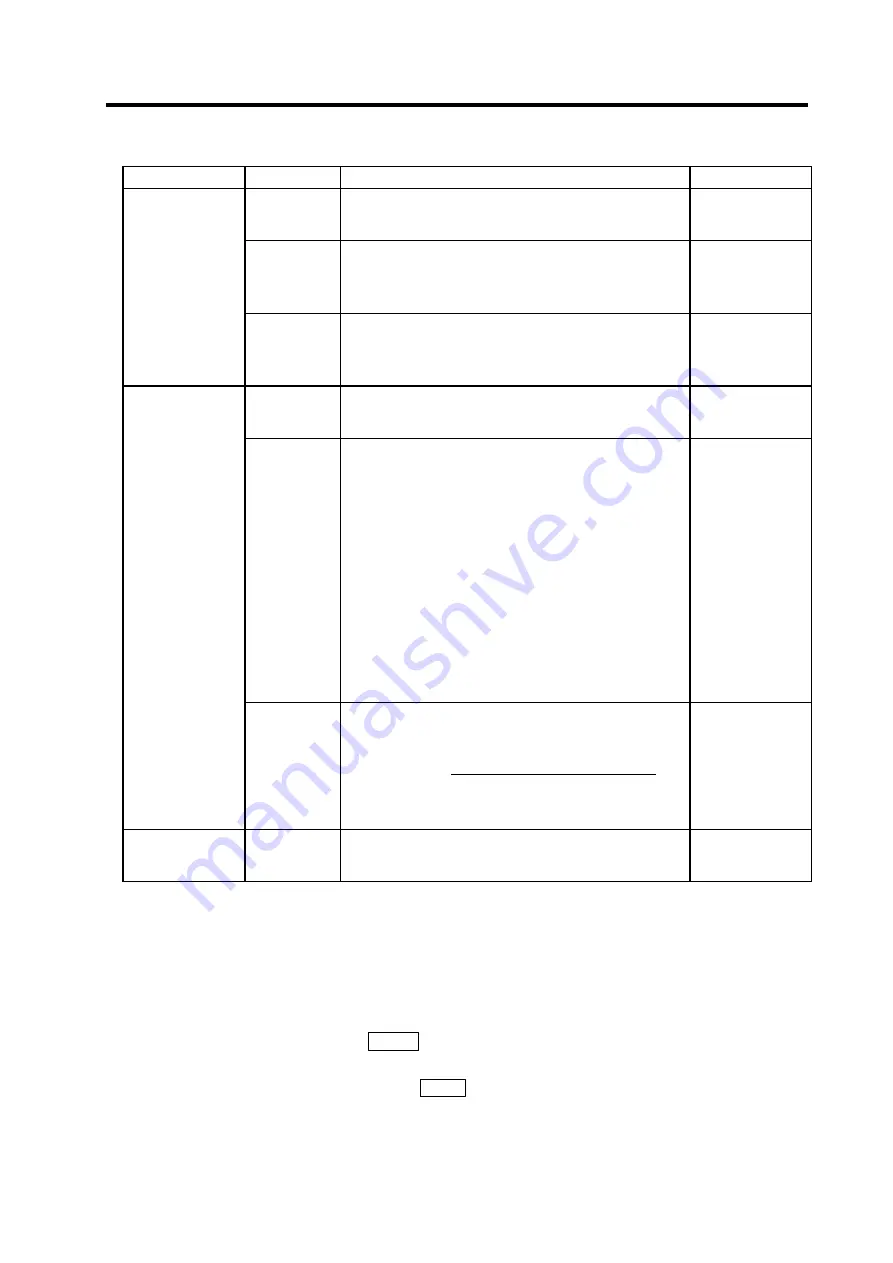
8. Adjustment Procedure
8
−
16
Screen selection
Parameter
Details
Setting value
SPINDLE NC
PARAMETER
sgear
This sets the gear ratio between the spindle and spindle
encoder. Always set this to 0 (1:1) when there is no
spindle encoder (semi-closed method).
0
Standard: 0
stap
1
stap 2
stap 3
stap 4
Gear00, Gear 01, Gear 10, Gear11
Set the max. spindle speed during the constant
inclination tap cycle in each gear.
0 ~ 99999 (rpm)
stapt
1
stapt 2
stapt 3
stapt 4
Gear00, Gear01, Gear10, Gear11
Set the time constant to the max. tap speed during the
constant inclination tap cycle in each gear. The setting
method is the same as that in tap-tl above.
0 ~ 5000 (msec)
SPINDLE
PARAMETER
PGT
This sets the position loop gain during synchronous tap.
This must be set to the same value as parameter
PGN1SP of the (Z axis).
1 ~ 100
Standard: 10
SPECT
bit5
.....
This sets the rotation direction of the detector
(spindle encoder) during synchronous tap. Set
to 0 for semi-closed method.
bit3
.....
Set to 1 for stronger excitation during
synchronous tap. The response to the impact
load increases. Normally set to 0.
bit0
.....
0: Closed (spindle with encoder)
1: Semi-closed (spindle without encoder)
bit4
.....
This determines the motor command direction
(spindle rotation direction in G84) during
synchronous tap.
bitE=0
.
A zero point return is carried out at the first of
the synchronous tap mode.
bitE=1
.
The position loop is entered after the
deceleration stop without carrying out a zero
point return.
−−
GRA1
~
GRA4,
GRB1 ~
GRB4
The gear ratio (No. of gear teeth) of each gear stage
must be accurately set.
Motor speed
×
Motor shaft side No. of gear teeth
(GRB1 to GRB4)
Spindle side No. of gear teeth
(GRA1 to GRA4)
= Spindle speed
−−
EGEAR
This sets the gear ratio between the spindle and spindle
encoder. Always set this to 0 (1:1) when there is no
spindle encoder (semi-closed method).
0
Standard: 0
< Precautions >
1) Accurate synchronous tapping is difficult when the spindle is driven with a belt or timing belt in
the semi-closed method (when there is no spindle encoder), due to the stretching, slipping,
etc. of the belt.
Use an encoder when driving the spindle with a belt, and carry out synchronous tap with the
closed method. Use the encoder method orientation in this case.
2) Set the spindle parameter EGAR to 1 when the spindle and encoder are connected by a
2:1 speed ratio in the closed method (when there is a spindle encoder).
Also set the spindle NC parameter sgear to 1.