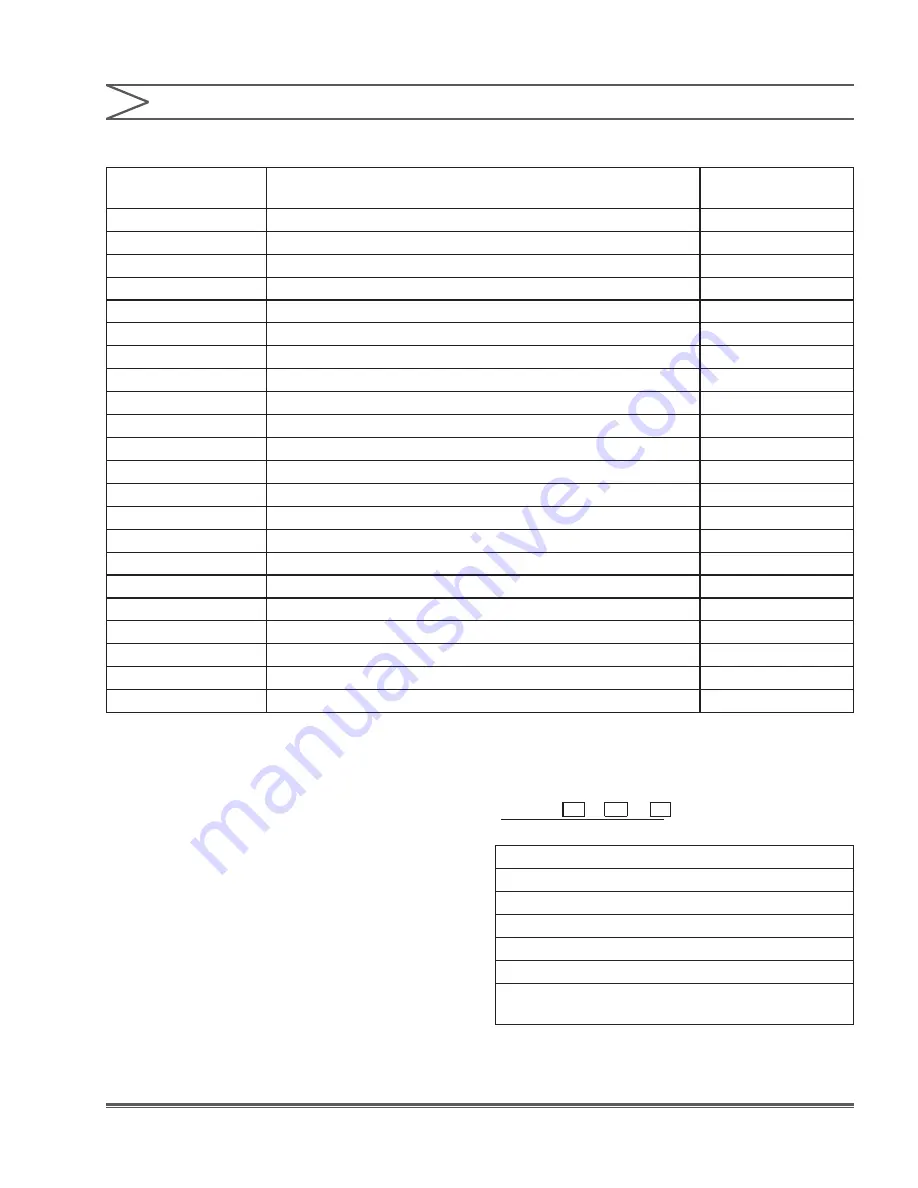
29
Instruction Manual
SECTION 6 - PART NUMBERS
6.2.3 3- FUNCTION VALVE
(see Figure 8)
Item No.
Description
Qty.
Req.
850
Valve Cap
1
860
Purge Button
1
870
Pin
1
880
Purge Button Spring
1
890
Relief Valve Adjustment Screw
1
900
Relief Valve Locking Nut
1
910
Relief Valve Adjustment Nut
1
920
O-Ring
2
930
Purge Stem
1
935
Washer
1
940
O-Ring
1
950
Relief Valve Spring (1-1/4, 1-3/4” plungers)
PVC Liquid End (purple)
1
Metallic Liquid End (orange)
1
950
Relief Valve Spring (2-1/2, 3” plungers),purple
1
1015(note 1)
Poppet Assembly
1
960(note 2)
Air Bleed Valve Body
1
970(note 2)
Ball
1
980(note 2)
O-Ring
1
990(note 2)
Air Bleed Ball Seat
1
1000(note 2)
Spring
1
1005(note 2)
Air Bleed Body Seat
1
Note 1: Includes items 960, 970, 980, 990, 1000, 1005.
Note 2: Not sold separately. Must purchase item 1015 (Poppet Assembly).
6.2.4 CHECK VALVE PARTS
(see Figures 10-13)
The Pump Model Number is used to identify the
check valve parts.
The 4 & 5 digits identify the plunger size, digit 6
identifies the liquid end material.
4
5
6
MGH -
Digits
Codes for Digits 4 & 5
• Code 20 is a 1-1/4”(32mm) Plunger
• Code 28 is a 1-3/4”(45mm) Plunger
• Code 40 is a 2-1/2”(63mm) Plunger
• Code 48 is a 3”(75mm) Plunger
Codes for Digit 6
• Code 1 is 316SS, Code 2 is PVC, Code 5 is
Alloy 20