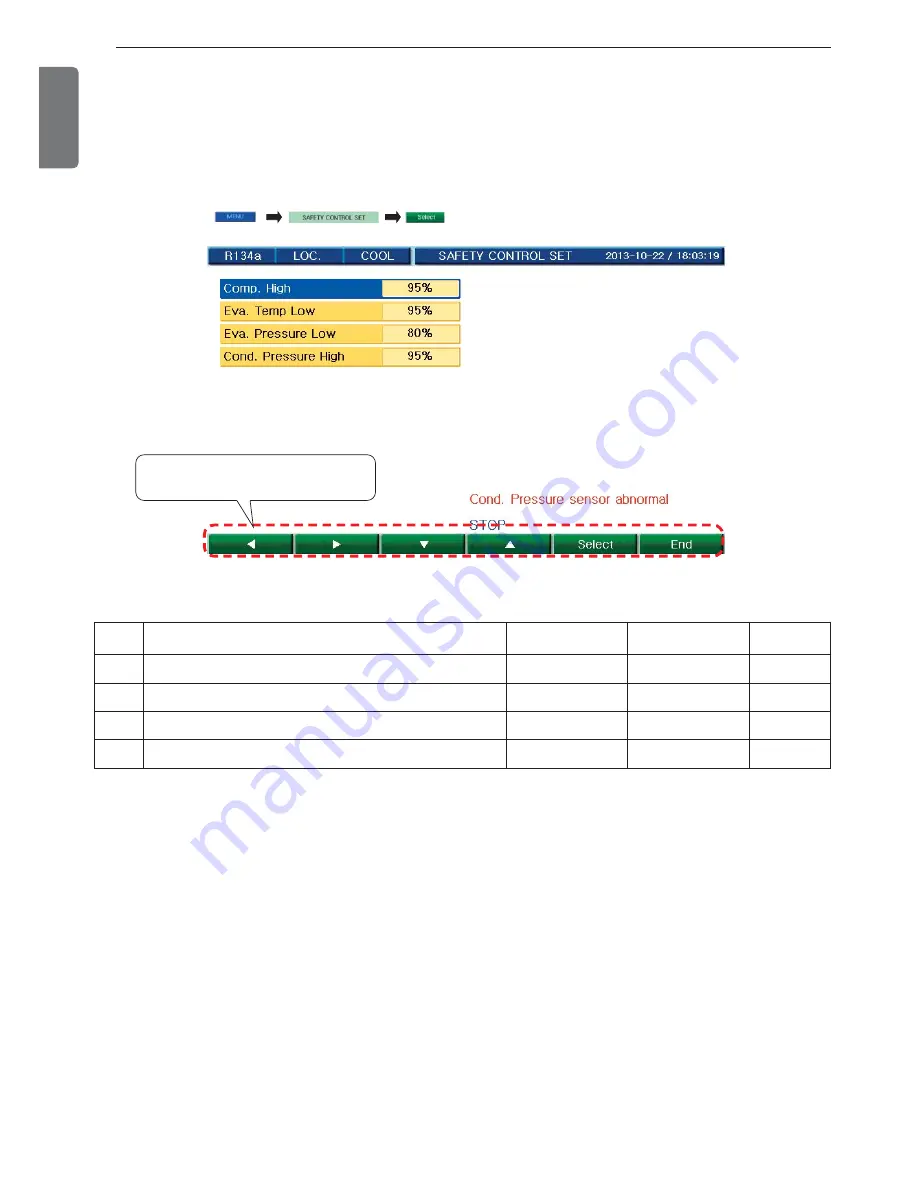
60
4. CONTROL SYSTEM
ENGLISH
Safety control setting
Here, you can set the values of safety control of the chiller.
If you move cursor to an item which you want to set in the menu bar, and press 'Select' key, then the key menu will
alternate through Previous, Next, Down and Up with the cursor blinking on the set value.
You can set a value by designating the cipher with Previous or Next key and changing it with Decrease or Increase
key, and pressing Set key.
- Movement path :
No
Setting items
Setting Range
Default value/unit
Remark
1
To prevent compressor discharge temperature high
50~100
95%
Note 1.
2
To prevent evaporator refrigerant temperature low
50~100
95%
Optional
3
To prevent evaporator pressure low
50~100
95%
4
To prevent condenser pressure high
50~100
95%
Note 1. R134a(High pressure) : Standard application, R123(Low pressure) : Option
The method of use is the same as
in "2) User setting".
Figure 40 Safety control setting screen
1. To prevent compressor discharge temperature high
If the compressor discharge reaches 95% of temperature of "Compressor discharge temperature high” during the
-operation, the capacity control valve controls to the direction of closing to implement the control to prevent the
chiller from abnormal stop. Although the setting value can be changed based on the operation condition of the in-
stallation site of the chiller, consult an expert for correct setting, since incorrect setting can affect the temperature
control of the chiller.
2. To prevent evaporator refrigerant temperature low
If the evaporator refrigerant temperature is lower than the setting value, capacity control valve is controlled to the
direction of closing. The standard value of the setting is the Evaporator refrigerant temperature. Please refer to the
abnormal setting menu.
3. To prevent evaporator pressure low
This is the item to set the preventive control for the Evaporator pressure lower limit. If the evaporator pressure is
lower than the setting value during the chiller running, capacity control valve is controlled to the direction of clos-
ing. The default value of the setting is the “Evaporator pressure low”. Please refer to the abnormal setting menu.
4. To prevent condenser pressure high
This is the item to set the preventive control for the Condenser pressure high. If the condenser pressure is above
the setting value during the chiller running, Capacity control valve is controlled to the direction of closing.
The default value of the setting is the “Condenser pressure high”. Please refer to the abnormal setting menu.
Содержание LCWW
Страница 119: ......