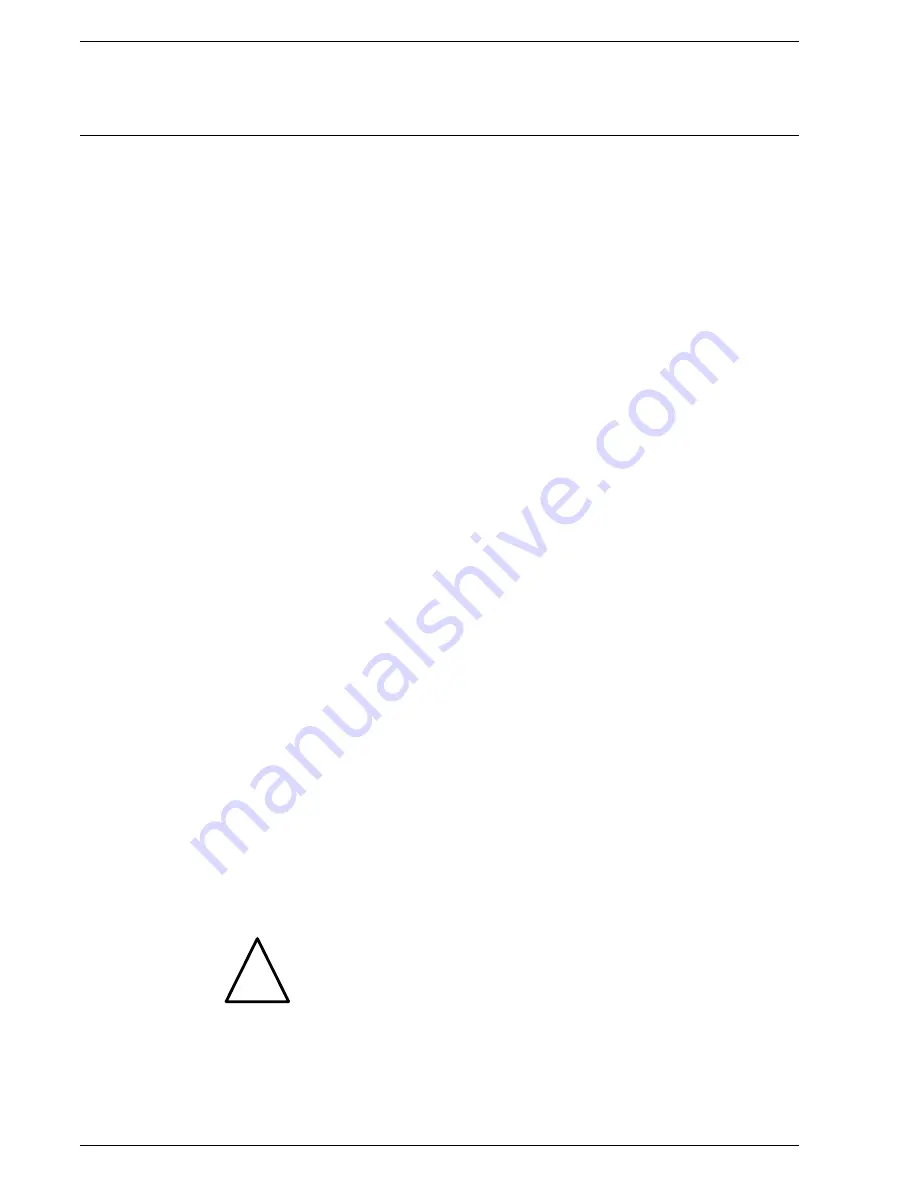
FMS Fault Correction
Parameters ( P )
Aids
P1
This parameter determines whether or not the compound control unit works
Parameter 4
with separate ignition point and whether the load default is set automatically
(level 2)
during setting. (See Tips & Tricks)
_____________________________________________________________________________________________________
P2
This determines whether the band shift in the event of a change in power
Parameter 707
output (in order to obtain excess air whilst running to a new load point) acts
on the load axis or the set-point axis. If it acts on the set-point axis the points
set are simply added to the existing set-points. If it acts on the load axis the
points are rated at the steepness of the curve and only then added. In the
case of continuous outputs and control elements with a linear characteristic
the effect should be applied to the set-point axis. In the case of control
elements with non-linear or exponential characteristic the parameter should
be set to "1”.
_____________________________________________________________________________________________________
P3
The band shift of the respective channel in the event of a change in power is
Parameters 708 to 712
entered in points here. The electronic compound control unit automatically
assesses the directions in which the band shift is to act on the basis of the
configuration of each control element (air up, fuel down). The band shift also
acts only when the load varies in the direction that represents an air advance
for the channel (in a load reduction the fuel is advanced, in a load increase the
air). The size of the values that must be entered here depends on the effect of
the control element on the lambda.
_____________________________________________________________________________________________________
P4
A number of points is entered here determining how wide the duct is to open
Parameters 346 to 350
in pre-ventilation. If 999 is entered (standard value) the duct runs as far as the
stop. This parameter serves for setting pre-ventilation limits, e.g. on air
dampers in order to curtail the pre-ventilation time (whilst nevertheless
guaranteeing the exchange of air during pre-ventilation) or on the
re-circulation damper in order to prevent overloading of the re-circulation
frequency converter during pre-ventilation.
_____________________________________________________________________________________________________
P5
The range limits (upper and lower) for the respective control element are
Parameters 186 to 300
entered here. Generally these are determined automatically, i.e. the
FMS / VMS fills in this parameter itself. The range limits determined form the
limits of the unit's control range. Should motors be changed or limit switch
settings be adjusted, the range limits must be re-determined.
_____________________________________________________________________________________________________
P6
These indicate how the control element is to behave in the event of a fault
Parameters 374 to 378
shut-off. The direction of running may be entered or the direction of running
combined with an external condition.
NOTE:
Since the FMS is already in the "Fault” condition, the function of the
control element can no longer be reliably monitored after this fault
shut-off. If it is absolutely essential that the position entered by reliably
attained, this must be guaranteed by way of a separate interrogation
measure, e.g. limit switch
(may be possible with defined valve positions for turbine exhaust
gas systems etc.)
With some internal faults, the FMS also switches off the
+
24 V supply to
terminal 10. In this case, too, the servomotors will no longer run.
109
!