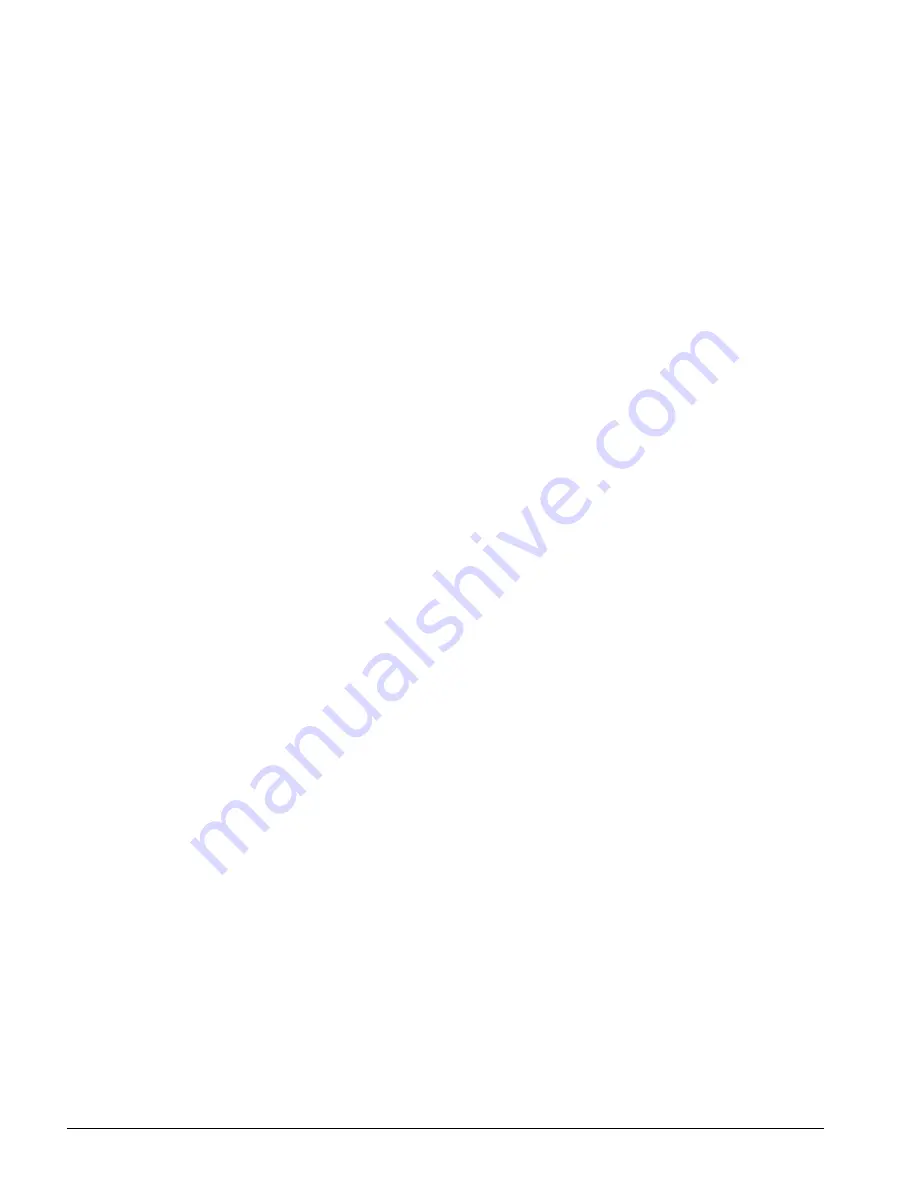
IMPULSE®•G+/VG+ Series 4 Profinet Installation Manual - August 2014
29
8. Communication
This section describes the PROFINET IO messaging used in communication with the drive.
For detailed information on PROFINET IO communication, refer to the PROFINET specification
Application Layer protocol for decentralized periphery and distributed automation v2.0 available at
www.profibus.com.
Introduction to PROFINET IO
PROFINET IO is a fieldbus protocol that enables communication between programmable controllers
and distributed field devices in an Ethernet network. The protocol classifies devices into IO
controllers, IO supervisors, and IO devices, which have a specific collection of services.
PROFINET IO uses three different communication channels to exchange data. The standard UDP/
IP and TCP/IP channel is used for parameterization and configuration of devices and for acyclic
operations. The Real Time (RT) channel is used for cyclic data transfer and alarms. The third
channel, Isochronous Real Time (IRT) channel, is used e.g. in motion control applications (not
implemented in SI-EP3).
PROFINET IO devices are structured in slots and sub-slots, which can contain modules and sub-
modules correspondingly. Devices can have almost any number of slots and sub-slots and they can
be virtual or real. Device specific data is represented in slot 0; module and sub-module specific data
in subsequent slots and sub-slots.
One of the benefits of PROFINET IO is the diagnostics and alarm mechanism. Every module and
sub-module provide alarm data to the IO controller using the cyclic channel. Diagnostic data can be
read non-cyclically from the device by using record data.
Properties and services of a PROFINET IO device are described in a GSD file that is written in
General Station Description Markup Language (GSDML). The GSD file describes the device specific
modules and the method of assigning modules and sub-modules to predefined slots and sub-slots.
PROFINET IO in SI-EP3
The decision to use either the PROFIdrive control and status words or the Magnetek-specific control
and status words is done in a hardware configuration tool (customer-supplied). The default value is
the Magnetek-specific format.
SI-EP3 uses slots 0 and 1. Slot 0 does not have any sub-slots and the attached device access point
(DAP) module represents the device. Other functional modules and sub-modules described in the
GSD file can be assigned to slot 1 and its sub-slots.
•
Slot 0 = Device access point (DAP)
•
Slot 1, sub-slot 1 = Standard telegram 1, Standard telegram 1 + 5 configurable inputs, outputs,
Forty byte IO with 5 configurable input, outputs
The services provided by the SI-EP3 option can be defined using the F07-XX parameters in the drive
or by using a configuration tool. To define the service using the F07-XX parameters, set the
parameter to a value other than 0.
If all F07-XX parameters are set to 0, the value from the configuration tool will be used.
The SI-EP3 option provides the following services:
•
Cyclic messaging in PROFIdrive or Magnetek-specific mode
•
Acyclic parameter access mechanism
•
Identification & Maintenance functions (I&M0)
•
PROFIdrive parameters