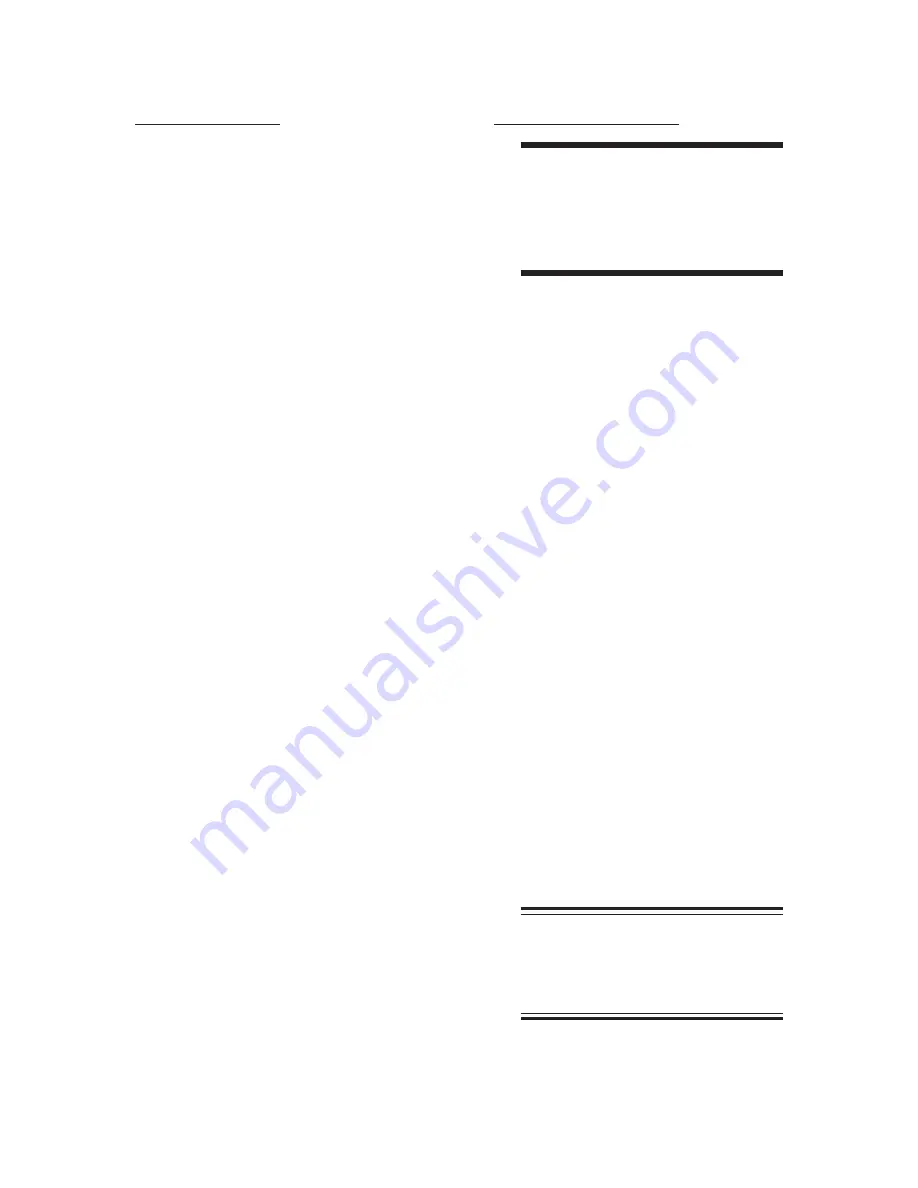
GL16
Operating Guidelines
3-9
Flatwork Handling
It is very important how operators use the unit.
By following these guidelines, operators can
increase productivity, extend the life of the unit,
and most importantly - promote safety.
Safety
•
Remove the flatwork only after it has
cleared the unit. Do not pull on the
finished flatwork while it is still in
the unit.
•
Parts of the unit can be hotter than 300°F
(150°C). Severe burns can result.
Maximum Efficiency
•
Follow the posted standards for the type
of flatwork being processed.
•
Place the flatwork straight and square on
the feed ribbons.
•
Stretch the flatwork slightly to the sides
when feeding the flatwork into the unit.
•
Feed pillowcases lengthwise with the
closed end first.
•
Leave a small gap between each item
being processed when you feed flatwork.
•
Two operators should feed and receive
flatwork. While one operator is manually
folding flatwork, the other operator can
prepare the next piece of flatwork for
processing.
Ironing Cylinder
•
Use the entire width of the heated ironing
section. This is especially important when
finishing pillowcases.
•
Work from side to side to prevent dirt and
heat buildup at the ends of the ironing
cylinder. This also preserves padding life.
•
Rewax the ironing section before ironing
thicker flatwork such as tablecloths. This
will result in a better finish quality.
Clearing a Jam Safely
WARNING
The ironing cylinder will
burn you on contact. Never
reach in, on, or near the
ironing cylinder.
If a piece of flatwork becomes jammed, use
the following procedure to clear the jam safely:
1.
Stop feeding flatwork.
2.
Wait for any flatwork already in the unit
to exit.
3.
Turn the SPEED knob to the slowest
speed.
4.
Stop the unit by pressing a red STOP but-
ton.
5.
Turn the GAS switch to OFF.
6.
Make sure the jammed flatwork can be
removed easily before removing it.
7.
If the jammed flatwork cannot be re-
moved easily, announce the unit is being
started. Make sure everyone is a safe dis-
tance away from the unit.
8.
Turn the JOG switch forward or back-
ward and jog the unit briefly, then pause
2-3 seconds before jogging the unit again.
Continue jogging the unit forward or back-
ward in brief increments until the jammed
flatwork can be safely and easily removed.
Do not start the unit until the jam is
cleared.
NOTE:
If jamming occurs
regularly, tell the maintenance or
service people so they can fix the
problem.
Содержание Flatwork Ironer Series
Страница 1: ...GL16 Gas Heated Flatwork Ironer INSTRUCTION MANUAL...
Страница 8: ...Skyline S1 S20 Installation...
Страница 12: ......
Страница 18: ...Skyline S1 S20 Installation...
Страница 58: ...Skyline S1 S20 Installation...
Страница 76: ...Skyline S1 S20 Installation...
Страница 94: ...Skyline S1 S20 Installation...
Страница 166: ...Skyline S1 S20 Installation...
Страница 168: ......
Страница 176: ...8 PL 3031 009c GL16 Drive Side View Type R Only...
Страница 180: ...12 PL 3031 009c GL16 Rolls and Ribbons Type R Machine Only NOTE Ribbon Quantities May Vary Per Model Lengths...
Страница 183: ...15 GL16 PL 3031 009c This Page Blank on Purpose...
Страница 186: ...18 PL 3031 009c GL16 Disconnect Panel...
Страница 188: ......
Страница 189: ...GL16 Schematics and Parts 3210 361...
Страница 190: ...2...
Страница 192: ...4...
Страница 194: ...6...
Страница 196: ...8...
Страница 198: ...10...
Страница 200: ...12...
Страница 202: ...14...
Страница 203: ...GL16 15...
Страница 204: ...Skyline S1 S20 Installation...
Страница 205: ......
Страница 206: ......
Страница 207: ......
Страница 208: ......
Страница 209: ......
Страница 210: ......
Страница 214: ......
Страница 216: ......
Страница 217: ...3045 001a...
Страница 218: ......
Страница 219: ......
Страница 220: ......
Страница 221: ......
Страница 222: ......
Страница 223: ......
Страница 224: ......
Страница 225: ......
Страница 226: ......
Страница 227: ......
Страница 228: ......
Страница 229: ......
Страница 230: ......
Страница 231: ......
Страница 232: ......
Страница 233: ......
Страница 234: ......
Страница 235: ......
Страница 236: ......
Страница 238: ......