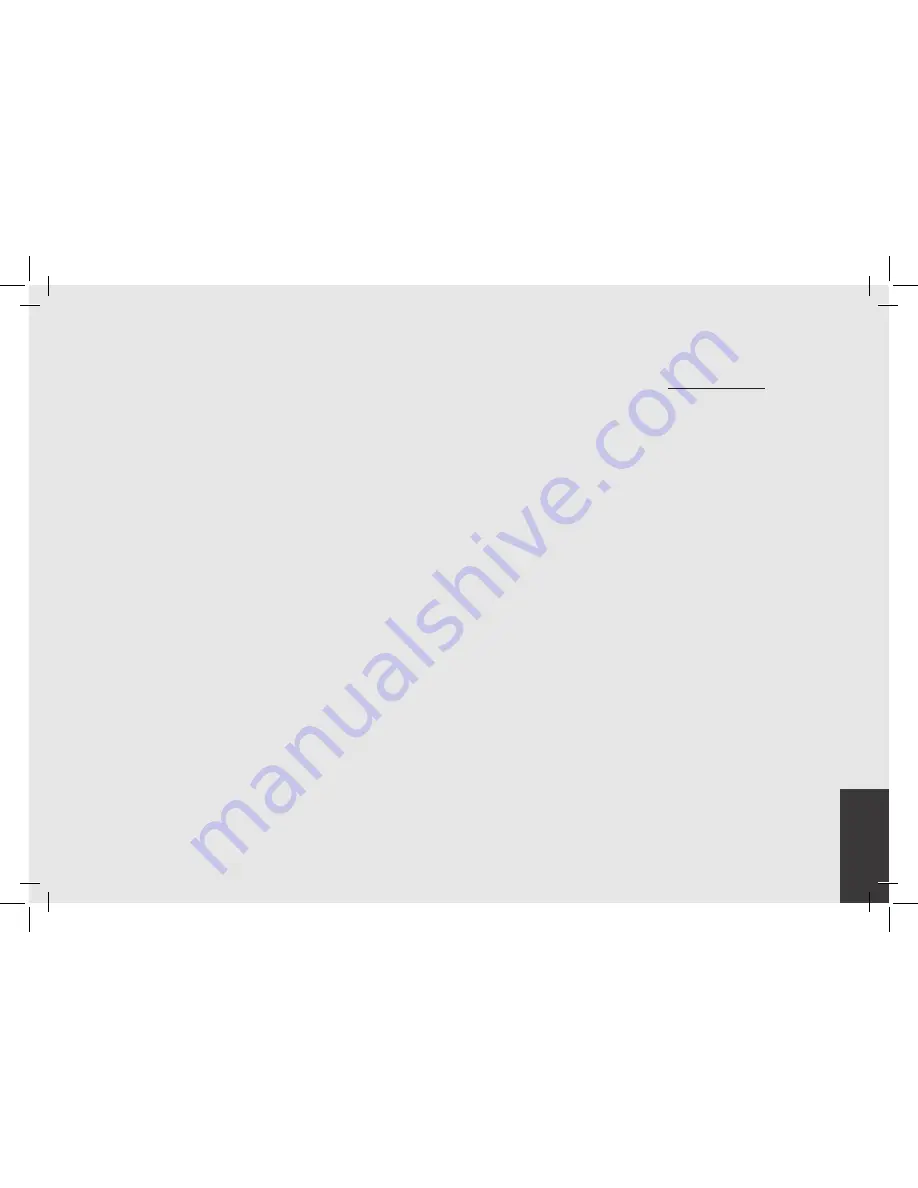
EN
17
3. Cleaning the body.
Wipe the stainless steel surfaces with a
soft, non abrasive cloth in the direction of
the glazing marks, if any. Do not use any
alcohol or solvents whatsoever on painted,
imprinted, or plastic parts in order not to
damage them. Clean the side panels using
a soft cloth. Clean only with a damp soft
cloth or possibly soaked in warm water and
mild soap.
4. Cleaning the steam nozzles.
Steam nozzles must be cleaned
immediately after use with a damp cloth
and by producing a short burst of steam
so as to prevent the formation of deposits
inside the nozzles themselves, which
may alter the flavor of other drinks to be
heated. If milk residue is present on the
steam wand, soak the tip in a container of
hot water, then it will be possible to wipe
the tip clean. Repeat process if residue
remains.
5. Cleaning the hot water nozzles.
Hot water nozzles must be cleaned
periodically with a damp cloth soaked in
water and/or mild soap.
NOTE:
This cleaning schedule is based
upon a moderate to average use (5-20)
cups per day. If machine use is less than
moderate then this schedule may be
adjusted accordingly.
6. Clean the water reservoir and the drain
box:
The water reservoir needs to be
cleaned periodically to ensure that no
algae forms on the inside surfaces. To
clean, first remove the water reservoir from
the machine. Disconnect the clear plastic
water intake hose. Hand wash each part
with water containing mild soap.
Cleaning frequency
Daily
•
Portafilter
•
Filter
•
Diffuser screen
•
Diffuser screw
•
Steam wand (just after use)
•
Drain grille
Weekly
•
Water Reservoir
•
Drain Box
Monthly
•
Cleaning the hot water nozzle
N.B.:
For details about cleaning, refer to the
quick start guide on the website
http://global.lamarzocco.com/en/linea-mini-en
Содержание linea mini
Страница 28: ......