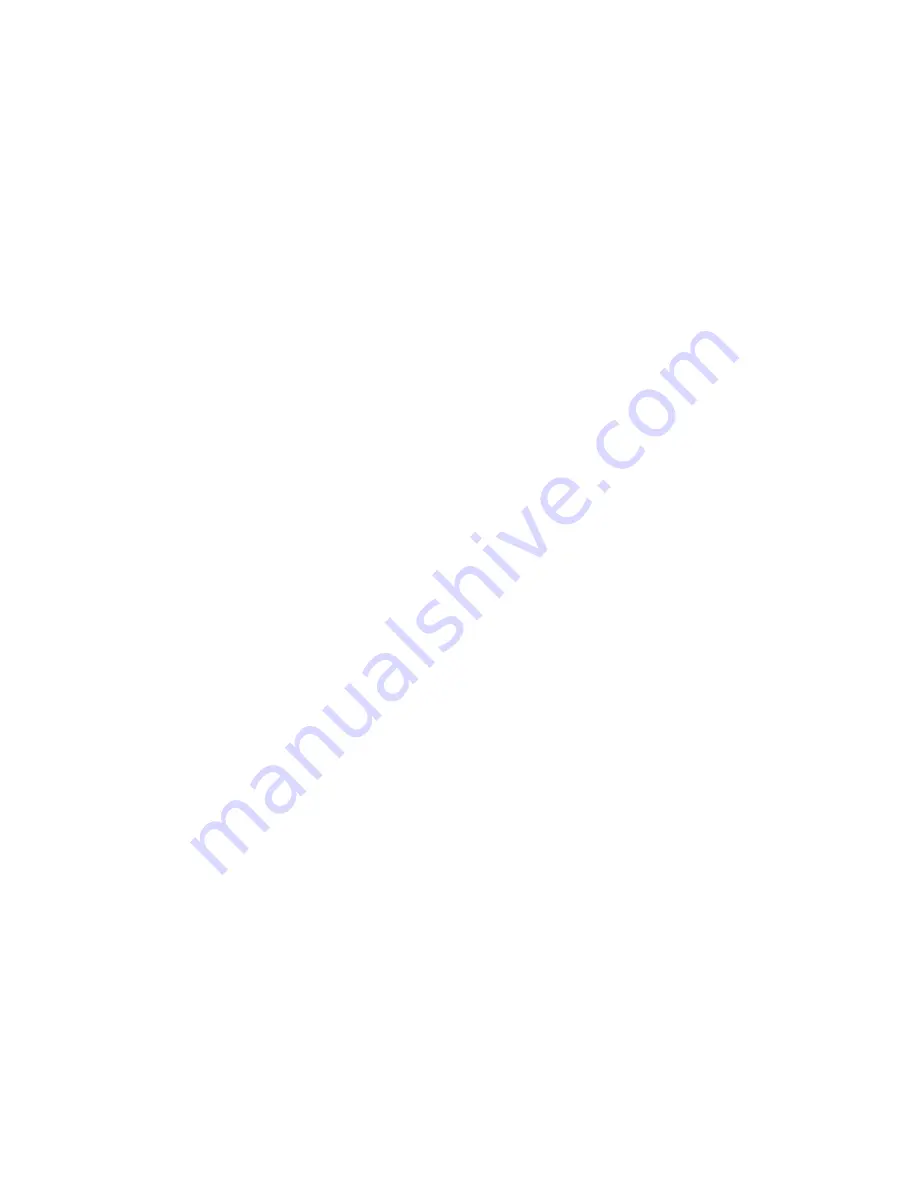
OM-257 675 Page 56
9-15. Touch Sensor Operation
The touch sensor feature allows the robot to locate a weldment using the wire feed system and the welding power source. Touch sensor operation is
turned on by a contact closure to the Peripheral receptacle RC25 sockets K and L (see Section 8-6). The closure is provided by the robot controller.
When touch sensor is turned on “LIVE WIRE” will appear on the power source displays. The voltage at the welding wire is 80 volts DC. Generally, when
the touch sensor is turned on, the robot is programmed to move slowly towards the workpiece. Once the workpiece is touched, the voltage sensing
circuit closes and sends a +24 volts DC signal to the robot controller. The touched signal will remain present until the touch sensor operation is turned off
by opening the contacts at the robot controller (see robot controller Owner’s Manual for specific touch sensor set-up information).
Some uses for the touch sensor operation are as follows:
1.
Locating welding seam
2.
Identify which part is in the fixture
3.
Identify what sized part is in the fixture
4.
Identify what parts are installed on a weldment
5.
Use for automatic tool point correction systems.
9-16. Stick Check Function
A stick check function removes welding wire that has stuck to the workpiece at the end of a weld. Automated systems should use this function to prevent
damaging automated equipment that could potentially move before the wire is released from a workpiece.
The welding power source performs a stop routine call sharp start at the end of a weld that usually prevents wire from sticking to the workpiece. If sharp
start does not remove the wire, the power source goes through a stick check routine. The stick check turns on the power source at a minimum amount of
output. If current flows, the welding wire must be shorted to the workpiece. The output rises to burn off the short and then current flow is checked again.
The stick check runs for approximately 250 ms and if it has not cleared the short during this time, ERR STUK will appears on the displays. The operator
must remove the welding wire from the workpiece manually and reset the power source (see Section 13-2).
Information to remember about stick check is the following:
1.
Some robots have stick check as part of their functions and it can be turned on or off in the robot. Typically, the robot stick check works fine;
however, only one stick check routine should be active, either the robot function or the power source function, not both.
2.
When programming the movement of the robot arm, be sure to leave enough time for the stick check to perform its function. The power source
stick check time is approximately 350 ms.
9-17. Arc Blow
Arc blow is the deflection of the welding arc from its normal path due to magnetic forces. This condition is usually encountered in direct current welding of
magnetic materials, such as iron and nickel. Arc blow can happen in alternating current welding under certain conditions, but these cases are rare and
the intensity of the arc blow is always less severe. Direct current flowing through the electrode and base metal will set up a magnetic field around the
electrode. This magnetic field tends to deflect the arc to the side at times, but usually the arc deflects either forward or backwards along the joint.
Back blow is encountered when welding toward the work cable connection on a workpiece near the end of a joint or into a corner. Forward blow is
encountered when welding away from the work cable connection on a workpiece at the start of a joint. In general, arc blow is the result of two basic
conditions:
1.
The change of current flow direction as it enters the work and is conducted toward the work cable.
2.
The asymmetric arrangement of magnetic material around the arc, a condition that normally exists when welding is performed near the end of
ferromagnetic materials.
Although arc blow cannot always be completely eliminated, it can be controlled or reduced to an acceptable level through knowledge of the two condi-
tions listed above.
4Except in cases where arc blow is unusually severe, certain steps can be taken to eliminate or reduces its severity. Some or all of the following steps
may be necessary:
1.
Place work cable connection as far as possible from joints to be welded.
2.
If back blow is the problem, place the work cable connection at the start of the joint to be welded and weld toward a heavy tack weld.
3.
If forward blow is the problem, place the work cable connection at the end of the joint to be welded.
4.
Position electrode angle so that arc force counteracts arc blow.
5.
Use the shortest possible arc that maintains good welding practices (this helps arc force to counteract arc blow).
6.
Reduce welding current if possible.
7.
Weld toward a heavy tack weld or runoff tab.
8.
Use the back step sequence of welding.
9.
Change to an AC welding operation which may require a change in electrode classification.
10.
Wrap the work cable around the workpiece in the direction that sets up a magnetic field to counteract the magnetic field causing the arc blow.
Содержание Auto-Axcess E Digital
Страница 6: ......
Страница 16: ...OM 257 675 Page 10...
Страница 18: ...OM 257 675 Page 12 Notes...
Страница 22: ...OM 257 675 Page 16 Notes...
Страница 26: ...OM 257 675 Page 20 Notes...
Страница 30: ...OM 257 675 Page 24 Notes...
Страница 37: ...General OM 257 675 Page 31 Notes...
Страница 98: ...Safety OM 257 675 Page 92 Notes...
Страница 115: ...Trouble OM 257 675 Page 109 Notes...
Страница 120: ...OM 257 675 Page 114 Figure 15 2 Circuit Diagram For Auto Axcess E 300 Digital Welding Power Source Part 2 Of 2...
Страница 121: ...Circuits OM 257 675 Page 115 257 679 A Part 2 Of 2...
Страница 122: ...OM 257 675 Page 116 Figure 15 3 Circuit Diagram For Auto Axcess E 450 Digital Welding Power Source Part 1 Of 2...
Страница 123: ...Circuits OM 257 675 Page 117 257 678 A Part 1 Of 2...
Страница 124: ...OM 257 675 Page 118 Figure 15 4 Circuit Diagram For Auto Axcess E 450 Digital Welding Power Source Part 2 Of 2...
Страница 125: ...Circuits OM 257 675 Page 119 257 678 A Part 2 Of 2...
Страница 126: ...OM 257 675 Page 120 Figure 15 5 Circuit Diagram For Auto Axcess E 675 Digital Welding Power Source Part 1 Of 2...
Страница 127: ...Circuits OM 257 675 Page 121 257 676 A Part 1 Of 2...
Страница 128: ...OM 257 675 Page 122 Figure 15 6 Circuit Diagram For Auto Axcess E 675 Digital Welding Power Source Part 2 Of 2...
Страница 129: ...Circuits OM 257 675 Page 123 257 676 A Part 2 Of 2...
Страница 130: ...OM 257 675 Page 124 Figure 15 7 Circuit Diagram For Axcess E Digital Module...
Страница 131: ...Circuits OM 257 675 Page 125 257 680 A...
Страница 132: ...OM 257 675 Page 126 Figure 15 8 Circuit Diagram For Motor And Digital I O Interface...
Страница 133: ...Circuits OM 257 675 Page 127 258 246 A...
Страница 143: ...E450 Parts OM 257 675 Page 137 Notes...
Страница 153: ...E675 Parts OM 257 675 Page 147 Notes...