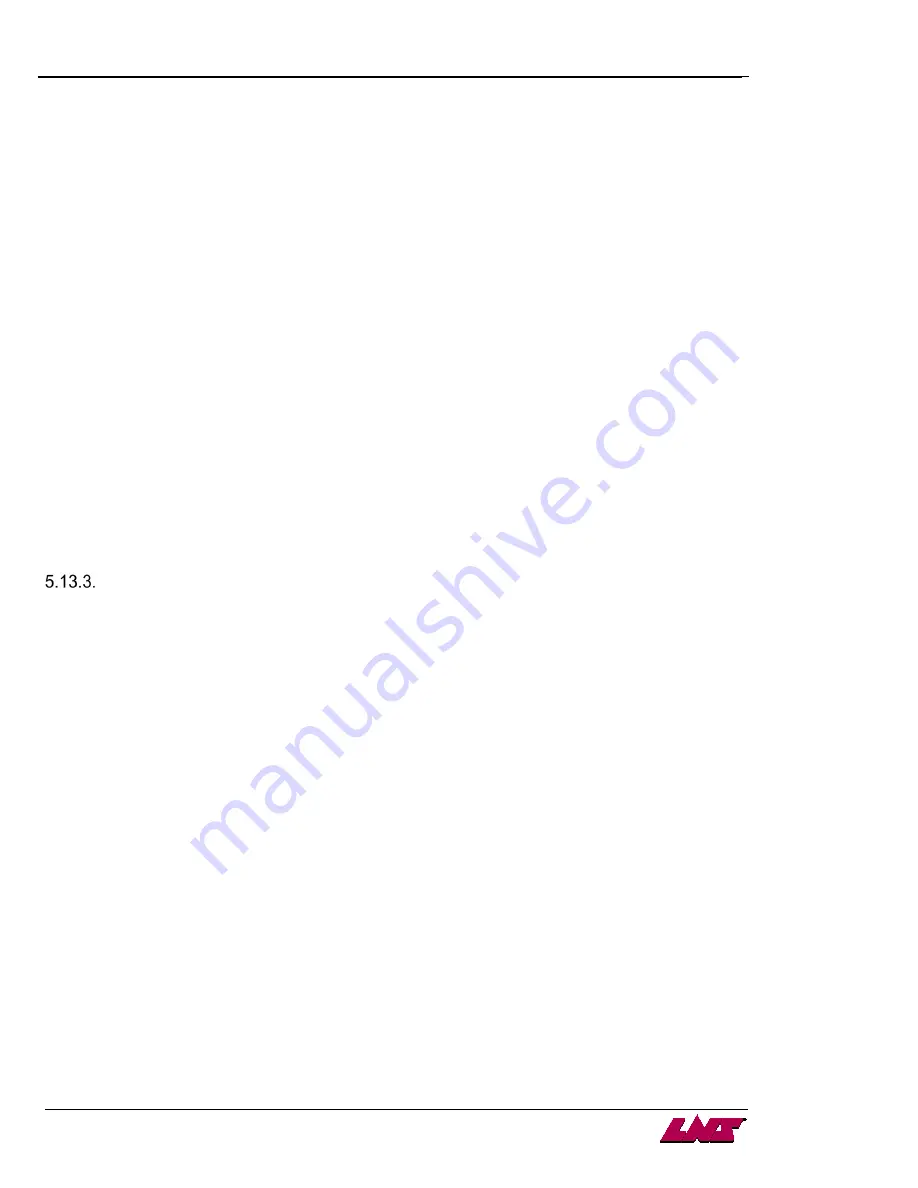
ELECTRICAL EQUIPMENT
SERVICE MANUAL –ALPHA SL 65S
c) R2 loading cycle completed signal relay
When the pusher is stopped based on servo encoder setup, it will energize Relay R2. Generally this signal is for confirming
the bar stock hit the stopper during feeding so that the lathe chuck should closed accordingly.
d) R3 end of bar signal relay
When the pusher reaches END OF BAR position during feeding, relay R3 energizes. This signal is used to indicate that the
rest bar stock length is not long enough to machine a complete part according to part length setup value.
Refer to operation parameter P06 and service parameter MODE 11, 12, 13 for further information.
e) R4 automatic mode relay
This signal is present as soon as the bar feed system is in automatic cycle (Auto Ready + Auto Start).
f) R5 INCHING relay
This relay energizes under
circumstances below:
Index
Beginning
End
1
The moment SHORT pusher
leaves the home position for
proceeding FIRST FEED.
The moment that SHORT
pusher returns to the home
position.
2
The moment when the LONG
pusher leaves the home
position for TOP CUT.
The moment the LONG pusher
stopped after arriving at TOP
CUT position.
3
The moment when the lathe
chuck opens during machining.
The moment the LONG pusher
is stopped after it has fed the
part length.
Refer to service parameter MODE 16 for more information.
RECAPITULATION OF SAFETY INSTRUCTIONS RELATED TO THE INTERFACE
•
The lathe foot switch for opening the lathe clamping device should not be operational during the automatic cycle of the
lathe.
•
The lathe pedal should not be operational as long as the feeding pusher feed command signal is present.
•
Whenever possible, it is advisable to interlock lock the manual command for opening the lathe clamping device while
the feeding pusher command signal is on.
•
If the lathe is in the Emergency Stop mode, the bar feed system must also be under the Emergency Stop mode, and
vice-versa.
•
If the bar feed system generates an alarm, the lathe must go into alarm mode. The feeding pusher feed command
signal must go off, the spindle axis and rotation must stop.
Содержание ALPHA SL65 S
Страница 5: ...GENERAL SERVICE MANUAL ALPHA SL 65S...
Страница 29: ...PROCEDURES SERVICE MANUAL ALPHA SL 65S...
Страница 37: ...MECHANICAL EQUIPMENT SERVICE MANUAL ALPHA SL 65S...
Страница 41: ...PNEUMATIC EQUIPMENT SERVICE MANUAL ALPHA SL 65S...
Страница 59: ...ELECTRICAL EQUIPMENT SERVICE MANUAL ALPHA SL 65S...
Страница 87: ...MAINTENANCE SERVICE MANUAL ALPHA SL 65S...
Страница 89: ...TECHNICAL CHARACTERISTICS SERVICE MANUAL ALPHA SL 65S...
Страница 91: ...DISPOSAL SERVICE MANUAL ALPHA SL 65S...
Страница 101: ...TROUBLESHOOTING SERVICE MANUAL ALPHA SL 65S SEQUENCE LISTING...
Страница 102: ...TROUBLESHOOTING SERVICE MANUAL ALPHA SL 65S...
Страница 116: ...TROUBLESHOOTING SERVICE MANUAL ALPHA SL 65S PLC INPUTS OUTPUTS...
Страница 117: ...TROUBLESHOOTING SERVICE MANUAL ALPHA SL 65S...
Страница 121: ...TROUBLESHOOTING 121 SERVICE MANUAL ALPHA SL 65S...
Страница 123: ...APPENDICES 123 SERVICE MANUAL ALPHA SL 65S WIRING DIAGRAM BSL65 A8...
Страница 124: ...124 APPENDICES SERVICE MANUAL ALPHA SL 65S...
Страница 125: ...APPENDICES 125 SERVICE MANUAL ALPHA SL 65S...
Страница 126: ...126 APPENDICES SERVICE MANUAL ALPHA SL 65S...
Страница 127: ...APPENDICES 127 SERVICE MANUAL ALPHA SL 65S...
Страница 128: ...128 APPENDICES SERVICE MANUAL ALPHA SL 65S PNEUMATIC DIAGRAM...