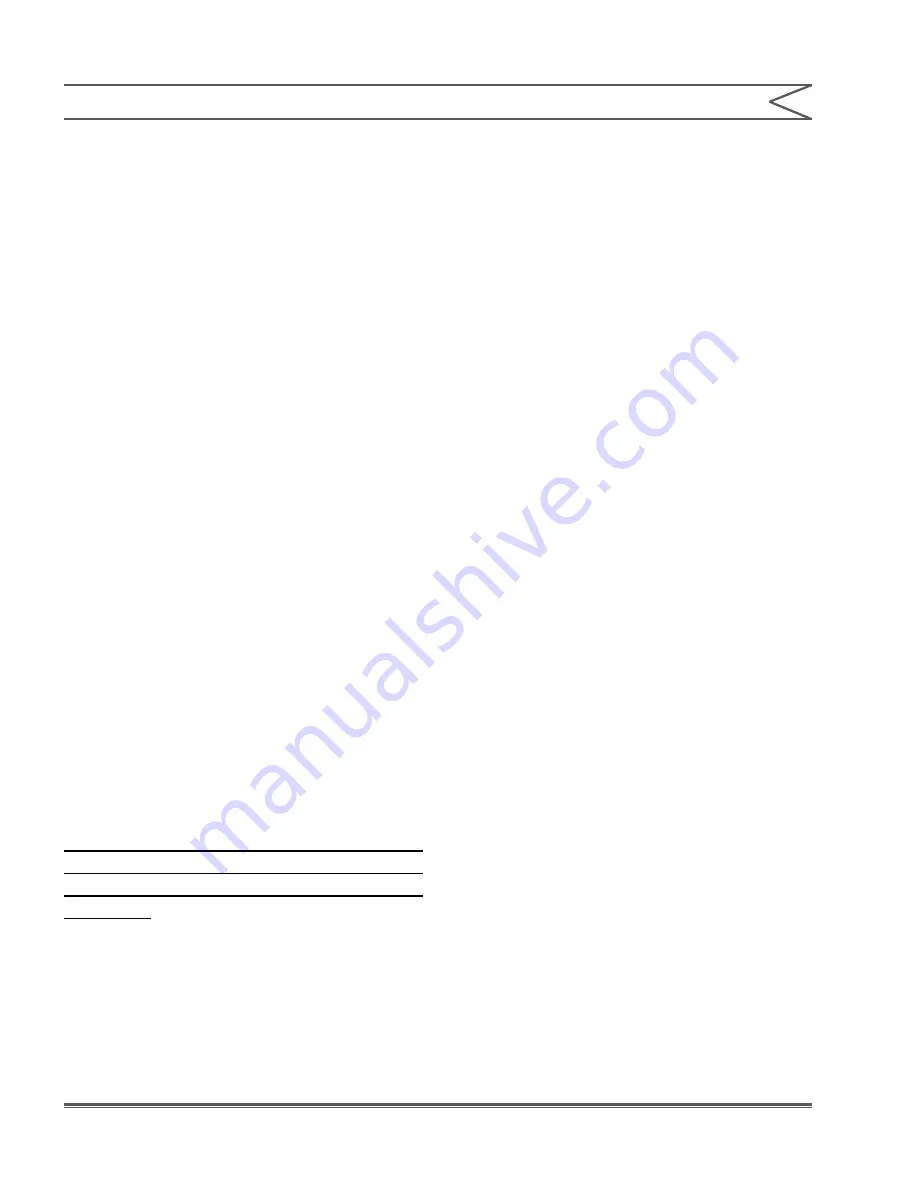
6
Instruction Manual
SECTION 2 - INSTALLATION
2.3.4 Electrical Equipment
1. Motors should be prepared in the manner
prescribed by their manufacturer. If information
is not available, dismount and store motors as
indicated in step 3 below.
2. Dismount electrical equipment (including
motors) from the pump.
3. For all electrical equipment, place packets of
Vapor Phase Corrosion Inhibitor (VPCI) inside of
the enclosure, then place the entire enclosure,
with additional packets, inside a plastic bag.
Seal the bag tightly closed. Contact Milton Roy
Service Department for recommended VPCI
materials.
2.4 MOUNTING
Support the pump firmly in a level position on a
solid, vibration- free foundation, preferably with
the base above floor level to protect the pump
from wash downs and to provide easier access
for service. Be sure to allow enough space around
the pump for easy access during maintenance
operations, pump adjustments, and/or oil filling or
draining procedures.
MILROYAL
®
G pumps are provided with mounting
holes to accommodate anchor bolts. Refer to
Figure 3
for mounting hole dimensions.
Some MILROYAL
®
G pumps are shipped with
motors dismounted. After anchoring pump in
position, install motor, referring to
Figure 5
.
To avoid damage to pump drive during
operation, make sure spring (360) provided with
pump is installed in worm shaft prior to motor
installation
. Pumps installed outdoors should be
protected by a shelter.
2.5 CONVENTION PROCEDURE
A MILROYAL
®
G pump can, in some cases, be
converted from one liquid end plunger size or
material of construction to another. For more
information on converting between different liquid
end models, please contact the Milton Roy factory
or your local authorized representative.
2.6 PIPING CONNECTIONS
2.6.1 NPSH Considerations
The MILROYAL
®
G HPD liquid end is far superior
to conventional diaphragm liquid ends for suction
lift and many other NPSH- critical applications.
In these demanding applications, the patented
diaphragm and refill mechanism give this liquid
end truly exceptional performance.
For NPSH apply a 3 psia limitation (instead of
9 psia) in evaluating applications for this liquid end.
Size piping to accommodate peak instantaneous
flow. Because of the reciprocating motion of
the pump diaphragm, pump delivery follows an
approximate sine curve with a peak instantaneous
flow equal to pi (3.14) times the average flow.
Therefore, piping must be designed for a flow
3.14 times the pump capacity; this means that a
pump rated for 100 gallons per hour (379 L/hr.)
requires piping sufficient for 3.14 x 100 gph, or
314 gph (1188 L/hr.).
To minimize viscous flow losses when handling
viscous liquids, it may be necessary to use suction
piping up to four times larger than the size of
the suction connection on the pump. If in doubt,
contact your nearest Milton Roy representative to
determine the necessary pipe size.