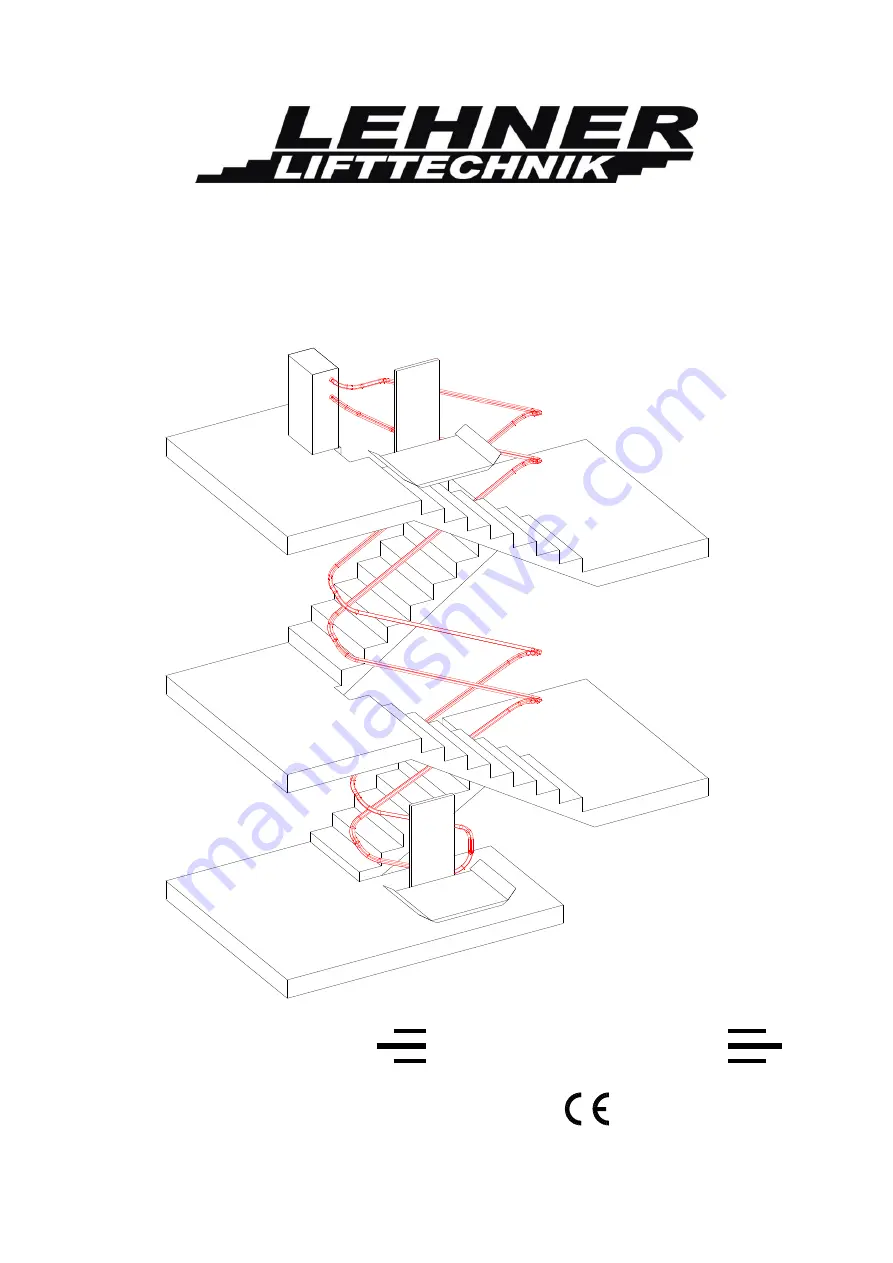
Austria, 4724 Neukirchen/W, Salling 8
Tel: +4372783514
Email: [email protected]
Mobil: +436641612980
Installation Manual
MEGA – F
s t a i r l i f t
Austria, 4724 Neukirchen/W, Salling 8
Tel: +4372783514
Email: [email protected]
Mobil: +436641612980
Installation Manual
MEGA – F
s t a i r l i f t