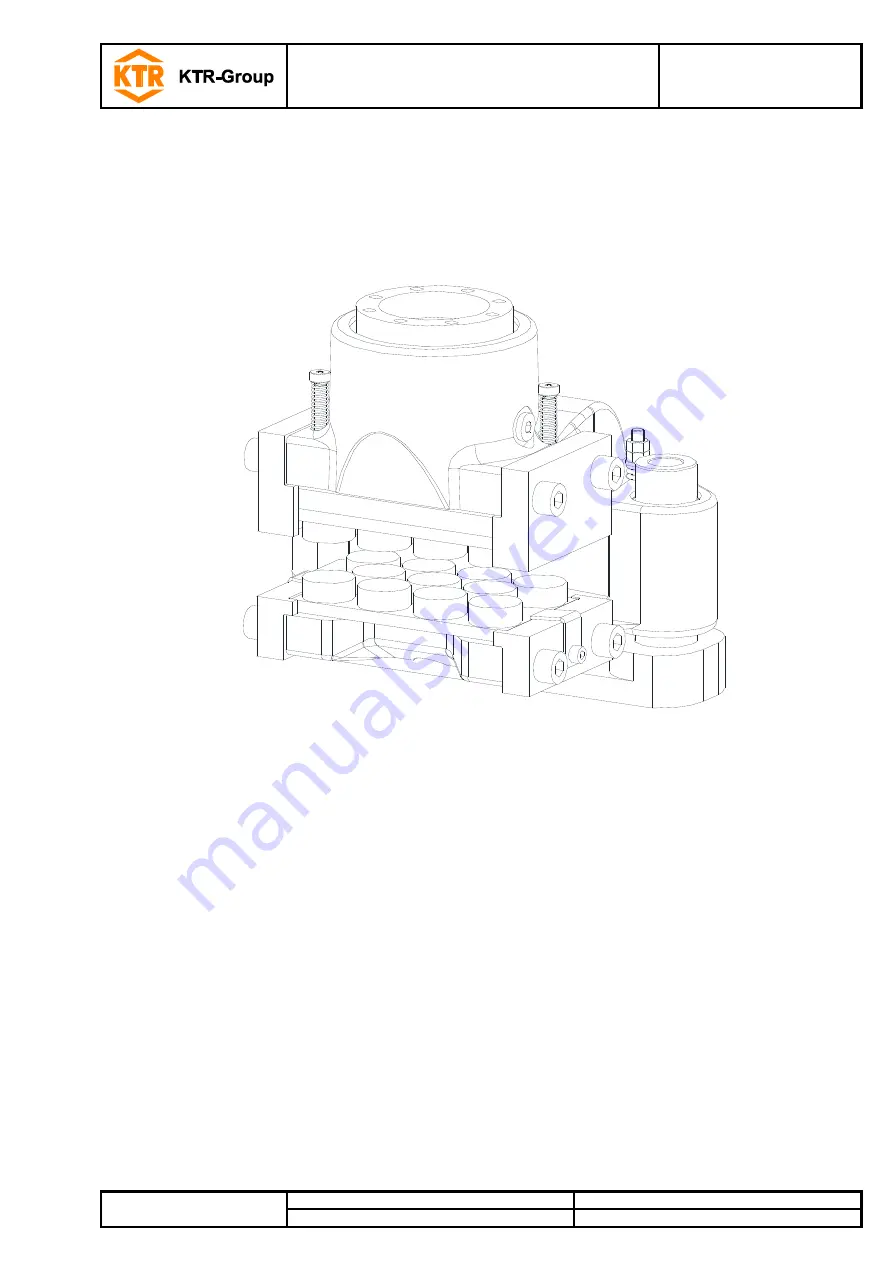
KTR-STOP
®
XS-xx-F B-xx
Operating/Assembly instructions
KTR-N
Sheet:
Edition:
44536 EN
1 of 25
3
Please observe protection
note ISO 16016.
Drawn:
2020-03-26 Shg/Wie
Replacing:
KTR-N dated 2017-12-19
Verified:
2020-03-26 Shg
Replaced by:
KTR-STOP
®
XS-xx-F B-xx
XS-xx-F B-xx is a spring-actuated brake in a floating calliper design serving to
generate a brake force on a brake disk in order to decelerate a plant’s movement
or stop it, respectively, or keep it at standstill.