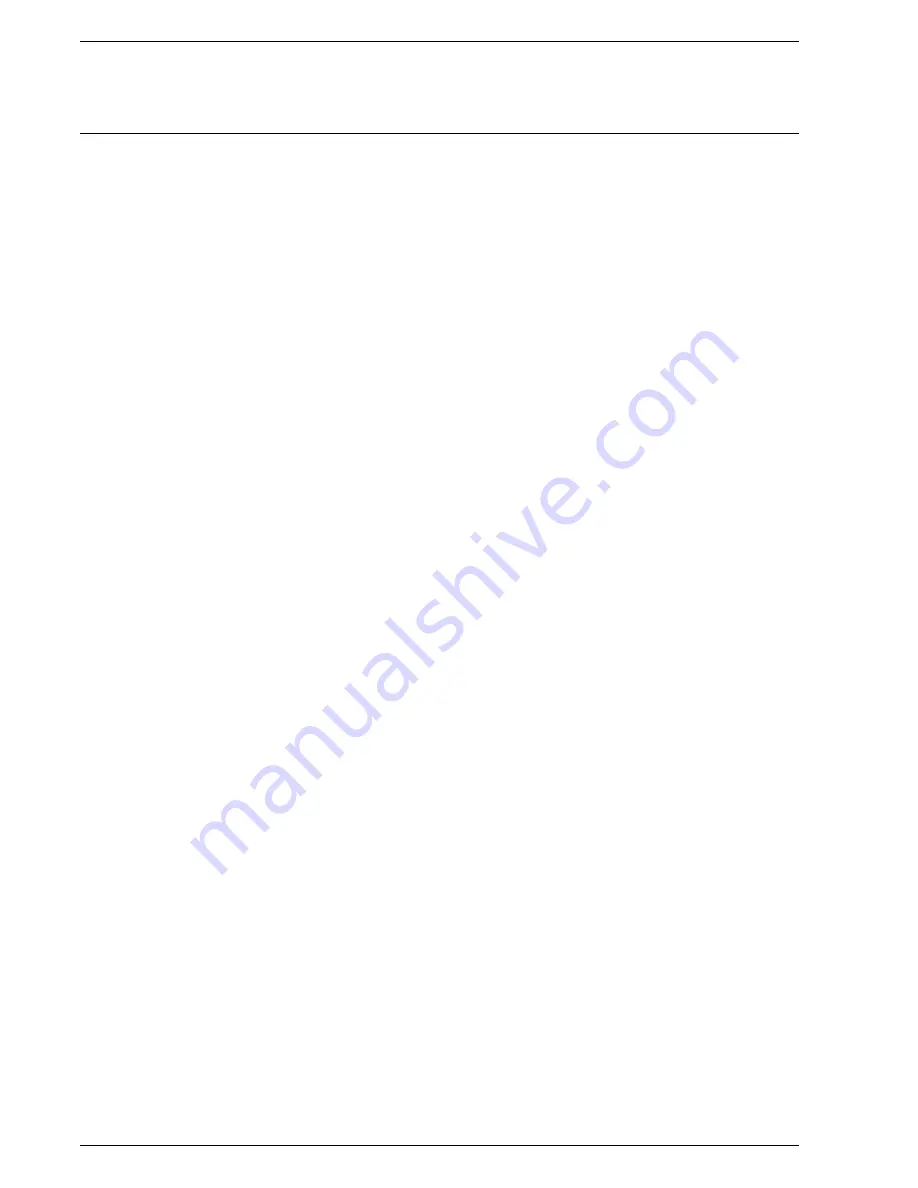
100
VMS Fault Correction
Feedback (E)
Aids
E1
A minimum value is not displayed in
On feedback via potentiometer:
"Actual value” position and "AU” display
Cause: potentiometer connections transposed
Check terminals
Cause: Potentiometer incorrectly fitted to the motor shaft
Turn potentiometer with control element connected until the desired
value is displayed.
Cause: control element is not in "CLOSED” position
Check whether the "CLOSE” relay on the relay module has pulled on
(recognisable from the LED on the relay module)
Check "F2” fuse (on the power supply front panel) of the VMS
Check lead to the control elements
(Is the "CLOSE” signal reaching the control element)
Cause: the FMS has read in an incorrect range limit.
Re-enter range limits
_____________________________________________________________________________________________________
E2
Feedback does not move, although
Check feedback connection to the FMS (See connection diagram)
the control element moves
___________________________________________________________________
In order to locate faults, it is recommended that the feedback be simulated at
various points on the feedback circuit (using potentiometer or a current
transmitter).
___________________________________________________________________
_____________________________________________________________________________________________________
E3
The feedback of the continuous output For feedback via potentiometer, see E4
does not display the values indicated
For feedback via current, see E5
_____________________________________________________________________________________________________
E4
The feedback displays much too high
Potentiometer leads are transposed
a value or goes only
to approx. 500 points
Check connections
___________________________________________________________________
In order to ensure that the FMS is working correctly a 5k
S
potentiometer
may connected directly to the VMS feedback input in order to simulate the
feedback manually.
___________________________________________________________________
_____________________________________________________________________________________________________
E5
Feedback shows "000” and does not
The poles of the feedback current signal are probably reversed.
vary, even if the current is increased.
Check connections
___________________________________________________________________
The feedback can be simulated by means of a current transmitter.
This makes it easier to locate the fault on the feedback circuit.
___________________________________________________________________
_____________________________________________________________________________________________________
E6
Fault 361
Main and monitoring processor do not
Check limit switch position
show the same feedback value,
although the same signal is fed
Check connections for transposition and reversal, see also E5, E4, E1
to each of them