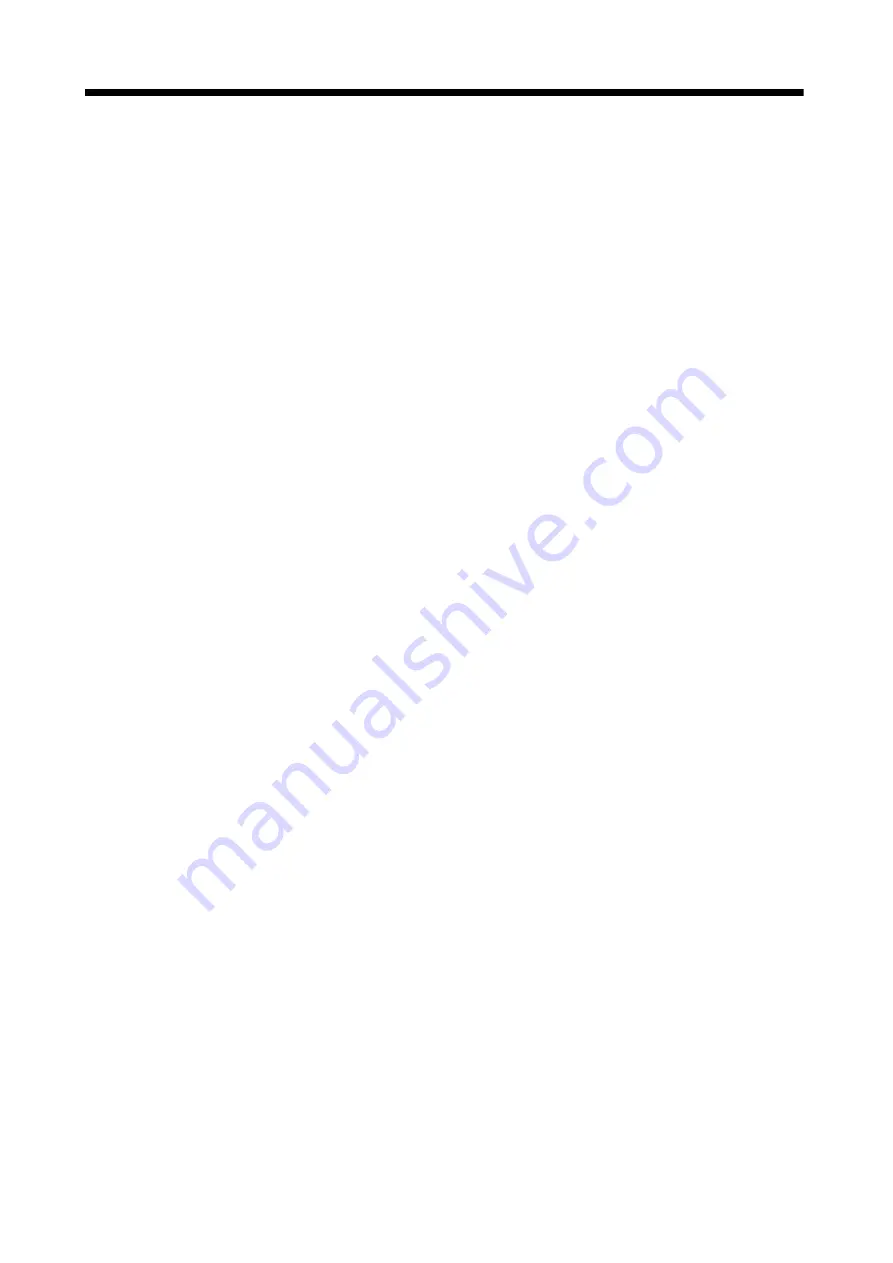
4 - 6
4. OPERATION
(4) Servo on
Switch the servo on in the following procedure:
1) Switch on main circuit/control power.
2) Switch on the servo on signal (SON) (short SON-SG).
When placed in the servo-on status, the servo amplifier is ready to operate and the servo motor
is locked.
(5) Start
Using speed selection 1 (SP1) and speed selection 2 (SP2), choose the servo motor speed. Turn on
forward rotation select (DI4) to run the motor in the forward rotation (CCW) direction or reverse
rotation select (DI3) to run it in the reverse rotation (CW) direction, generating torque. At first, set a
low speed and check the rotation direction, etc. If it does not run in the intended direction, check the
input signal.
On the status display, check the speed, load factor, etc. of the servo motor.
When machine operation check is over, check automatic operation with the host controller or the like.
(6) Stop
In any of the following statuses, the servo amplifier interrupts and stops the operation of the servo
motor:
Refer to Section 3.8, (2) for the servo motor equipped with electromagnetic brake.
(a) Servo on (SON) OFF
The base circuit is shut off and the servo motor coasts.
(b) Alarm occurrence
When an alarm occurs, the base circuit is shut off and the dynamic brake is operated to bring the
servo motor to a sudden stop.
(c) Forced stop (EMG) OFF
The base circuit is shut off and the dynamic brake is operated to bring the servo motor to a sudden
stop. Alarm A. E6 occurs.
4.3 Multidrop Communication
You can use the RS-422 communication function to operate two or more servo amplifiers on the same bus.
In this case, set station numbers to the servo amplifiers to recognize the servo amplifier to which the
current data is being sent. Use parameter No. 15 to set the station numbers.
Always set one station number to one servo amplifier. Normal communication cannot be made if the same
station number is set to two or more servo amplifiers.
For details, refer to Chapter 13.