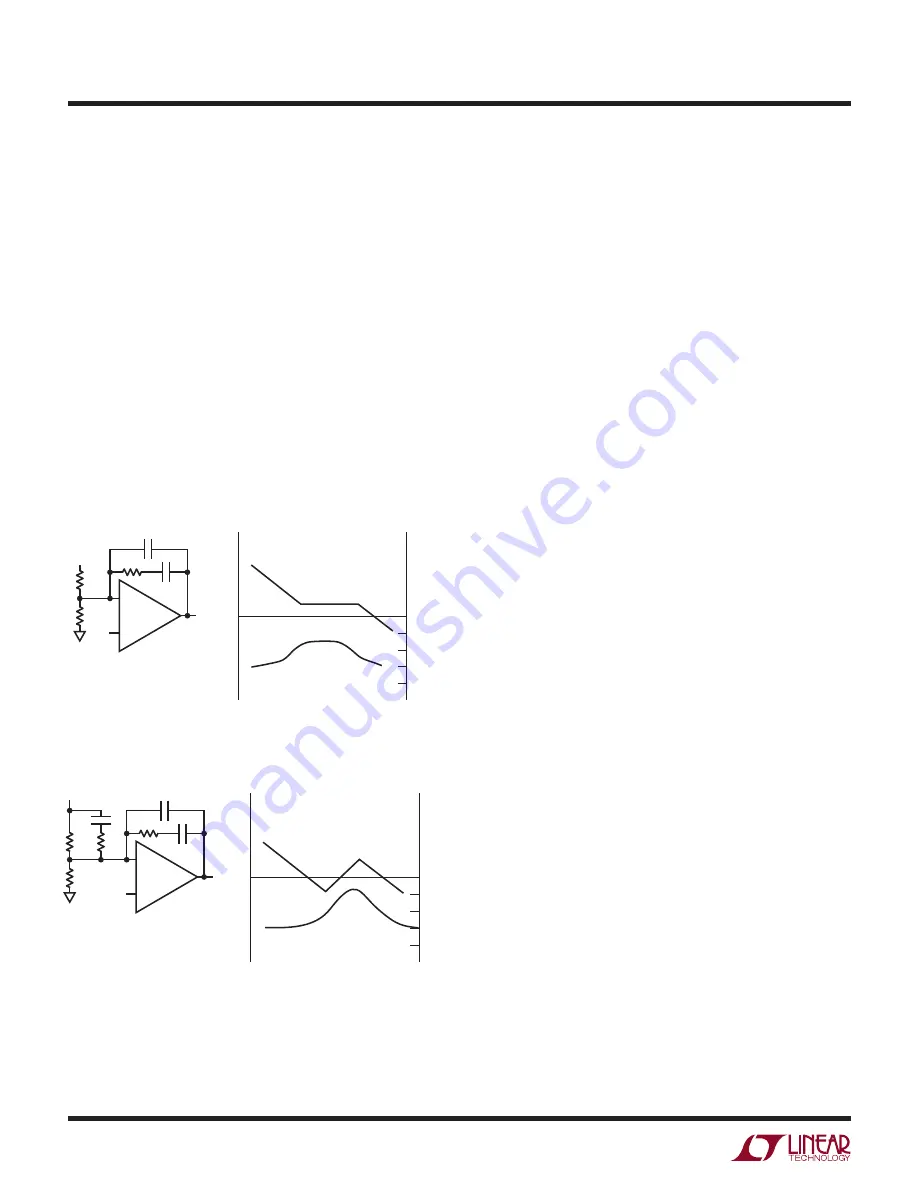
LTC3810-5
24
38105fd
Figure 11. Type 2 Schematic and Transfer Function
requirement of the compensation will be to guarantee that
the gain is below zero at frequencies above f
SW
/4. If the
ESR zero is above the crossover frequency, the feedback
amplifier will probably be required to provide phase boost.
For most LTC3810-5 applications, Type 2 compensation will
provide enough phase boost; however some applications
where high bandwidth is required with low ESR ceramics
and lots of bulk capacitance, Type 3 compensation may
be necessary to provide additional phase boost.
The two types of compensation networks, “Type 2” and
“Type 3” are shown in Figures 11 and 12. When compo-
nent values are chosen properly, these networks provide
a “phase bump” at the crossover frequency. Type 2 uses
a single pole-zero pair to provide up to about 60° of phase
boost while Type 3 uses two poles and two zeros to provide
up to 150° of phase boost.
Figure 12. Type 3 Schematic and Transfer Function
Feedback Component Selection
Selecting the R and C values for a typical Type 2 or Type 3
loop is a nontrivial task. The applications shown in this
data sheet show typical values, optimized for the power
components shown. They should give acceptable perfor-
mance with similar power components, but can be way off if
even one major power component is changed significantly.
Applications that require optimized transient response will
require recalculation of the compensation values specifically
for the circuit in question. The underlying mathematics are
complex, but the component values can be calculated in
a straightforward manner if we know the gain and phase
of the modulator at the crossover frequency.
Modulator gain and phase can be obtained in one of
three ways: measured directly from a breadboard, or if
the appropriate parasitic values are known, simulated or
generated from the modulator transfer function. Mea-
surement will give more accurate results, but simulation
or transfer function can often get close enough to give
a working system. To measure the modulator gain and
phase directly, wire up a breadboard with an LTC3810-5
and the actual MOSFETs, inductor and input and output
capacitors that the final design will use. This breadboard
should use appropriate construction techniques for high
speed analog circuitry: bypass capacitors located close
to the LTC3810-5, no long wires connecting components,
appropriately sized ground returns, etc. Wire the feedback
amplifier with a 0.1µF feedback capacitor from I
TH
to FB
and a 10k to 100k resistor from V
OUT
to FB. Choose the
bias resistor (R
FB2
) as required to set the desired output
voltage. Disconnect R
FB2
from ground and connect it to
a signal generator or to the source output of a network
analyzer to inject a test signal into the loop. Measure the
gain and phase from the I
TH
pin to the output node at the
positive terminal of the output capacitor. Make sure the
analyzer’s input is AC coupled so that the DC voltages
present at both the I
TH
and V
OUT
nodes don’t corrupt the
measurements or damage the analyzer.
If breadboard measurement is not practical, a SPICE
simulation can be used to generate approximate gain/
phase curves. Plug the expected capacitor, inductor and
MOSFET values into the following SPICE deck and gener-
ate an AC plot of V
OUT
/V
ITH
with gain in dB and phase in
applicaTions inForMaTion
GAIN (dB)
38105 F11
0
PHASE
–6dB/OCT
–6dB/OCT
GAIN
PHASE (DEG)
FREQ
–90
–180
–270
–360
R
FB2
V
REF
R
FB1
R2
FB
C2
IN
OUT
+
–
C1
GAIN (dB)
38105 F12
0
PHASE
–6dB/OCT
+6dB/OCT
–6dB/OCT
GAIN
PHASE (DEG)
FREQ
–90
–180
–270
–360
V
REF
R2
FB
C2
IN
OUT
+
–
C1
C3
R3
R
FB2
R
FB1