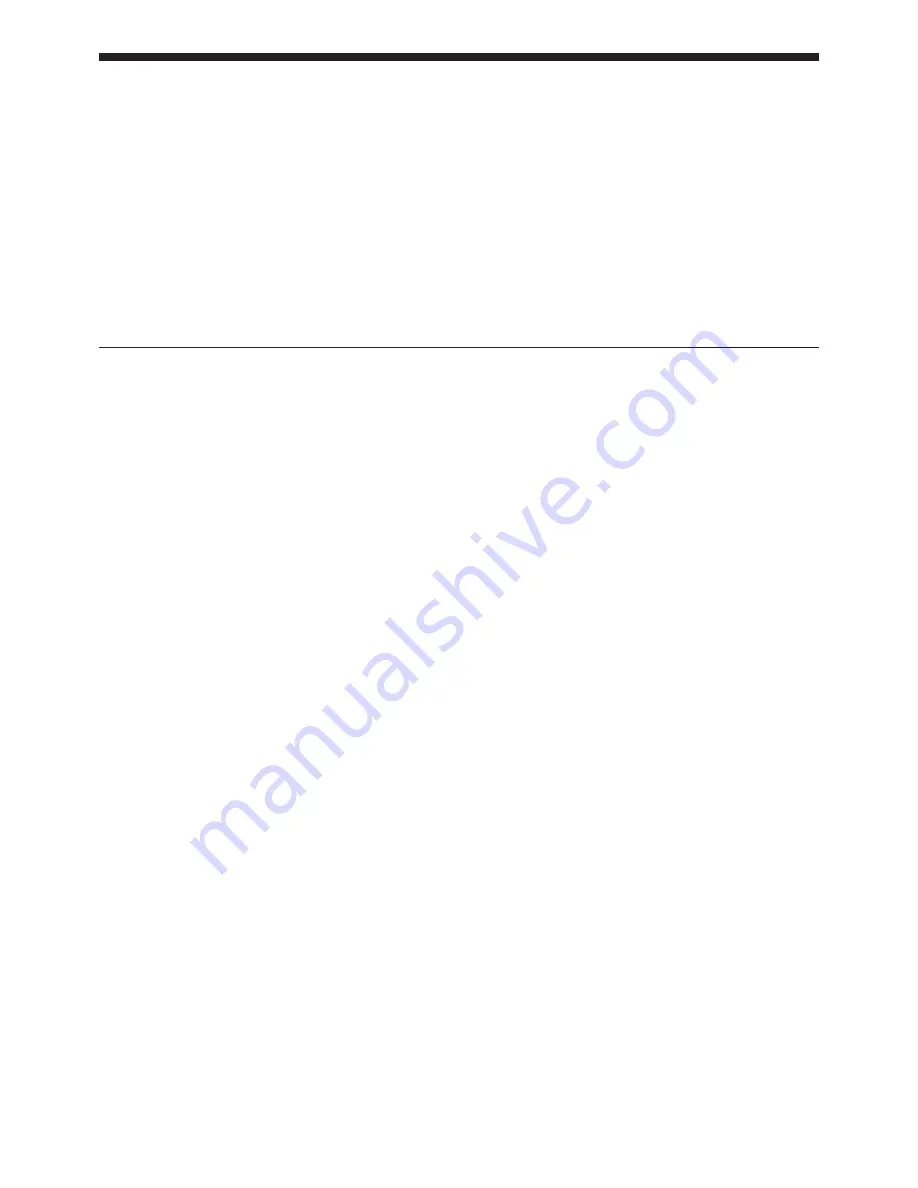
MPI – GENERAL
13A-1
SECTION 13A
MPI (Multi-point Fuel Injection)
CONTENTS
General ..................................................................... 2
Servicing standards .................................................3
Special tools ............................................................3
Troubleshooting ......................................................5
Servicing the vehicle ............................................29
1. Adjusting specified revolutions when idling.....29
2. MPI system components layout diagram........29
3. Checking the air temperature sensor..............29
4. Checking the oil feeder control valve..............30
GENERAL
Servicing guidelines have been changed because of the changes listed below.
• A variable valve timing control system (V.V.T.) has been adopted. Because of this, an oil feeder control valve and an intake
cam position sensor have been added.
• A manifold absolute pressure (MAP) sensor has been added.
• An air temperature sensor has been added.
Содержание Lancer Evolution IX 2005
Страница 1: ...LANCER Evolution IX Chassis Engine Wiring Diagrams ...
Страница 2: ...SERVICE MANUAL Supplement ...
Страница 6: ... Notes ...
Страница 8: ... Notes ...
Страница 16: ... Notes ...
Страница 22: ... Notes ...
Страница 64: ...13A 24 MPI TROUBLESHOOTING 13A 23 6 Service data table 7 Engine ECU checks 7 1 Terminal voltage table ...
Страница 106: ... Notes ...