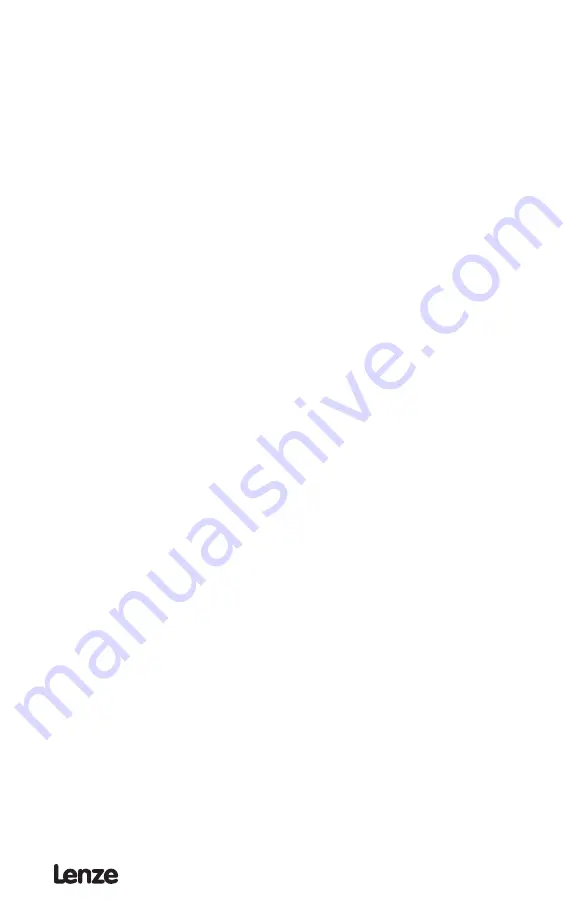
S94P01B
27
5.4.4 MODBUS RTU support
As a default, the RS232 and RS485 interfaces are configured to support MotionView
program operations. In addition, the RS485 interface can be configured to support
the MODBUS RTU slave protocol. The interface can be configured through the
MotionView program. When configured for MODBUS operation, the baud rate for
RS485 is set by the parameter “Modbus baud rate” in MotionView, while the RS232
baud rate is set on the drive’s front panel. Thus RS485 and RS232 can have different
speeds at the same time if RS485 is configured for MODBUS operation. Please note
that if RS485 is configured for MODBUS operation, the command repeat function (see
5.4.3) is unavailable even if baud rates are set the same for both interfaces.
The Modbus RTU slave interface protocol definitions can be found in the MotionView
help menu under “Product Manuals”.
5.5 Motor Selection
The PostionServo 940 drive is compatible with many 3-phase AC synchronous servo
motors. MotionView is equipped with a motor database which contains over 600
motors for use with the 940 drive. If the desired motor is in the database, no data to
set it up is needed. Just select the motor and click “OK”. However, if your motor is not
in the database, it can still be used, but some electrical and mechanical data will need
to be provided to create a custom motor profile. The auto-phasing feature of the 940
allows the user to correctly determine the relationship between phase voltage and hall
sensor signals, eliminating the need to use a multi-channel oscilloscope.
5.5.1 Motor connection.
Motor phase U, V, W (or R, S, T) are connected to terminal P7. It is very important that
motor cable shield is connected to Earth ground terminal (PE) or the drive’s case.
The motor feedback cable must be connected to encoder terminal P4 if the motor
is equipped with an incremental encoder. If the motor is equipped with a resolver it
needs to be connected to terminal P11 on the resolver option module.
5.5.2 Motor over-temperature protection
If using a motor equipped with an encoder and PTC thermal sensor, the encoder
feedback cable will have flying leads exiting the P4 connector to be wired to the P7.1
(T1) and P7.2 (T2) terminals. If using a motor equipped with a Resolver and a PTC
sensor, the connector on the Resolver Option Module (P11) provides this connection.
Use parameter “Motor PTC cut-off resistance” (see section 6.3.12) to set the
resistance which corresponds to maximum motor allowed temperature. The parameter
“Motor temperature sensor” must also be set to ENABLE. If the motor doesn’t have
a PTC sensor, set this parameter to DISABLE. This input will also work with N.C.
thermal switches which have only two states; Open or Closed. In this case “Motor PTC
cut-off resistance” parameter can be set to the default value.
Содержание PositionServo 940
Страница 1: ...Model 940 USERS MANUAL S94P01B S929...
Страница 12: ...S94P01B 10 3 2 Clearance for Cooling Air Circulation S924...
Страница 66: ...S94P01B 64 Notes...
Страница 67: ......