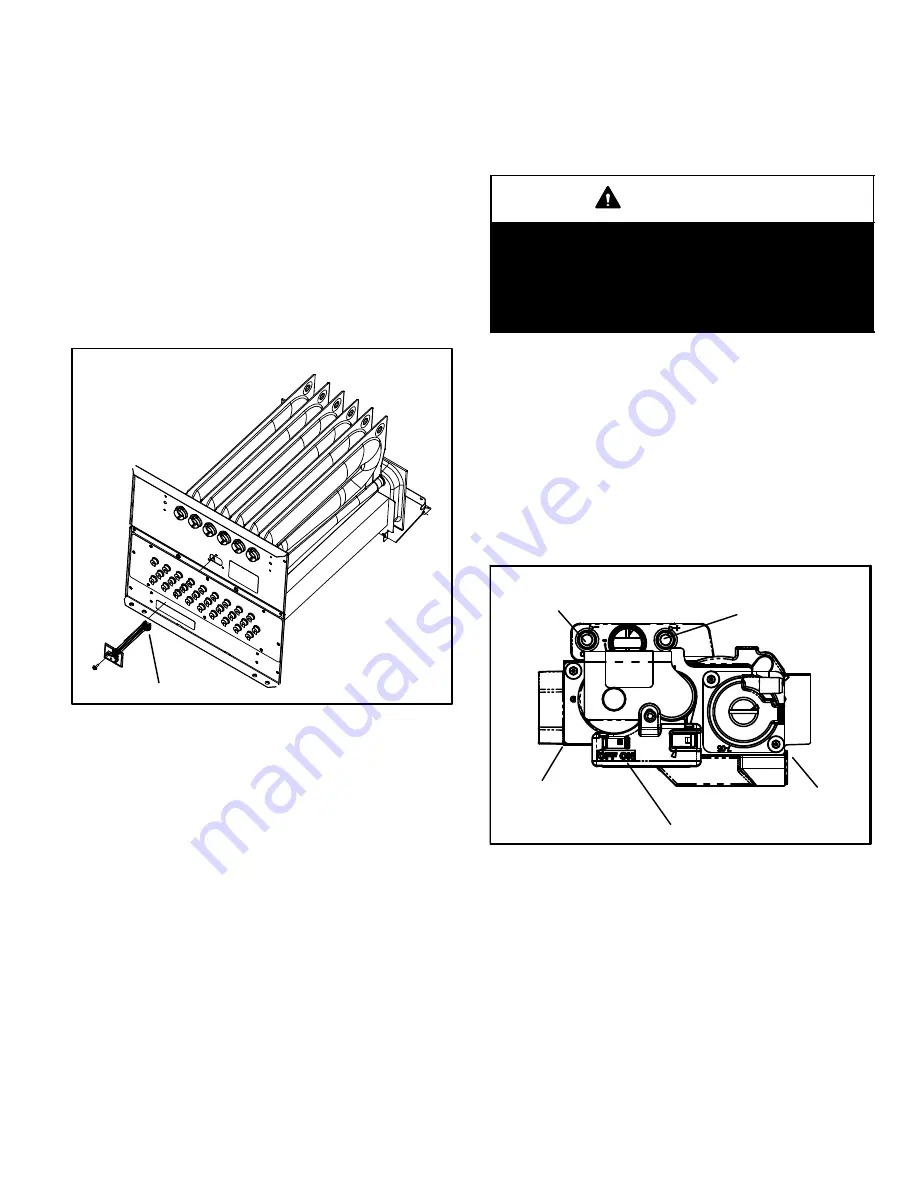
Page 33
6. Primary Limit Control (S10)
Figure 12 shows the primary limit (S10) used on SLP98UHV
units located in the heating vestibule panel. When excess heat
is sensed in the heat exchanger, the limit will open. Once the
limit opens, the furnace control energizes the supply air
blower and de−energizes the gas valve. The limit automati-
cally resets when unit temperature returns to normal. The
switch is factory set and cannot be adjusted. In the event of
restricted air flow, the integrated control will reduce firing
rate and indoor blower airflow in 10% increments until a sus-
tainable air flow is reached. If the furnace reaches 35% fir-
ing rate, and adequate air flow is not available, the furnace
will shutdown and enter one hour watchguard. For limit re-
placement remove wires from limit terminals and rotate limit
switch 90 degrees. Slowly remove from the vestibule panel.
FIGURE 12
Primary Limit Location and Heat Exchanger
install limit face down
7. Gas Valve (GV1)
The SLP98UHV uses a variable capacity gas valve (figure
44) and is applicable for two−stage or variable capacity set-
tings. See Thermostat selection modes" in the integrated
control section (section A− subsection 4.) for more details
The valve is internally redundant to assure safety shut−off. If
the gas valve must be replaced, the same type valve must
be used.
A 24VAC 2−pin plug and gas control switch are located on the
valve. 24V applied to the pins enables valve operation.
Inlet and outlet pressure taps are located on the valve.
LPG change over kits are available from Lennox. Kits include
burner orifices and an LP gas valve.
DANGER
Danger of explosion.
There are circumstances in which odorant used with
LP/propane gas can lose its scent. In case of a leak,
LP/propane gas will settle close to the floor and may
be difficult to smell. An LP/propane leak detector
should be installed in all LP applications.
The burner box is sealed and operates under a negative
pressure. A pressure hose is connected from the burner box
to the gas valve. The gas valve senses the pressure in the
burner box and uses that to set the maximum manifold pres-
sure while the pressure switch with pressure conditioning
device adjusts the gas flow. This will compensate for differ-
ent vent configurations which can greatly affect the rate of
the unit.
NEGATIVE AIR
PRESSURE PORT
POSITIVE AIR
PRESSURE PORT
MANIFOLD
PRESSURE TAP
INLET
OUTLET
SUPPLY
PRESSURE
TAP
GAS VALVE SHOWN IN THE ON POSITION
FIGURE 13