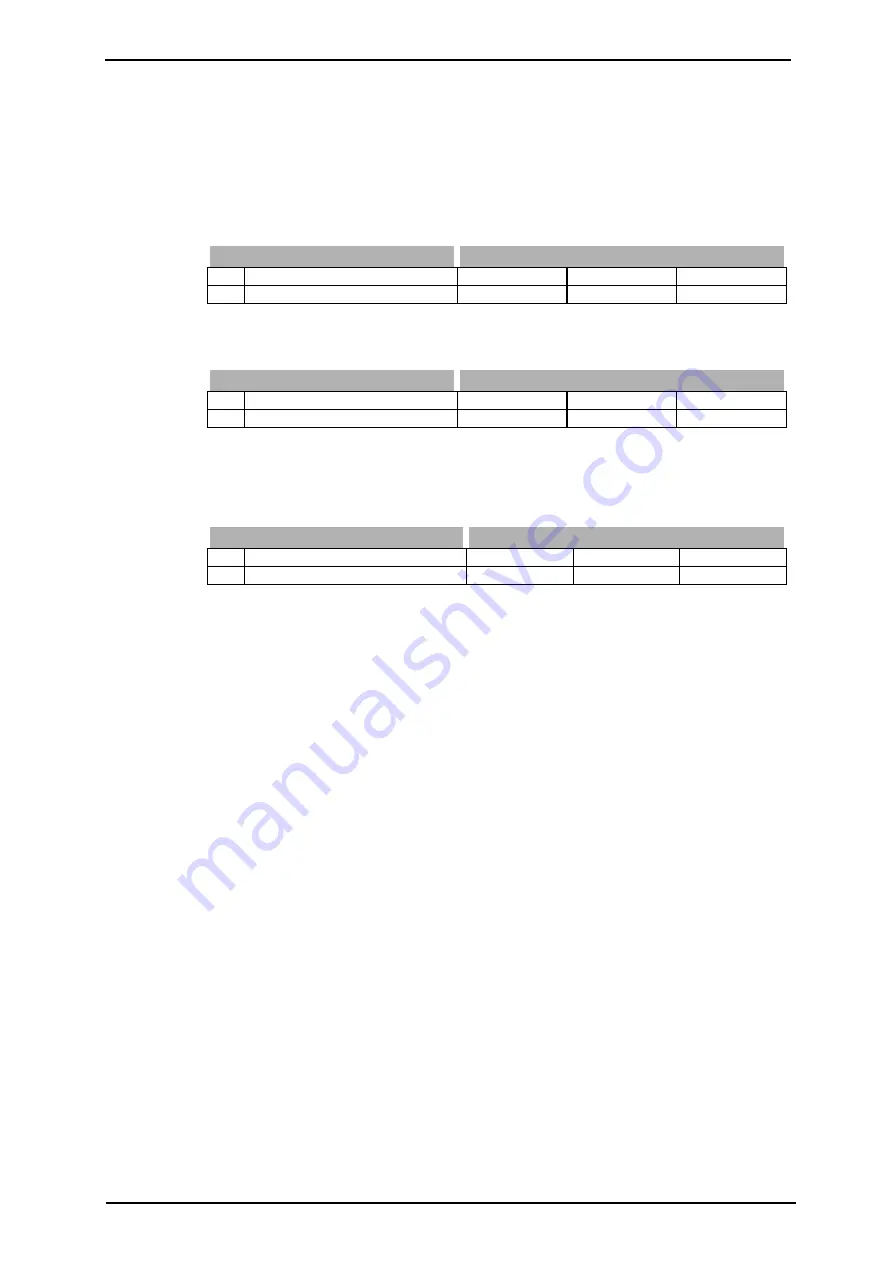
KFU 2-/4-
126
The positioning is started by a start command from a signal source (e.g. digital input)
which must be assigned to the parameter
Start Positioning of Axle
37
. The signal
source can be selected from the operation modes for digital inputs described in chap-
ter "Digital inputs".
The positioning starts on condition that the
Actual frequency
241
of the output signal
is smaller than the value entered in parameter
Positioning frequency
471
. Due to a
stopping behavior, the actual frequency drops below the positioning frequency.
Parameter
Settings
No.
Description
Min.
Max.
Fact. sett.
471 Positioning frequency
1.00 Hz
50.00 Hz
50.00 Hz
Via the parameter
Max. positional error
472
, the maximum permissible deviation
from the
Reference orientation
469
can be set.
Parameter
Settings
No.
Description
Min.
Max.
Fact. sett.
472 Max. positional error
0.1°
90.0°
3.0°
Via parameter
Time constant positioning controller
479
, the time constant for control-
ling the positional error can be set. The value of the time constant should be in-
creased if oscillations of the drive around the reference orientation occur during the
positioning.
Parameter
Settings
No.
Description
Min.
Max.
Fact. sett.
479 time constant positioning contr.
1.00 ms
9999.99 ms
20.00 ms
To make sure that the set position is maintained if a load torque is applied, a stopping
behavior should be selected for parameter
Operation mode
630
which impresses a
starting current either permanently when the drive is at a standstill or for the stopping
time.
The status message “60 - Target Position Reached“ which is displayed when the
reference orientation is reached can be assigned to a digital output. The message is
output on the following conditions:
Operation mode 2 (axle positioning) for parameter
Operation mode
458
is se-
lected.
The controller enable signal at digital inputs S1IND/STOA and S7IND/STOB is
switched on.
Start Positioning of Axle
37
is activated
.
The speed sensor monitoring is activated, i.e. operation mode 2 (error message)
for parameter
Operation mode
760
of the speed sensor monitoring is selected.
Operation mode 1004 or 1104 (quadruple evaluation with reference impulse) is
selected for the speed sensor input.
The
actual frequency
241
is smaller than 1 Hz.
The deviation of the current position from the reference orientation is smaller than
the
max. orientation error
472
.
The current position after
Start Positioning of Axle
37
is recognized by the frequency
inverter as follows:
During commissioning, after switching on the frequency inverter, a search mode
is performed for 3 rotations at a rotational frequency of 1 Hz in order to detect the
reference signal. As soon as the reference signal was recognized twice, the drive
is positioned to the
Reference orientation
469
.
If the motor was already rotating before axle positioning was enabled, the posi-
tioning to the
Reference orientation
469
is performed without search mode be-
cause the position of the reference point was already detected by the frequency
inverter.