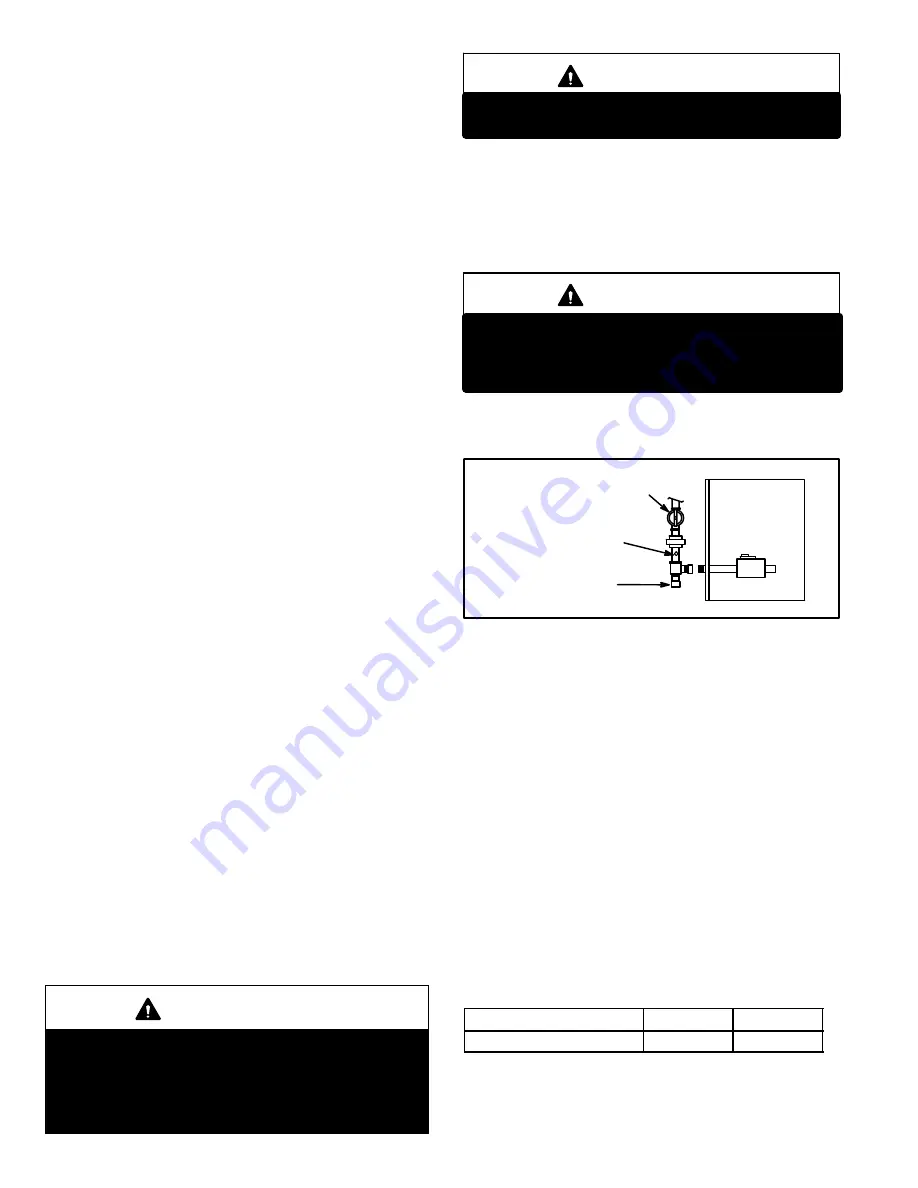
Page 54
8 − Move gas valve switch to the
ON
position. See figure 44.
Do not force.
9 − Replace the upper access panel.
10− Turn on all electrical power to to the unit.
11− Set the thermostat to desired setting.
NOTE
− When unit is initially started, steps 1 through 11 may
need to be repeated to purge air from gas line.
12− If the appliance will not operate, follow the instructions
Turning Off Gas to Unit" and call your service techni-
cian or gas supplier.
Turning Off Gas to Unit
1 − Set the thermostat to the lowest setting.
2 − Turn off all electrical power to the unit if service is to be
performed.
3 − Remove the upper access panel.
4 − Move the gas valve switch to the
OFF
position.
5 − Replace the upper access panel.
Failure To Operate
If the unit fails to operate, check the following:
1 − Is the thermostat calling for heat?
2 − Are access panels securely in place?
3 − Is the main disconnect switch closed?
4 − Is there a blown fuse?
5 − Is the filter dirty or plugged? Dirty or plugged filters will
cause the limit control to shut the unit off.
6 − Is gas turned on at the meter?
7 − Is the manual main shut-off valve open?
8 − Is the gas valve turned on?
9 − Is the unit ignition system in lock out? If the unit locks out
again, inspect the unit for blockages.
10 − Is blower harness connected to integrated control? Fur-
nace will not operate unless harness is connected.
C−Safety or Emergency Shutdown
Turn off unit power. Close manual and main gas valves.
D−Extended Period Shutdown
Turn off thermostat or set to UNOCCUPIED" mode. Close
all gas valves (both internal and external to unit) to guaran-
tee no gas leak into combustion chamber. Turn off power to
unit. All access panels and covers must be in place and se-
cured.
V−HEATING SYSTEM SERVICE CHECKS
A−CSA Certification
All units are CSA design certified without modifications. Re-
fer to the SLP98UHV Installation Instruction.
B−Gas Piping
CAUTION
If a flexible gas connector is required or allowed by
the authority that has jurisdiction, black iron pipe
shall be installed at the gas valve and extend outside
the furnace cabinet. The flexible connector can then
be added between the black iron pipe and the gas
supply line.
WARNING
Do not exceed 600 in−lbs (50 ft−lbs) torque when at-
taching the gas piping to the gas valve.
Gas supply piping should not allow more than 0.5"W.C. drop
in pressure between gas meter and unit. Supply gas pipe
must not be smaller than unit gas connection.
Compounds used on gas piping threaded joints should be
resistant to action of liquefied petroleum gases.
C−Testing Gas Piping
IMPORTANT
In case emergency shutdown is required, turn off
the main shut-off valve and disconnect the main
power to unit. These controls should be properly
labeled by the installer.
When pressure testing gas lines, the gas valve must be dis-
connected and isolated. Gas valves can be damaged if sub-
jected to more than 0.5psig (14" W.C.). See figure 45
.
FIGURE 45
MANUAL MAIN SHUT−OFF
VALVE WILL NOT HOLD
NORMAL TEST PRESSURE
CAP
FURNACE
ISOLATE
GAS VALVE
1/8" N.P.T. PLUGGED TAP
When checking piping connections for gas leaks, use pre-
ferred means. Kitchen detergents can cause harmful corro-
sion on various metals used in gas piping. Use of a specialty
Gas Leak Detector is strongly recommended. It is available
through Lennox under part number 31B2001. See Corp.
8411−L10, for further details.
Do not use matches, candles, flame or any other source of
ignition to check for gas leaks.
D−Testing Gas Supply Pressure
When testing supply gas pressure, connect test gauge to
supply pressure tap on the gas valve. See figure 44. Check
gas line pressure with unit firing at maximum rate. Low pres-
sure may result in erratic operation or underfire. High pres-
sure can result in permanent damage to gas valve or over-
fire. See table 25 for operating pressure at unit gas connec-
tion (line).
On multiple unit installations, each unit should be checked
separately, with and without units operating. Supply pres-
sure must fall within range listed in table 25.
TABLE 25
All SLP98UHV Units
Natural
LP
Line Pressure WC"
4.5 − 10.5
11.0 − 13.0
E−Check Manifold Pressure
To correctly measure manifold pressure, the differential
pressure between the positive gas manifold and the nega-
tive burner box must be considered. Use pressure test