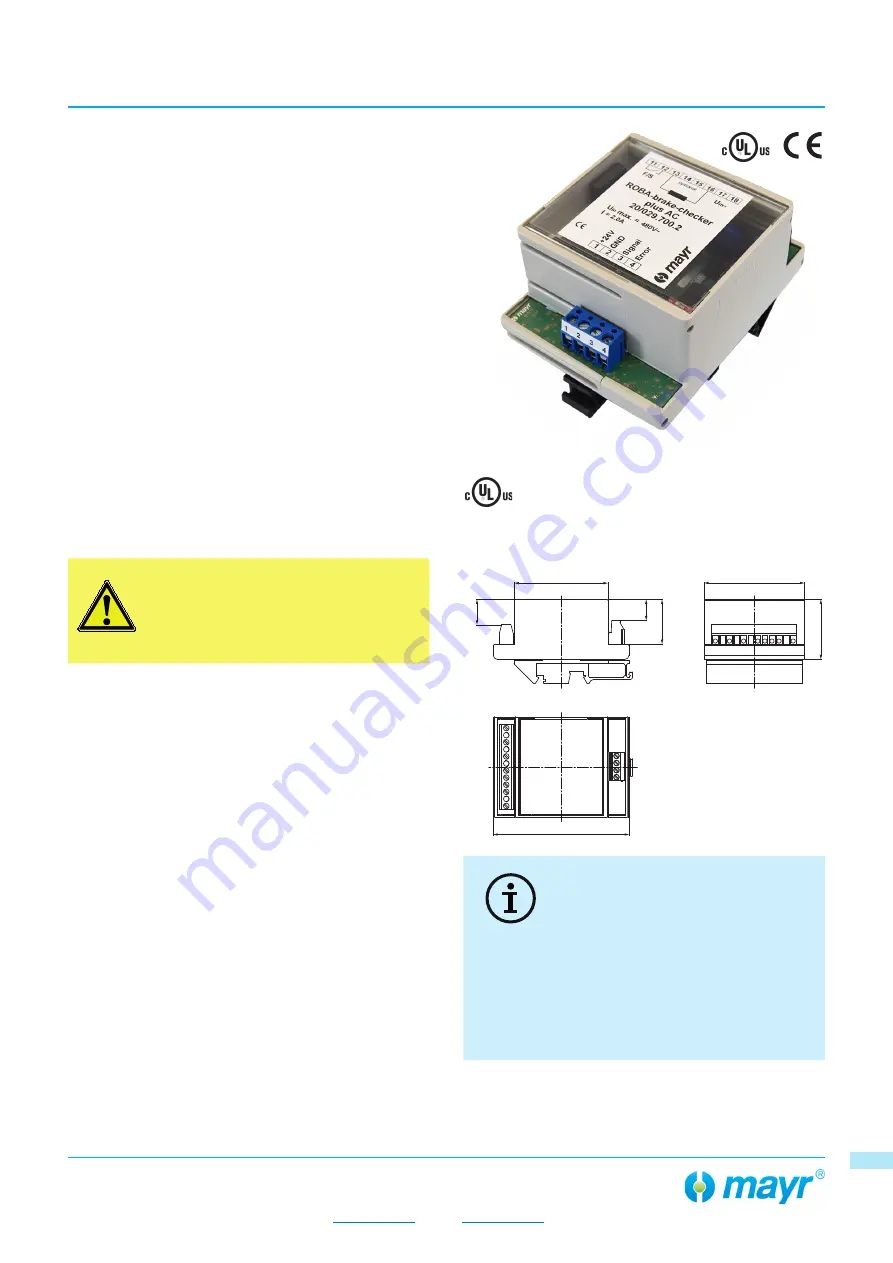
Installation and Operational Instructions for
ROBA
®
-brake-checker plus AC Type 029.700.2
(B.0297002.EN)
your reliable partner
26/06/2019 HH/GF
Page 3 of 10
Chr. Mayr GmbH + Co. KG
Eichenstraße 1, D-87665 Mauerstetten, Germany
Tel.: +49 8341 804-0, Fax: +49 8341 804-421
www.mayr.com
, E-Mail:
33
Function
The ROBA
®
-brake-checker plus AC monitoring module is
intended for use with an input voltage of 200 to 480 VAC.
The monitoring module supplies the connected brakes and
regulates to a permanently programmed overexcitation
voltage. After the overexcitation time ends, it regulates to
the permanently programmed holding voltage.
The overexcitation time is set automatically.
The monitoring module monitors the movement of the arma-
ture disk and emits the determined switching condition via
control terminal 3 (signal output).
Critical conditions (line breakages, wear) can be recognized
and the respective signal can be emitted via control terminal
4 (error output).
The movement detection feature of the armature disk is
based on the detection of electromagnetic changes in
the brake. If, due to unfavourable external influences, the
secured detection cannot be ensured, it is possible that the
signal and error outputs do not correspond to the expected
state (plausibility).
CAUTION
The ROBA
®
-brake-checker cannot be used
in all applications (e.g. when operating
noise-damped brakes, it cannot be used
without additional measures). The product’s
suitability should be checked before use.
Application
ROBA
®
-brake-checker plus AC monitoring modules are
used to connect permitted ROBA
®
-stop safety brakes to AC
voltage.
Motion monitoring of the armature disk for released ROBA-
stop
®
safety brakes is possible.
Monitoring module ROBA
®
-brake-checker plus AC
• Consistently controlled output voltage
• Consumer operation with overexcitation or power reduc-
tion
• Input voltage: 200 – 480 VAC
• Supply voltage with 50 or 60 Hz
• Max. output current I
RMS
: 2 A
• Sensorless and contactless detection of switching
statuses
• Motion recognition of the brake (release and drop-out
recognition of the armature disk)
• Preventative function monitoring (wear recognition and
error recognition, functional reserve)
• Continuous drop-out recognition
• Simple installation or retrofitting
• Electrical isolation on the output channels
66
14.8
31.5
42.3
15
96
17.8
70.8
Dimensions
(mm)
The UL information applies only when the UL mark is
printed onto the product label
.
The use of the ROBA
®
-brake-checker in
combination with brakes of other manuf-
acturers is not intended and expressly not
approved by
mayr
®
power transmission.
In these cases, operation is at your
own risk
, the guarantee and service
and support provided by
mayr
®
power
transmission no longer apply.
33