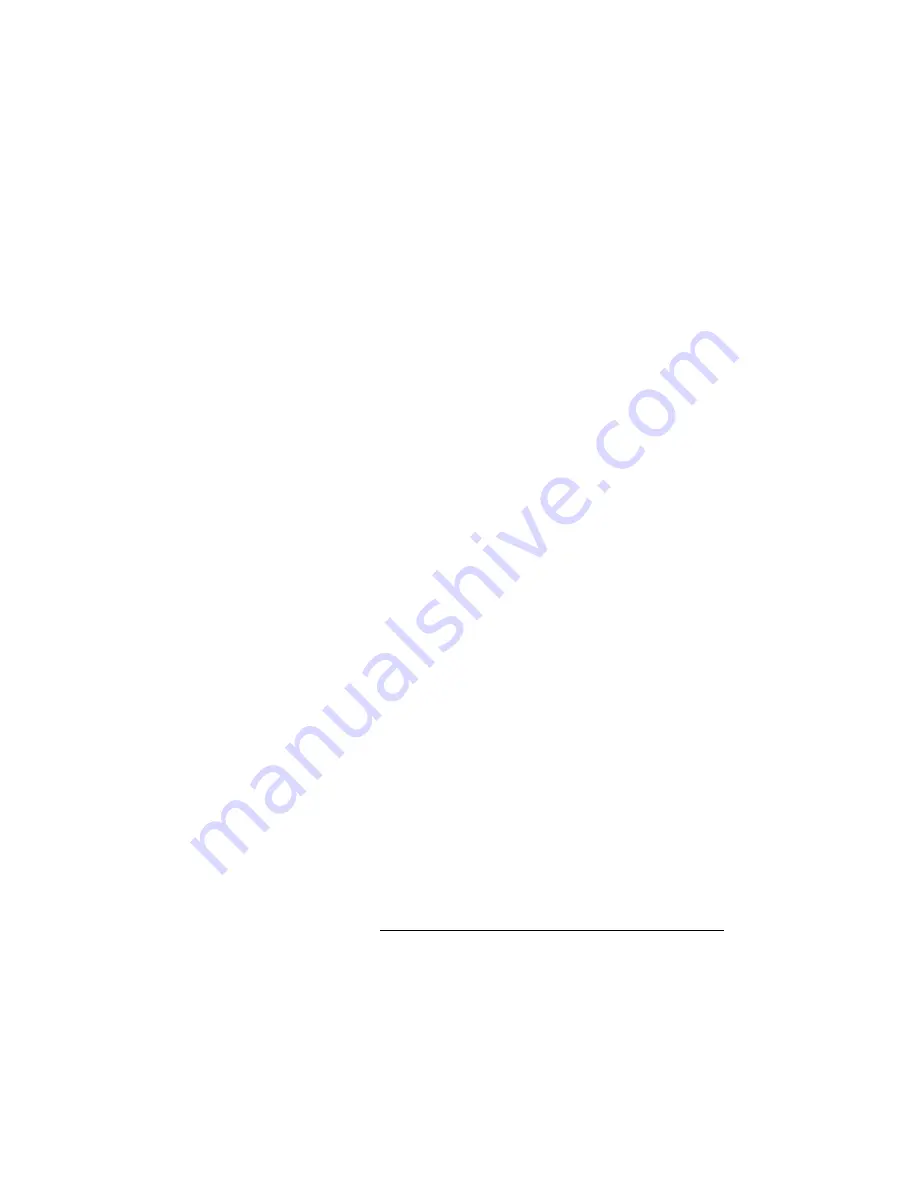
a reference voltage of 12.1V and a reference of –1.2V are gener-
ated.
An
I/O-expansion
is needed to obtain the I/O for the processor.
A SIPO (Serial In Parallel Out) shift register is used. The outputs
of this register control three magnet valves, and a miniature air
compressor, beeper, step motor (step motor inhibit signal) and
dual-color LED. Note: The LED is currently not used, except for
development tests.
3.
Stepper Motor Driver.
Refer to Schematic Diagrams 1 and 4
(Top Level and Stepper Motor Driver.
The Ericcson PBD3517N
is used
as the stepper motor driver. The motor is run in half step
mode to obtain an optimum of force and speed. The half step re-
duces the potential problems of resonance (increased noise for
system at certain motor speeds) in the system. The driver is con-
trolled by the signals
STEP_INHIBIT-,
STEP_DIR, STEPB-
and
STEP_CNT
. These signals have the following function:
STEP_INHIBIT-:
‘L’ = power down, ‘H’ = active
STEP_DIR:
Direction of rotation
STEPB-:
Motor speed – frequency from UARTs 16-bits timer
STEP_CNT:
Counting pulses to measure motor movement
There are three
magnet valves
that are controlled via the SIPO
shift register. The coils are driven by 24 V, with grounding via a
ULN2003 Darlington driver output. These outputs have internal
protection diodes that prevent the ULN2003 from the back volt-
age induced by the coil of the magnet valves when valve is re-
leased.
The miniature
air compressor
used for leak- and overpressure
tests is driven by three ULN2003 Darlington driver outputs in
parallel. Supply voltage to compressor is 24 V. The outputs are
internally protected against back voltages from inductive loads.
A
beeper
with built-in oscillator is driven by a ULN2003 Dar-
lington driver output, which is controlled by the shift register.
The beeper voltage is 24V. In case a lower volume is desired, a
serial resistor is prepared for and may be fitted on the board. The
beeper is controlled with the signal BEEPER.
From the
Power
supply, the QA-1290 board gets +5V and
+24V. From these the rest of the needed voltages are generated
on the QA-1290 board. The following voltages are present in the
system:
Voltage
Generated from
Description
+24
External Supply
Regulated 24V in
+15
+24
Local +15V analogue
+12
+24
+12V analogue for QA-90
-12
+12
-12V analogue for QA-90
+5A
+24
Local +5V analogue
-5A
+5
Local -5V analogue
8-3
Содержание QA-1290
Страница 1: ...QA 1290 User Service Manual 1 66 Firmware and higher QA 1290 NIBP Analyzer P N 17525 V 1 66...
Страница 6: ...This page intentionally left blank vi...
Страница 10: ...17520 User Manual QA 1290 P N 17525 Tubing Kit P N 17515 1 4...
Страница 30: ...This page intentionally left blank 4 8...
Страница 36: ...This page intentionally left blank 5 6...
Страница 51: ...Appendix A Tubing Kit Components A 1...
Страница 52: ...This page intentionally left blank B 2...
Страница 54: ...B 2...
Страница 55: ...B 3...
Страница 56: ...B 4...
Страница 57: ...B 5...
Страница 58: ...B 6...
Страница 59: ...B 7...
Страница 60: ...B 8...
Страница 61: ...B 9...
Страница 62: ...This page intentionally left blank B 10...