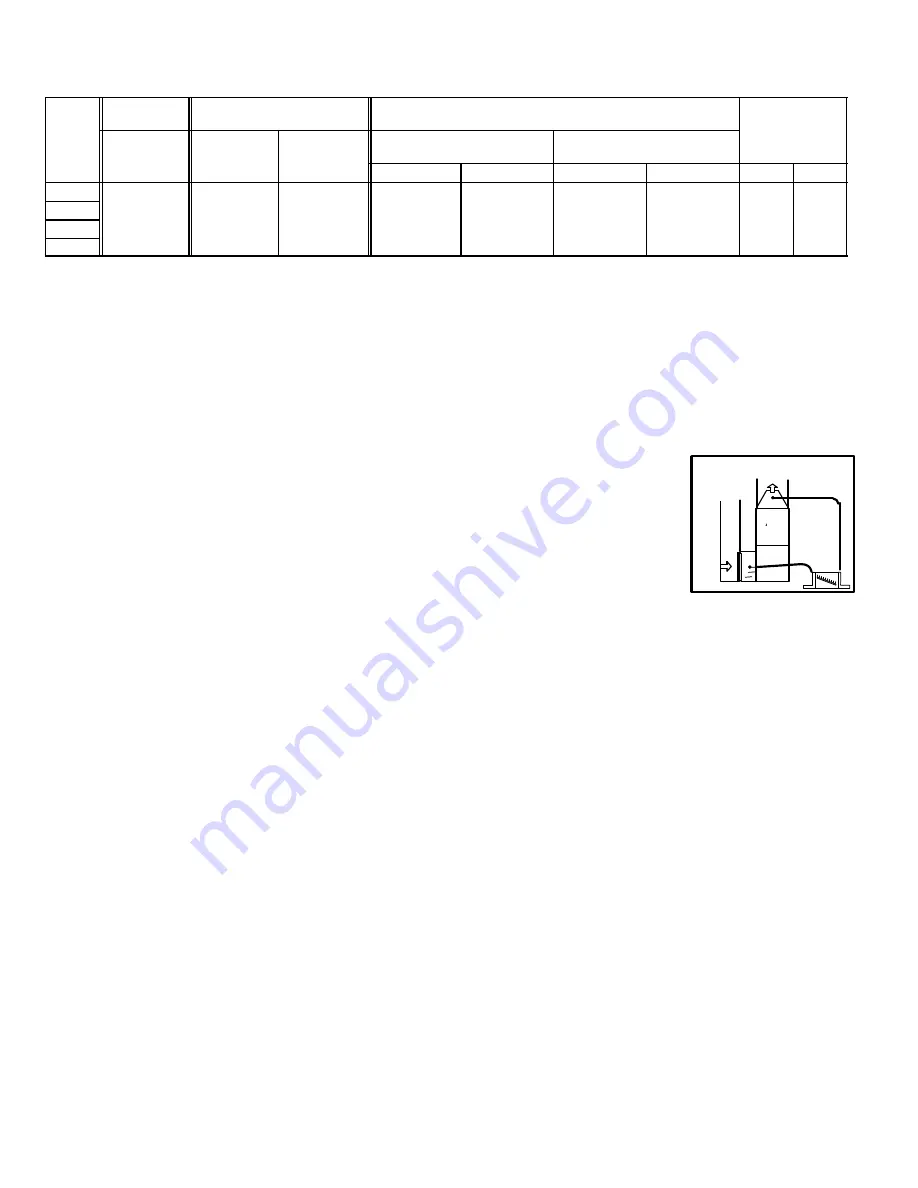
Page 56
TABLE 29
Conversion Kit Requirements and Manifold Test Pressures
Model
Input
Size
LP/Propane
Kit
High Altitude Pressure
Switch Kit
Manifold Pressure at All Altitudes (in. w.g.)
Gas Orifice Size
0 − 10,000
(0 − 3048 m)
0 − 7,500
(0 − 2286 m)
7,501 − 10,000
(2287 −
3048m)
Low Fire
(35% rate)
High Fire
(100% rate)
Natural Gas
LP/Propane
Natural Gas
LP/Propane
Nat
LP
−070
65W77
Not required
70W90
0.4 − 0.6
1.2 − 1.8
3.2 − 3.8
9.5 − 10.5
0.0625
0.034
−090
−110
−135
NOTE
− The values given in table are measurements only. The gas valve should not be adjusted.
VI−TYPICAL OPERATING CHARACTERISTICS
A−Blower Operation and Adjustment
1 − Blower operation is dependent on thermostat control
system.
2 − Generally, blower operation is set at thermostat subbase
fan switch. With fan switch in ON position, blower oper-
ates continuously. With fan switch in AUTO position,
blower cycles with demand or runs continuously while
heating or cooling circuit cycles.
3 − Depending on the type of indoor thermostat, blower and
entire unit will be off when the system switch is in OFF
position.
B−Temperature Rise
Temperature rise for SLP98UHV units depends on unit in-
put, blower speed, blower horsepower and static pressure
as marked on the unit rating plate. The blower speed must
be set for unit operation within the range of TEMP. RISE
°
F" listed on the unit rating plate.
To Measure Temperature Rise:
1 − Place plenum thermometers in the supply and return air
plenums. Locate supply air thermometer in the first hori-
zontal run of the plenum where it will not pick up radiant
heat from the heat exchanger.
2 − Set thermostat for heat call. Unit must operate on sec-
ond−stage heat.
If using a single−stage thermostat fur-
nace must fire at least 10 minutes before switching to
second−stage heat.
3 − After plenum thermometers have reached their highest
and steadiest readings, subtract the two readings. The
difference should be in the range listed on the unit rating
plate. If the temperature is too low, decrease blower
speed. If temperature is too high, first check the firing
rate. Provided the firing rate is acceptable, increase
blower speed to reduce temperature.
C−External Static Pressure
1 − Tap locations shown in figure 46.
2 − Punch a 1/4" diameter hole in
supply and return air ple-
nums. Insert manometer
hose flush with inside edge of
hole or insulation. Seal
around the hose with perma-
gum. Connect the zero end of
the manometer to the dis-
charge (supply) side of the system. On ducted systems,
connect the other end of manometer to the return duct
as above.
3 − With only the blower motor running and the evaporator
coil dry, observe the manometer reading. Adjust blower
motor speed to deliver the air desired according to the
job requirements.
4 − External static pressure drop must not be more than
0.8" W.C. in the heating mode and must not exceed 1.0"
W.C in the cooling mode.
5 − Seal the hole when the check is complete.
FIGURE 46
STATIC PRESSURE TEST
+
−