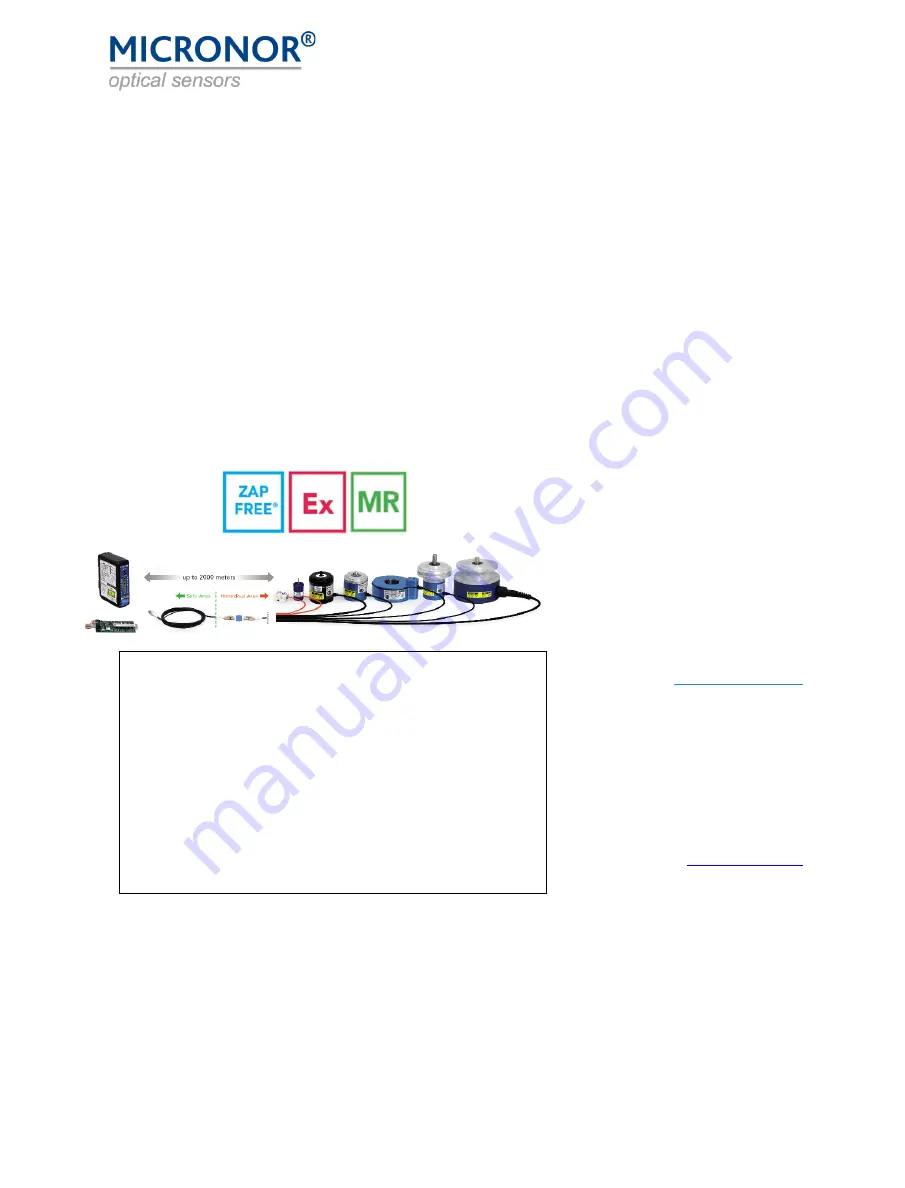
© COPYRIGHT 2018-2022, MICRONOR AG
REGENSDORF, SWITZERLAND
MR340-1
Fiber Optic Incremental Encoder
DIN Rail Mount Controller
Instruction Manual
Includes MR343 Linear Encoder
Application Information
Document: 98-0340-12
Revision: C
For Sales & Support in North America:
MICRONOR SENSORS, INC.
2085 Sperry Ave, Suite A-1
Ventura, CA 93003 USA
+1-805-389-6600
HQ and Worldwide Support:
MICRONOR AG
Pumpwerkstrasse 32
CH-8105 Regensdorf
Switzerland
+41-44-843-4020
Notice of Proprietary Rights
The design concepts and engineering details embodied in this manual, which are the property of MICRONOR AG,
are to be maintained in strict confidence; no element or detail of this manual is to be spuriously used, nor disclosed,
without the express written permission of MICRONOR AG. All rights are reserved. No part of this publication may
be reproduced, stored in a retrieval system, or transmitted in any form or by any means, electronic, mechanical,
photocopying, recording, or otherwise, without prior written permission from MICRONOR AG.
IMPORTANT NOTE
The MR340-1 Controller is a rebranding, part number change only
of the original MR302-1 DIN Controller. Any references to MR302-1
are applicable to the MR340-1 and vice versa. In addition, the former
MR303 Linear Encoder is now the MR343, and the former MR304
Mini Rotary Encoder is now the MR341.
The core dual wavelength 850nm/980nm optical technology of the
MR302 series replaces the 850nm/1300nm technology of the earlier
MR320 series, becoming the MR340 series. For more information on
the MR340 series Controller and Encoders and their compatibility
with earlier models, please consult Application Note AN127.