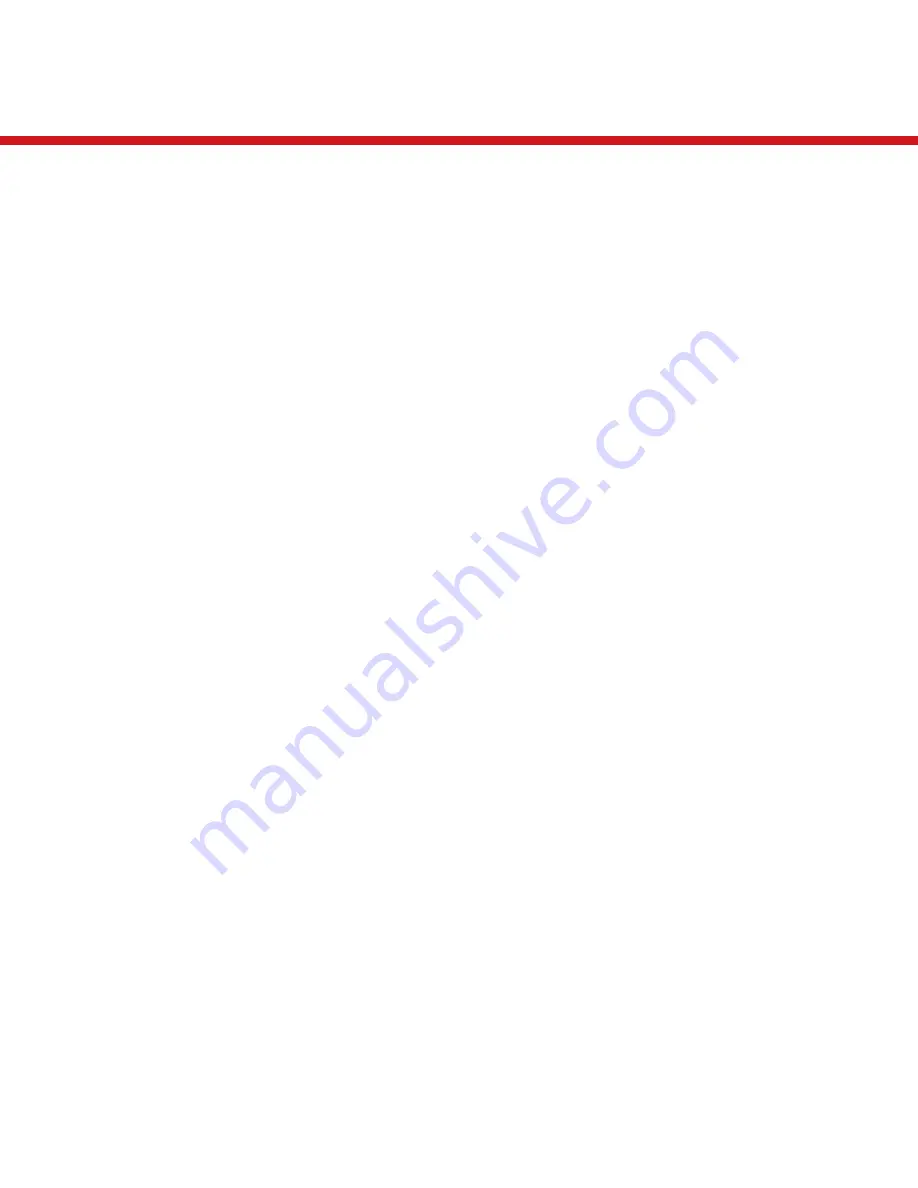
36
35-127 M
Safety
Lightning Storm
When lightning is striking in the vicinity of the crane, the operator should never attempt the following
procedures:
• Getting into the operator’s cab or attempting to get onto the carrier, superstructure or boom
assembly�
• If on the machine, do not try to get off the machine�
If you are in the operator’s cab during an electrical storm, stay in the cab� If you are on the ground during
an electrical storm, stay away from the vicinity of the machine�
Содержание 35-127 M
Страница 1: ...OPERATORS MANUAL LOAD KING 35 127 M C1046093 REV A FEBRUARY 09 2022...
Страница 2: ...PAGE INTENTIONALLY LEFT BLANK...
Страница 48: ...PAGE INTENTIONALLY LEFT BLANK...
Страница 63: ...63 Description Of Machine and Controls Operator Controls 5 3 2 4 8 7 1 9 10 6...
Страница 79: ...79 REPAIRS ADJUSTMENTS REMARKS ITEM REQUIREMENT DATE...
Страница 96: ...PAGE INTENTIONALLY LEFT BLANK...
Страница 109: ...109 Boom Angle Placards CAUTION Do not extend jib into this area unless boom is fully retracted...
Страница 124: ...PAGE INTENTIONALLY LEFT BLANK...
Страница 131: ...131 35 127 M Master Lube Chart 1 2 5 11 12 3 4 6 8 9 7...
Страница 132: ...132 35 127 M Maintenance...
Страница 150: ...150 35 127 M Maintenance...
Страница 172: ...PAGE INTENTIONALLY BLANK...
Страница 176: ...PAGE INTENTIONALLY LEFT BLANK...
Страница 201: ...201 Repairs Adjustments Remarks Log ITEM REQUIREMENT DATE...
Страница 202: ...PAGE INTENTIONALLY LEFT BLANK...
Страница 209: ...209 Torque Specs SAE Metric...
Страница 210: ...210 35 127 M Appendix...
Страница 212: ...PAGE INTENTIONALLY LEFT BLANK...
Страница 213: ...Notes...
Страница 216: ...35 127 M Operator Manual...