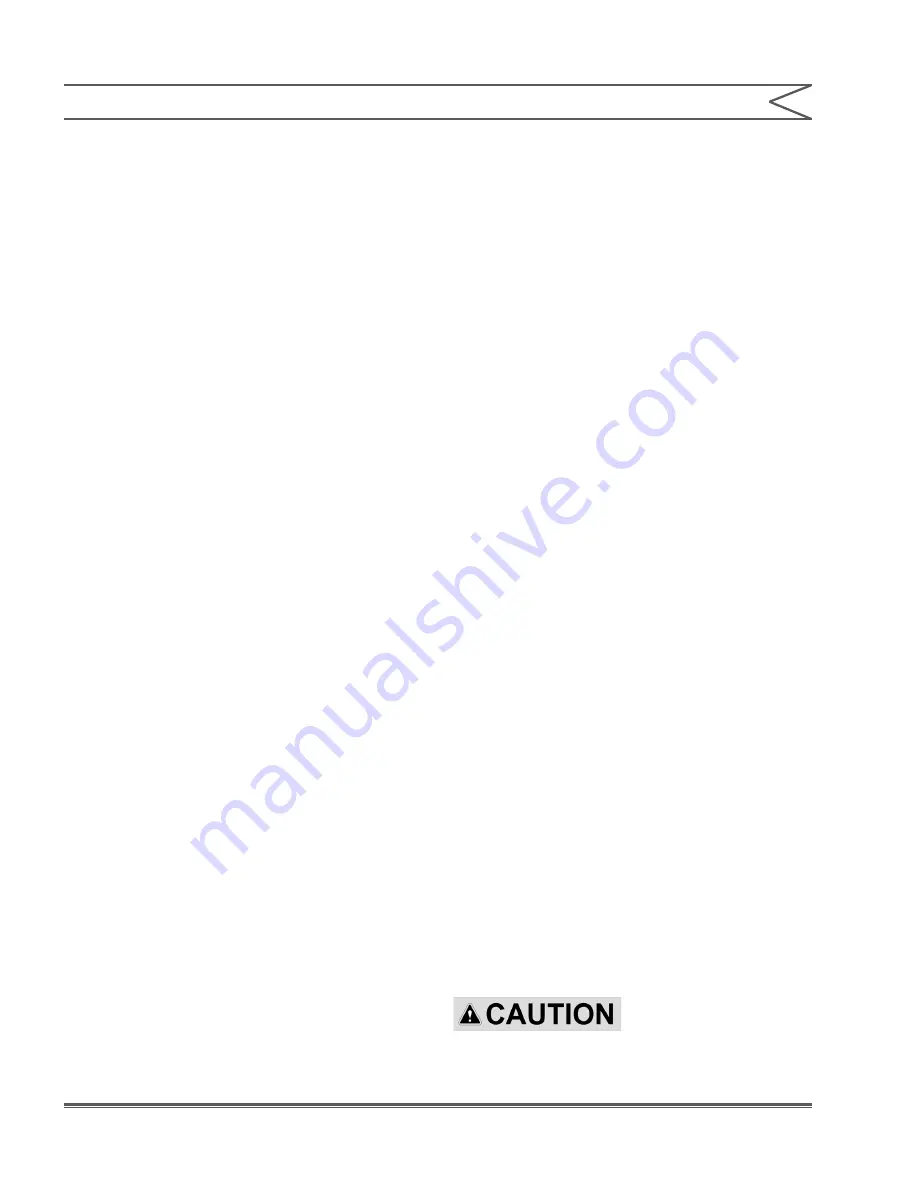
14
Instruction Manual
The operator should only activate the purge button
if some type of pump upset occurs such as the
above 4 examples. When activating the purge, only
press button for 2-3 seconds or until a stream of oil
flowing from the drain tube (640) is seen through
the sight glass (630). Immediately after activation
of the purge button, a temporary reduction in flow
will occur as the refill system replenishes oil lost
during the purge. However, the pump should return
to normal operation within 1 to 2 minutes after
activation of the purge button. If after that time, the
pump flow rate is still less than it should be, repeat
the purge operation and wait another 2 minutes.
If flow has still not resumed to expected levels,
consult the troubleshooting section of this manual.
3.4 MANUAL CAPACITY CONTROL
To adjust pump capacity on standard pumps
equipped with manual stroke adjustment, first
loosen the stroke locking screw located in
the pump side cover. Pump capacity is then
adjusted by turning the micrometer-type stroke
adjustment knob clockwise to decrease capacity or
counterclockwise to increase capacity as required.
The adjustment scale is marked in percent (%)
of full stroke, with calibration lines on the knob at
1% intervals. After adjusting the knob to the desired
capacity setting, hand tighten the stroke locking
screw to maintain the capacity setting.
SECTION 3 - OPERATION
3.5 FILLING PUMPING SYSTEM
For proper pump operation, it is especially important
that pump suction and discharge lines be free of
entrained air. To ensure this condition, operate the
pump without any discharge pressure and fill the
entire pumping system with liquid before starting
pressure tests. A simple method to assure priming
of the pump is to install a tee and a shut- OFF valve
at the discharge connection of the pump.
If the pump is idle for long periods, temperature
changes in the process liquid may produce air in
the system. To discharge the air, install a valve in
the discharge line which will allow the process liquid
to be pumped to a drain when starting the pump.
3.6 CAPACITY CALIBRATION
After the first 12 hours of operation, the pump
should be tested and calibrated to find the exact
pump capacity under specific operating conditions
and capacity settings for the specific fluid being
pumped. Typically, calibrating the pump at 100,
50, and 10 percent capacity settings is enough to
establish a pump performance curve throughout
the adjustment range.
The pump can be calibrated by measuring the
decrease in liquid level pumped from a calibrated
vessel. This method is recommended for hazardous
liquids because it eliminates operator contact
with the liquid. Milton Roy test-tube Calibration
Columns are available for convenient and accurate
calibration of any pump. The pump can also be
calibrated by collecting and measuring pumped
liquid at the pump discharge port in which case it
will be necessary to create discharge head at the
liquid takeoff point so that the pump will operate
properly.
(See Section 2 for recommended ways
to do this.)
THIS METHOD IS NOT
GENERALLY RECOMMENDED
AS IT MAY EXPOSE OPERATING PERSONNEL TO HAZARDOUS
LIQUIDS.