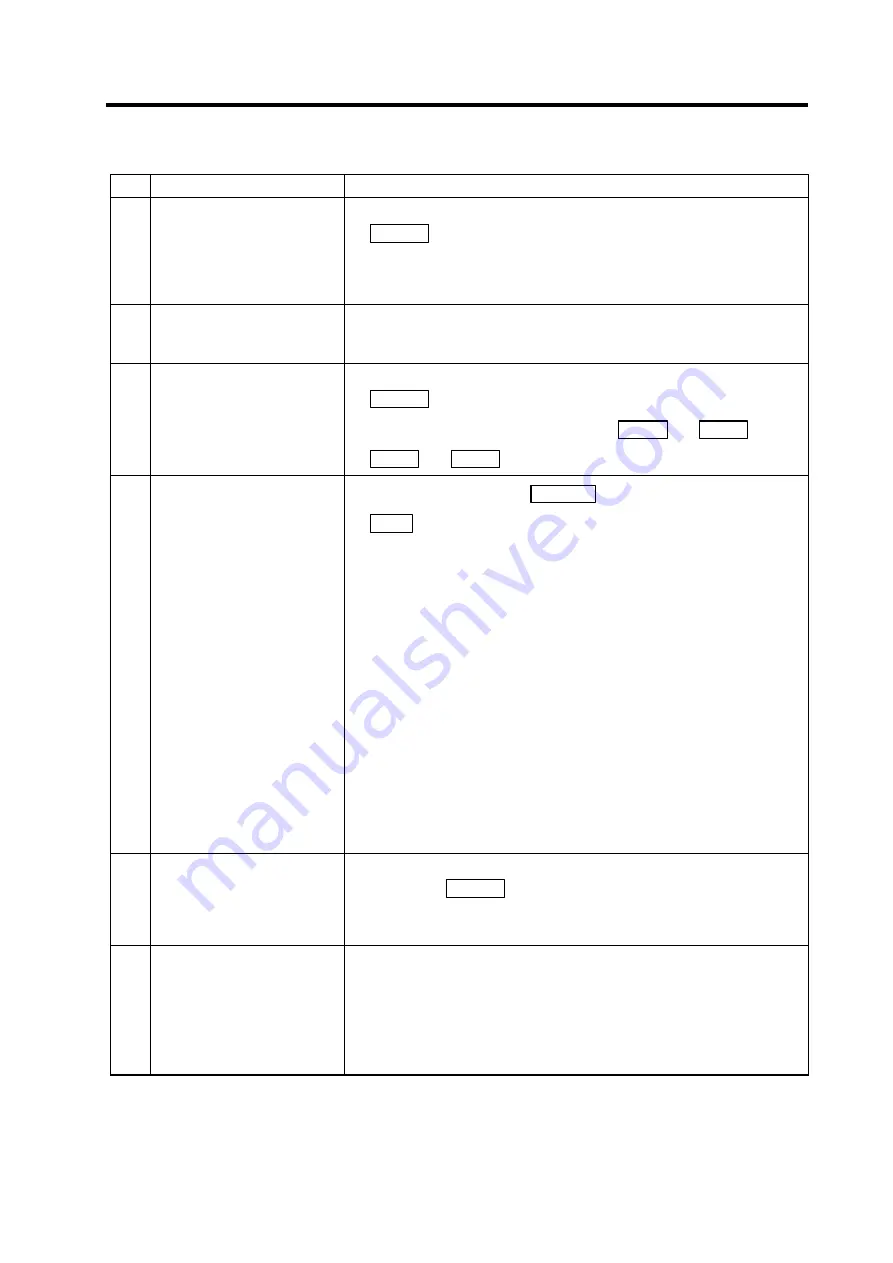
8. Adjustment Procedure
8
−
18
8.6.2 Troubleshooting for abnormal synchronous tap
No. Phenomenon
Factors/remedy
1
An EXCESSIVE ERROR
ALARM (alarm 52) occurs.
1) The synchronous tap detector direction of spindle parameter
SPECT bit5 is set backwards.
2) The spindle motor does not follow commands because the tap
time constant is too short. Multiply the start time for S commands
×
1.2 or more and set that value.
2 An
OVERCURRENT
(alarm 32) occurs.
1) The spindle motor does not follow commands because the tap
time constant is too short. Multiply the start time for S commands
×
1.2 or more and set that value.
3
The spindle rotation
movement amount does
not match the command
value.
1) The closed/semi-closed setting is incorrect in spindle parameter
SPECT bit0.
2) The spindle parameter gear settings GRA1 to GRA4 and
GRB1 to GRB4 do not match the machine gear ratios.
4
1) The tap breaks.
2) The tap accuracy is
poor.
1) The (Z axis) parameter PGNISP and spindle parameter
PGM values are different.
2) The tap time constant is short.
3) The program thread pitch F and actual tap pitch are different.
4) The tap is slipping at the chuck.
→
Substitute with a chuck having a large tightening torque.
5) The prepared hole is shallow, and the cutting chips are not being
discharged properly.
6) A tap with poor cutting chip discharge is being used. (A spiral tap
is preferred.)
7) The tap depth is too deep for the tap diameter. (Normally 2 to 3
fold)
8) Noise is superimposed on the position feedback signal, causing
poor synchronization accuracy. Check the shielding on the
spindle encoder cable for a closed method, and the speed
feedback cable from the motor for a semi-closed method.
→
Check whether the correct shielded cable is being used.
Also check for cable breaks.
9) Replace with a new tap.
5
1) The load is heavy. The
spindle stops during
tapping and the
accuracy is becoming
worse.
1) Select stronger excitation by setting bit 3 of the spindle
parameter SPECT to 1.
2) Raise the speed loop gain during tapping.
3) Use tapping paste.
6
There is no problem at low
speeds (1000rpm or less),
but the following occur at
high speeds:
1) The tap breaks.
2) The tap accuracy is
poor.
1) The position loop gain deviates slightly.
(Example)
With the closed method, the pulley ratio does not
match the theoretical gear ratio when the motor and
spindle are connected with a V-belt.