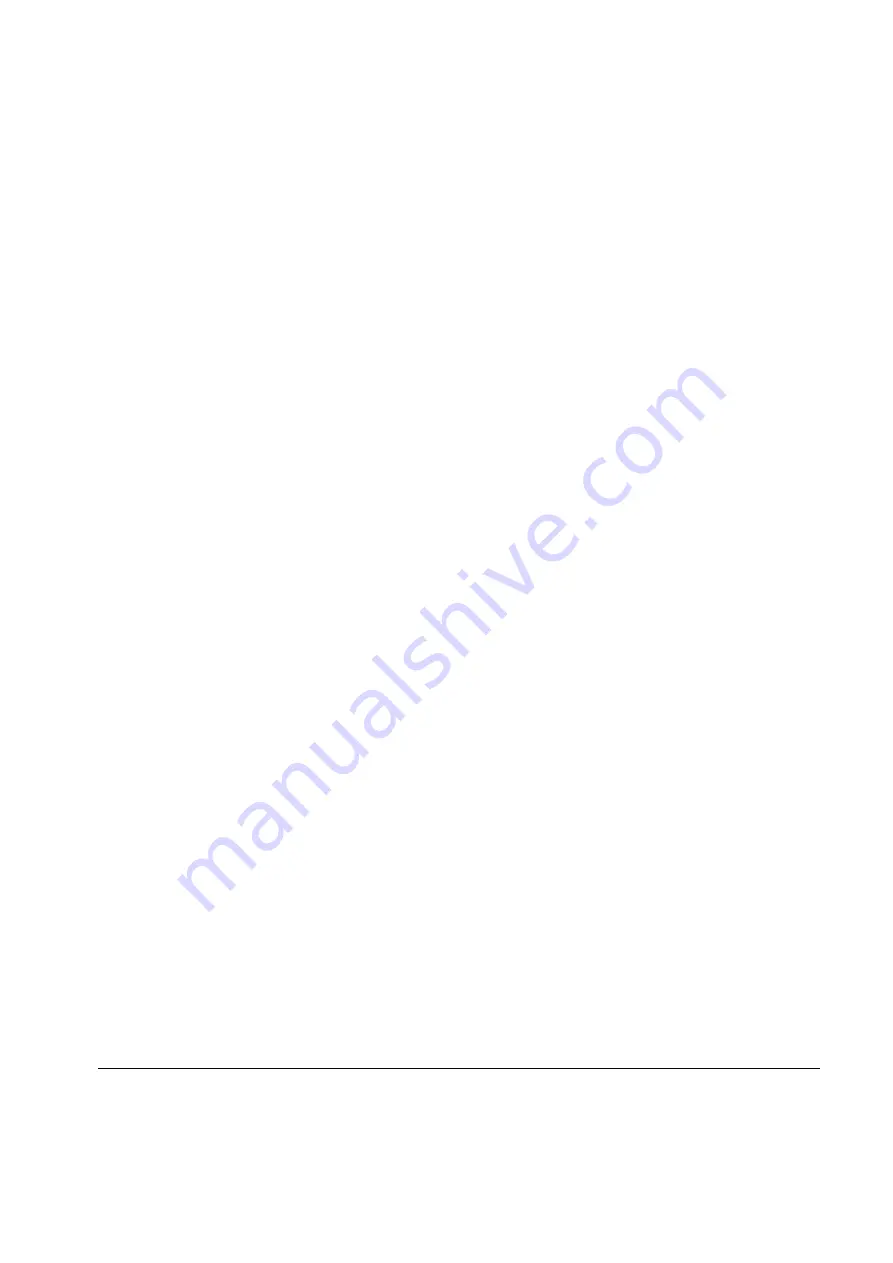
17
technological operation can be performed in a number of ways: immersion into the
reagent, immersion with a programmed period of activation, repeated dipping of slides into
the reagent (can accelerate the speed of procession).
When processing of a rack is complete, it goes back to the initial station, where it
has been loaded in the beginning*— the Stainer
signals about the completion of
processing of each rack and all loaded racks. Unloading of racks is performed
automatically with the help of the manipulator.
The mechanics of Stainer is unique in simplicity and reliability. The racks with slides
rotate not only in a horizontal plane but also up and down. The rising of a rack from
reagent is accompanied by inclining and vibration, which facilitates the draining of excess
liquid from slides and the rack. Thus, the transfer of reagents between troughs is very low.
The manipulator mechanism is designed in such a way that a rack gets firmly fixed in its
grab, making it possible to carry out high-speed movements (during dipping, shaking,
transfer from station to station, etc.). The option to program the duration of delay of a rack
above the trough (‘draining time’) lets excessive reagent flow off. Programming the interval
for the new rack processing launch makes it possible to configure programs with a parallel
procession of several racks. To multiply performance, there is a possibility to install several
troughs with the reagent that is used for a most time-consuming operation.
Thus, the Stainer offers a good number of opportunities to make the process of
staining FAST, versatile, and efficient despite their compact size.
*There is one exception of this rule: the reagent <XYLENE-E>, assigned to a station,
where the last operation of a program is performed, possess particular properties.
When this reagent is assigned, the processed rack with slides remains at the last station
in <XYLENE-E> and does not return to the parking station.