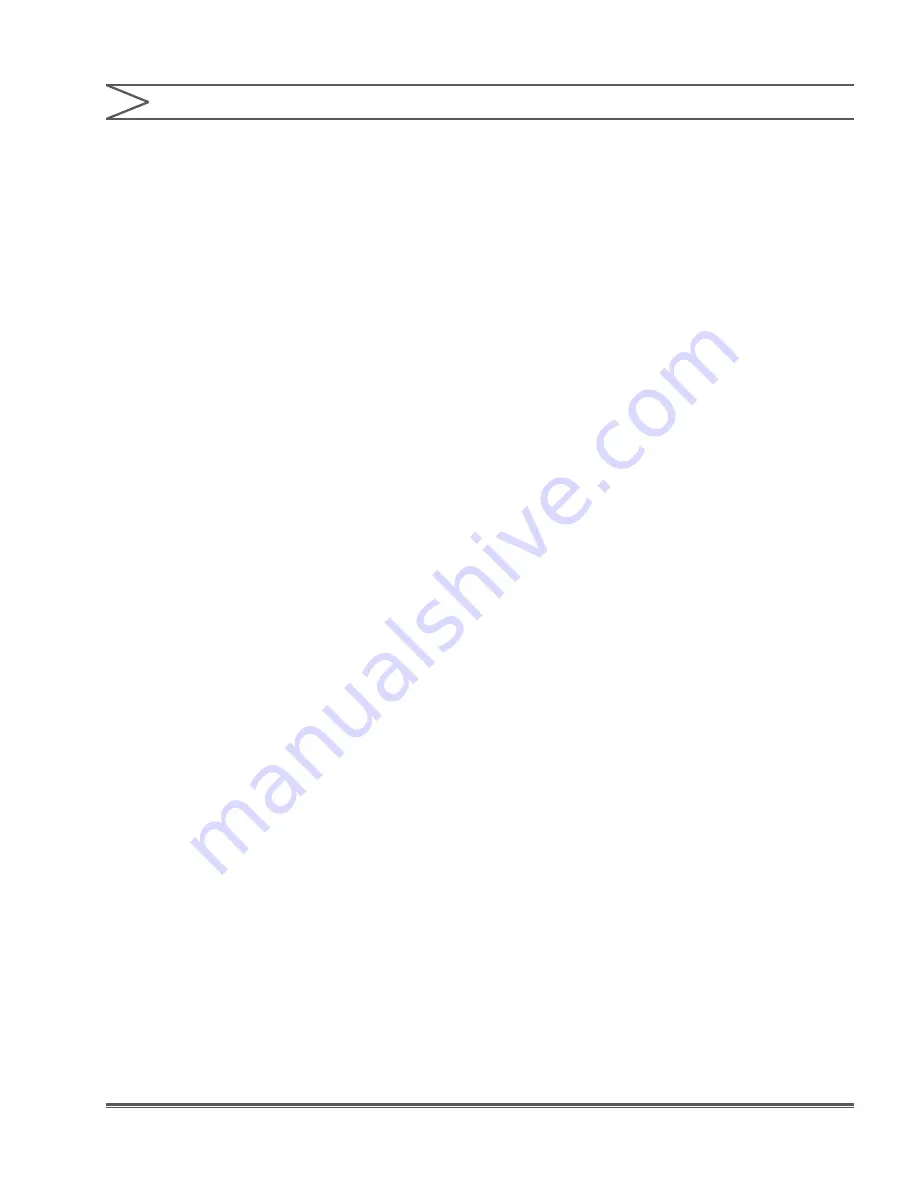
7
Instruction Manual
SECTION 2 - INSTALLATION
2.6.2 General Piping Considerations
1. Use extreme care in piping to plastic liquid
end pumps with rigid pipe such as PVC. If any
stresses or vibration are unavoidable, flexible
connections are recommended.
2. Use piping materials that will resist corrosion by
the liquid being pumped. Use care in selecting
materials to avoid galvanic corrosion at pump
liquid end connections.
3. Use piping heavy enough to withstand maximum
pressures.
4. Remove burrs, sharp edges, and debris from
inside piping. Blow out all pipelines before
making final connections to pump.
5. Because vapor in the liquid end will cause
inaccurate pump delivery, piping should be
sloped down to pump suction check valve to
prevent vapor pockets.
6. When pumping suspended solids (such as
slurries), install plugged crosses at all 90° line
turns to permit line cleaning without dismantling
piping.
7. See
Figure 4
for a typical recommended pump
installation scheme.
2.6.3 Suction Piping Considerations
1. It is preferable to have the suction of the pump
flooded by locating the liquid end below the
lowest level of the liquid in the supply tank.
Installing the supply vessel on the suction line
in close proximity to the pump will help ensure
a flooded suction line.
2. Avoid negative suction pressure conditions
(suction lift), as such conditions adversely
affect metering accuracy. A lift of 20 Ft. of water
column straight out of a supply tank is the
maximum suction lift permissible.
3. MILROYAL
®
G pumps are intended to be
operated with process liquid supplied at or
above atmospheric pressure. Although these
pumps can move liquids supplied at less
than atmospheric pressure, in these negative
pressure applications it is important that all
connections be absolutely drip free and vacuum
tight.
4. When pumping a liquid near its boiling point,
provide enough suction head to prevent the
liquid from “flashing” into vapor when it enters
the pump liquid end on the suction stroke.
5. If possible use metal or plastic tubing for the
suction line because such tubing has a smooth
inner surface and can be formed into long,
sweeping bends to minimize frictional flow
losses.
6. A strainer should be used in the suction line to
prevent foreign particles from entering the liquid
end. This and any other measures to prevent
debris from entering and fouling the ball-checks
will give increased maintenance-free service.
Check strainer frequently to prevent blockage
which could lead to cavitation.
7. Keep suction piping as short and straight as
possible.
8. Piping size should be one or two sizes larger
than the liquid end suction fitting to prevent
pump starvation.
9. If long suction lines are unavoidable, install a
stand pipe or suction accumulator dampener
near the pump in the suction line.
10. Suction piping must be absolutely airtight to
ensure accurate pumping. After installation,
test suction piping for leaks with air and soap
solution.