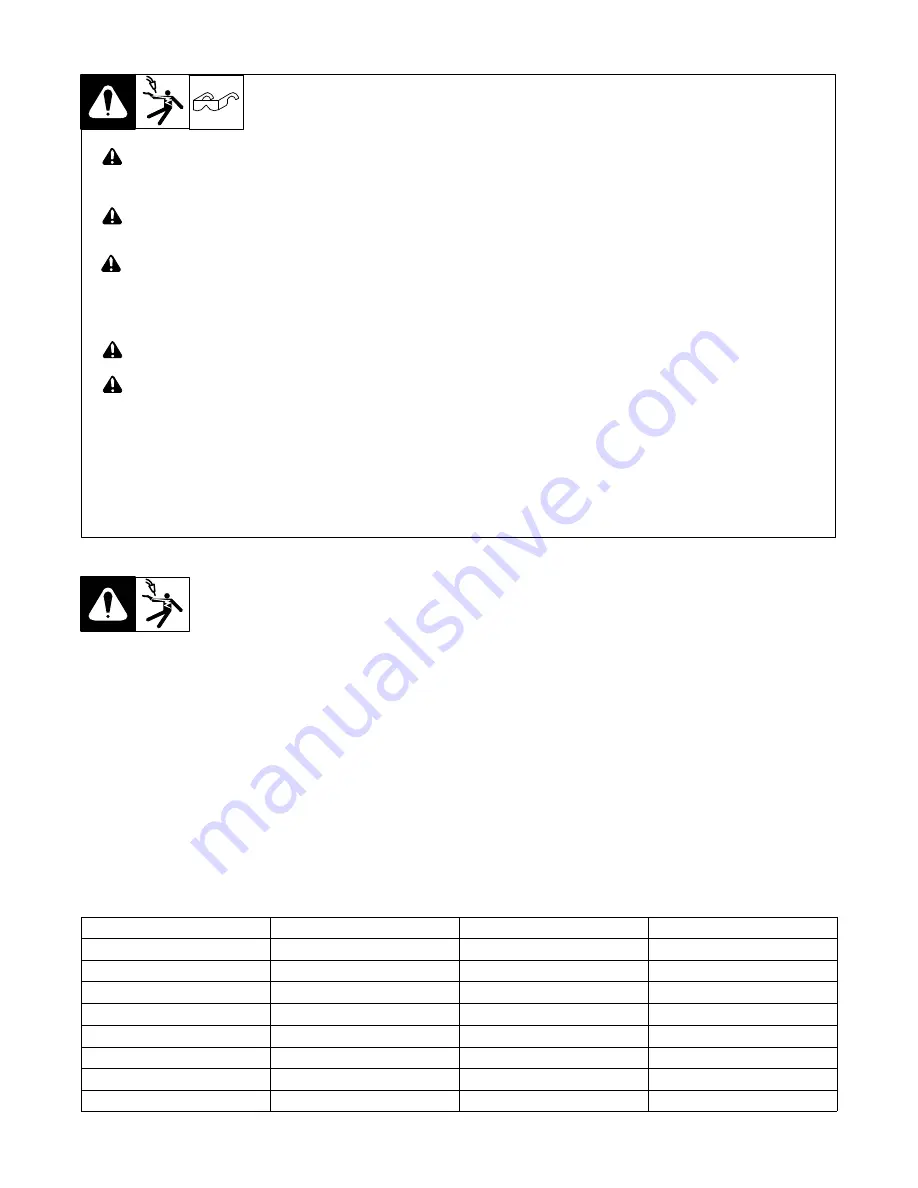
OM-231185 Page 23
Input5 2013
−
04
!
Turn Off welding power source, and
check voltage on input capacitors
according to Section 9-3 before
proceeding.
!
Installation must meet all National
and Local Codes
−
have only quali-
fied persons make this installation.
!
Disconnect and lockout/tagout
input power before connecting
input conductors from unit. Follow
established procedures regarding
the installation and removal of lock-
out/tagout devices.
!
Make input power connections to
the welding power source first.
!
Always connect green or
green/yellow conductor to supply
grounding terminal first, and never
to a line terminal.
See rating label on unit and check input volt-
age available at site.
1
Input Power Conductors (Customer
Supplied Cord)
Select size and length of conductors using
Section 5-9. Conductors must comply with
national, state, and local electrical codes. If
applicable, use lugs of proper amperage
capacity and correct hole size.
Welding Power Source Input Power
Connections
2
Strain Relief (Customer Supplied)
Install strain relief of proper size for unit and
input conductors. Route conductors (cord)
through strain relief and tighten screws.
3
Welding Power Source Grounding
Terminal
4
Green Or Green/Yellow Grounding
Conductor
Route green or green/yellow grounding
conductor through current transducer and
connect to welding power source grounding
terminal first.
5
Welding Power Source Line
Terminals
6
Input Conductors L1, L2, L3
Connect input conductors L1, L2, and L3 to
welding power source line terminals.
Reinstall side panel on welding power
source.
Disconnect Device Input Power
Connections
7
Disconnect Device (switch shown in
the OFF position)
8
Disconnect Device Grounding
Terminal
9
Disconnect Device Line Terminals
Connect green or green/yellow grounding
conductor to disconnect device grounding
terminal first.
Connect input conductors L1, L2, and L3 to
disconnect device line terminals.
10 Over-Current Protection
Select type and size of over-current protec-
tion using Section 5-9 (fused disconnect
switch shown).
Close and secure door on disconnect
device. Follow established lockout/tagout
procedures to put unit in service.
5-10. Connecting 3-Phase Input Power (Continued)
5-11. Touch Sensor Operation
The touch sensor feature allows the robot to locate a weldment using the wire feed system and welding power source. The weld output terminals pro-
vide a path for touch sensor voltage when this feature is turned on at the peripheral receptacle. Turning on touch sensor causes a DC voltage to be
present on the welding wire. When welding wire touches the weldment, the voltage sensing circuit closes, and a +24 volts DC output signal is sent to the
robot control indicating weldment detection. Touch sensor DC voltage on the welding wire is 80 volts DC. As soon as touch sensor turns on, WIRE LIVE
appears on the front panel display.
5-12. Remote Program Select
.
Remote Program Select is factory set to “On”. WaveWriter software is required to turn this function “Off”.
When Remote Program Select is On, a remote device or robot pendant may be used to select programs. When Off, program selection must be done
from the robot pendant.
5-13. Remote Program Setting
.
When Remote Program Select is “On”, program selection will be determined by remote input once a weld is initiated. Prior to welding, program
selection can be done in a normal manner from the welding power source front control panel.
See the following table for the remote program select binary code.
Program No.
Output A
Output B
Output C
1
Off
Off
Off
2
On
Off
Off
3
Off
On
Off
4
On
On
Off
5
Off
Off
On
6
On
Off
On
7
Off
On
On
8
On
On
On
Содержание Auto-Axcess 300 CE
Страница 27: ...OM 231185 Page 21 Notes...
Страница 58: ...OM 231185 Page 52 Figure 10 2 Circuit Diagram For Welding Power Source Part 2 Of 2...
Страница 59: ...OM 231185 Page 53 263 490 B Part 2 Of 2 RC1 PLG...
Страница 60: ...OM 231185 Page 54 Figure 10 3 Circuit Diagram For 72 Pin Robot Interface...
Страница 61: ...OM 231185 Page 55 219 266 D...
Страница 62: ...OM 231185 Page 56 Figure 10 4 Circuit Diagram For Peripheral Motor Interface...
Страница 63: ...OM 231185 Page 57 219 267 B...
Страница 72: ...Notes...
Страница 73: ...Notes...
Страница 74: ...Notes...