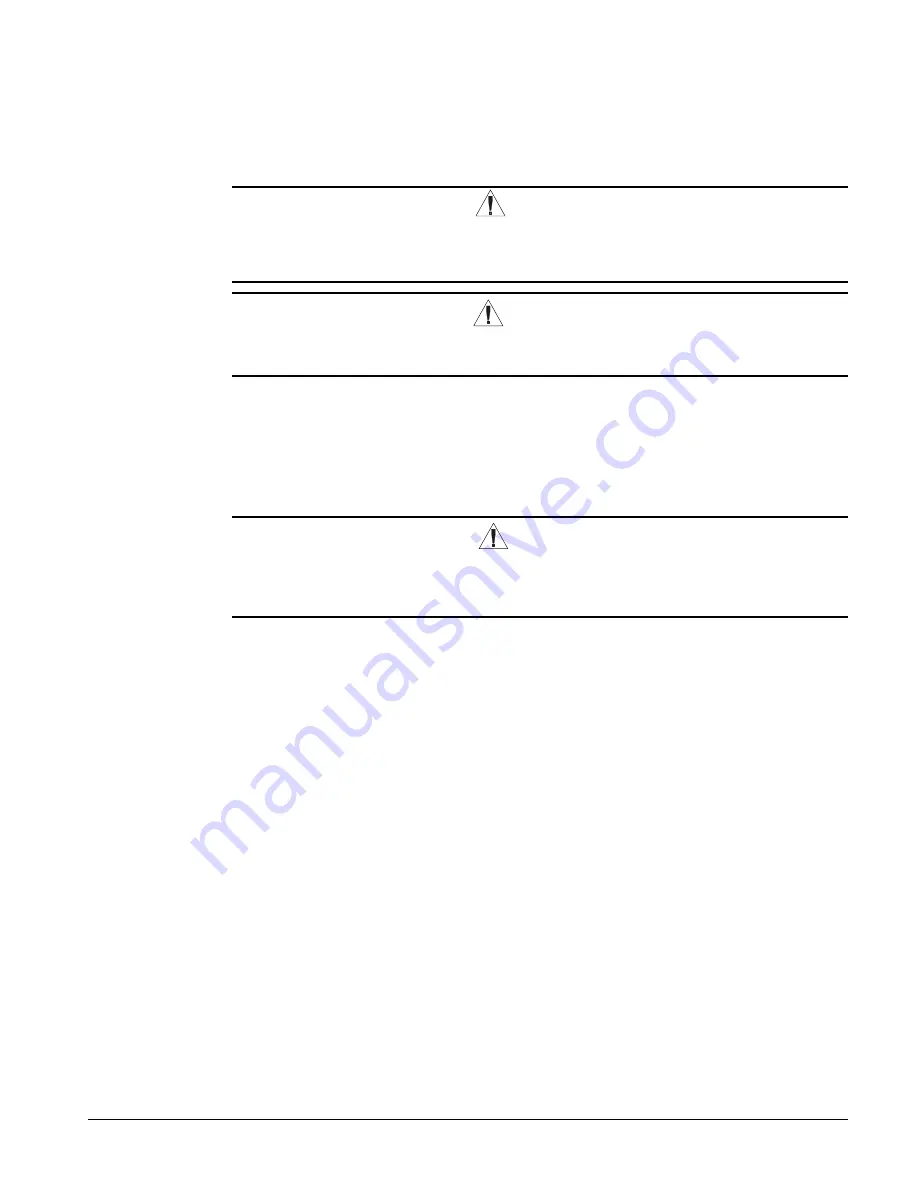
IMM AGS-2
75
The switch has automatic reset but is locked out by the MicroTech II control, which must be
reset through the software. A gauge can be put across the switch to actually measure the
pressure drop. The normal pressure drop is 5 to 6 psi. Change the filter at 15 psi.
Electrical Terminals
DANGER
Electric equipment can cause electric shock with a risk of severe personal injury or
death. Turn off, lock out and tag all power before continuing with following service.
Panels can have more than one power source.
CAUTION
Periodically check electrical terminals for tightness and tighten as required. Always
use a back-up wrench when tightening electrical terminals.
Condensers
The condensers are air-cooled and constructed of 3/8" (9.5mm) OD internally finned copper
tubes bonded in a staggered pattern into louvered aluminum fins. No maintenance is
ordinarily required except the routine removal of dirt and debris from the outside surface of
the fins. McQuay recommends the use of non-caustic, non-acidic, foaming coil cleaners
available at most air conditioning supply outlets. Flush the coil from the inside out.
WARNING
Use caution when applying coil cleaners. They can contain potentially harmful
chemicals. Wear breathing apparatus and protective clothing. Thoroughly rinse all
surfaces to remove any cleaner residue. Do not damage the fins during cleaning.
If the service technician has reason to believe that the refrigerant circuit contains
noncondensables, recovery of the noncondensables will be required, strictly following
Clean Air Act regulations governing refrigerant discharge to the atmosphere. The service
Schrader valves are located on both vertical coil headers on both sides of the unit at the
control box end of the coil. Access panels are located at the end of the condenser coil
directly behind the control panel. Recover the noncondensables with the unit off, after
shutdown of 15 minutes or longer, to allow air to collect at the top of the coil. Restart and
run the unit for a brief period. If necessary, shut the unit off and repeat the procedure.
Follow accepted environmentally sound practices when removing refrigerant from the unit.
Liquid Line Sight Glass
Observe the refrigerant sight glasses (one per circuit) weekly. A clear glass of liquid
indicates that there is adequate refrigerant charge in the system to provide proper feed
through the expansion valve. Bubbling refrigerant in the liquid line sight glass, during
stable run conditions, may indicate that there can be an electronic expansion valve (EXV)
problem since the EXV regulates liquid subcooling. Refrigerant gas flashing in the sight
glass could also indicate an excessive pressure drop in the liquid line, possibly due to a
clogged filter-drier or a restriction elsewhere in the liquid line (see page 25 for maximum
allowable pressure drops).
An element inside the sight glass indicates the moisture condition corresponding to a given
element color. If the sight glass does not indicate a dry condition after about 12 hours of
operation, the circuit should be pumped down and the filter-drier changed. An oil acid test
is also recommended.